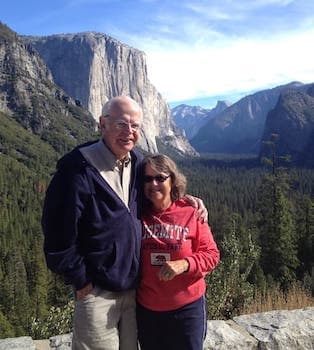
Curated with aloha by
Ted Mooney, P.E. RET
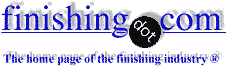
The authoritative public forum
for Metal Finishing 1989-2025
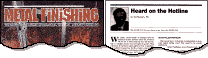
-----
Need coating to prevent galling between two aluminum surfaces
Q. I'm working on a project that requires two aluminum pieces to contact each other, not unlike a piston and its cylinder, heat is moderate (225 °F) , it's to be used only in emergency so longevity is not an issue. Both pieces are 6061, and economy is important. Parts are about the size of your thumb. Parts will be submerged in silicon fluid. Thanks for your help !
Ron MaddoxProduct Mfgr. - Medford, Oregon, USA
2003
A. I would try a moderate coat of anodize on both parts. Not knowing your tolerances or relative costs, it is not possible to suggest other possibilities like dry film lubrication --the baked on kind -- or a thin coat of EN or ?
James Watts- Navarre, Florida
2003
ACRONYMS:
EN = Electroless Nickel
Q. Thanks for the response James, my tolerances are very loose, in the .01" range and can be adjusted to accommodate any coating thickness. One of these surfaces will be TIG welded during the assembly process, so I would like to just coat the one side that doesn't get the weld. You mention a light anodize, how about a full hard coat type 3 anodize? What does EN stand for? I would be interested in the baked on dry film, where do I get more info? It's important that I get this right so I'm open to any ideas. Economy is important but it takes a back seat to being able to depend on the coating to work.
Thanks,
- Medford, Oregon, USA
2003
A. It is somewhat difficult to talk about a "best" solution when you cannot see the parts. I am a little gun shy of "silicon" so will exclude the dry film lube which would be the cheapest and possibly satisfactory if it was in air. My next choice would be one of economics. Either EN (electroless nickel) on the smallest part or anodize. A heavy coat of anodize should be all that you need. I do not see the need for Hard coat since the part will be infrequently operated and the silicon fluid should be an excellent lubricator. I would anodize (a heavy coat) the part that would require the least masking. It would be nice if that was not the welded part as the weldment will have a different color. With all of that said, are you sure that you need a coating.? If it is submerged in silicon fluid (oil) there should not be any galling.That is not so in air, so you would need to cycle it a couple hundred times to see if you really needed a coating. 0.01 is a very sloppy fit which may additionally reduce galling.
James Watts- Navarre, Florida
2003
Q. Thanks again James for your reply! I like the sound of no coating at all, I plan to do severe testing on these parts and will try the no coat to see what happens. I've had a local coating shop sell me on a dry film coating. It's a poly ceramic coating, a Benzene mixture. They make it sound like God's gift to man. You mentioned you were gun shy of dry films and silicon fluids, I thought silicon fluid was inert to everything, and very chemically stable. That's my reason for using it over a hydrocarbon based hydraulic fluid. I would sure like to hear more about why you would be gun shy of dry film and silicon. Any info you have to offer would be greatly appreciated!
Ron Maddox [returning]Metal Fab. - Jacksonville, Oregon, USA
2003
A. Dry film lube is a very generic term and there will be many definitions. My normal thought is Molybdenum disulfide. There are also some graphite based films. They are made into a suspension rather than a solution. Some can stay suspended for quite a long time. One analogy would to think of it like a paint. The liquid portion is normally an organic solvent. Then it will have a binder to "keep it together" when it is dried. The baked finishes are quite well stuck to the parent metal. It is very common to use a phosphate for better adhesion. We had excellent luck using a calcium modified zinc phosphate. Now, silicon covers a wide range of materials, again as defined by the user. Silicon does have the properties that you mentioned, but every now and then you will find that it has a strange effect on some materials. Not having any exposure to your intended use, I did not want to send you down a road that might lead to a long term failure where in the short term testing -it was OK. Now your vendor calling his a ceramic- is interesting. I would be a bit cautious and find out what it really was. He may have some totally different or new product that could be great. I always believe in testing over "hype".
James Watts- Navarre, Florida
2003
A. We process a co-deposit of Nickel w/ particles of P.T.F.E.(Teflon). It is utilized on wear components to provide self lubricity and corrosion protection.
Charlie Camenzind- Phoenix, Arizona, USA
2003
Suggested Dry Film Lubricant for Aluminum Piston
Q. I have a lubricant question. Due to proprietary info, let's assume I have a 1" diameter aluminum piston working against compressed air, with a 1" stroke at 1800 cycles per minute. Can a dry lube be used between the aluminum piston and the aluminum cylinder walls with indoor conditions (50 to 90 °F)? If not, what would be a good lubricant type and viscosity?
I know graphite cannot be used. What about Molybdenum Disulfide? Or, since it is a piston, would an oil/grease work better?
Thank you!
Materials Engineer - Wilton, Iowa, USA
August 10, 2015
A. Hi Mike. I don't think bare aluminum on bare aluminum is a good couple despite lubricants... but we appended you inquiry to a similar thread with a number of potential solutions, such as anodizing the piston or Electroless Nickel Plating it. Good luck.
Regards,
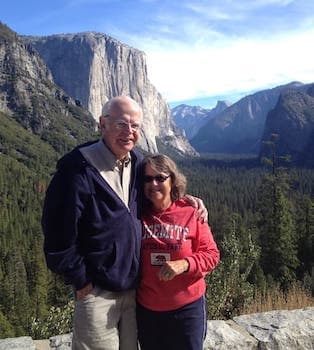
Ted Mooney, P.E. RET
Striving to live Aloha
finishing.com - Pine Beach, New Jersey
August 2015
Q, A, or Comment on THIS thread -or- Start a NEW Thread