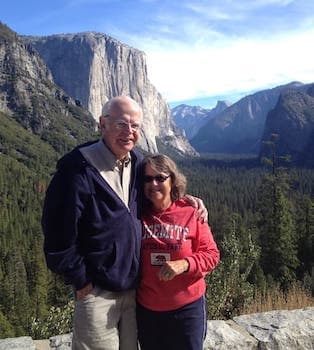
Curated with aloha by
Ted Mooney, P.E. RET
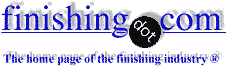
The authoritative public forum
for Metal Finishing 1989-2025
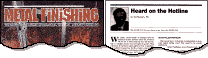
-----
Electroforming platinum or rhodium?
for Artisans, Jewelry, Crafts
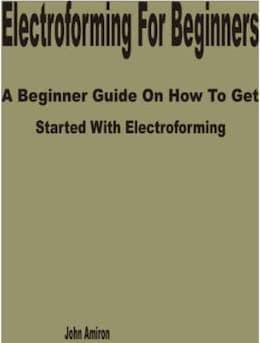
avail from eBay, AbeBooks or Amazon
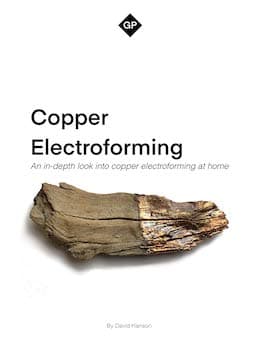
avail from Amazon
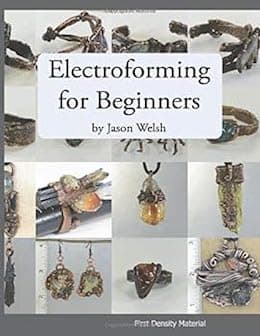
avail from Amazon
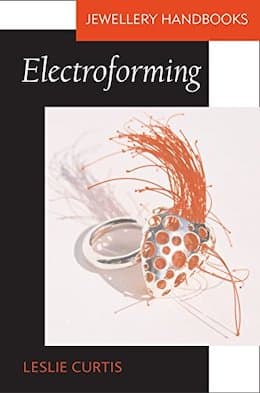
avail from eBay, AbeBooks or Amazon
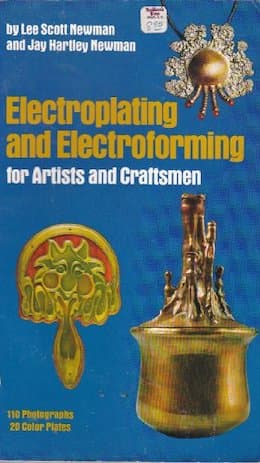
avail from eBay, AbeBooks or Amazon
(as an Amazon Associate & eBay Partner, we earn from qualifying purchases)
Dear Sir,
While browsing through the net on the above subject, I happened to see
topic 19652.
I would appreciate if you could please provide information on Platinum electroforming for jewelry application, or suggest a source from where this could be obtained.
Regards,
SN
- India
1998
A. The book "Electroforming" by Peter Spiro, 1971 does not address platinum and has one dated reference to a French paper.
"Modern Electroplating", edited by Lowenheim
[on
AbeBooks,
eBay, or
Amazon affil links]
has one reference to one solution plating to 0.5 mm. I suppose you could play with parameters and get a thicker plate.
It costs so much, most people would only electroplate a thin coat of platinum over a nickel or cobalt electroform.
- Navarre, Florida
Q. I would love to know how to produce stress free thick deposits of platinum.
Currently we are machining platinum bar to make inserts for nickel electroforms
We have evaluated many patents and not found anything suitable as have many other users. We are involved in a somewhat specialist market where the properties of platinum are a necessity.
There is a fortune available for anyone who can electroform thick ductile deposits of platinum. i.e 0.1 mm
1998
A. If it is not economically feasible to electroplate thick platinum layers, then I might suggest using a rapid vacuum vaporization method. If you have more info about the kind of parts, quantities and potential applications, I could help determine the feasibility.
Mandar Sunthankar- Fort Collins, Colorado
A. Bob:
I have plated several mil thick Pt deposits on .065" pins which have withstood 180 degree pinch bend test prior to any anneal/sinter. Very ductile. But you are right. There is a VERY tight band of plating parameters available for this process, outside of which the stress skyrockets.
Regards,
Dave
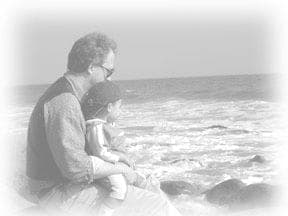
Dave Kinghorn
Chemical Engineer
SUNNYvale, California
A. Bob,
I would like to get a cut of the fortune. The PVD industry has been producing metal foils for years by depositing thick films on a mandrel and continuously stripping the film off the mandrel. Beryllium, Ti alloy and other metal foils are fabricated this way and I see no reason that platinum couldn't be formed the same way.
Society of Vacuum Coaters
Albuquerque, New Mexico
"Handbook of Physical Vapor Deposition (PVD) Processing" (2010) [on AbeBooks or eBay or Amazon affil links]
and "The Foundations of Vacuum Coating Technology" (2018) on AbeBooks or eBay or Amazon affil links]
Multiple threads merged: please forgive chronology errors and repetition 🙂
Q. I'm searching for micro tubing with a very high corrosion resistance. Is it possible to electroform platinum or rhodium tubing with an OD smaller than 0,15 mm and a length between 10 and 20 cm.?
Kevin van Dijckelectrochemical machining - Venray, Limburg, The Netherlands
2003
A. I hesitate to say that anything is impossible or even impractical, but to get a reasonably thick deposit of either, with acceptable properties in the way of stress and freedom from porosity sounds difficult. Any chance that gold would be sufficiently corrosion resistant? Besides being cheaper, the successful electroforming of those tubes from gold sounds a lot easier. Good luck.
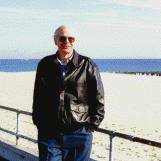
Ted Mooney, P.E.
Striving to live Aloha
finishing.com - Pine Beach, New Jersey
Use of platinum electroforms in jewellery?
Q. We are looking for information on the use of platinum electroforms in jewelry applications and would welcome any advice that you can give as to information sources.
Stefano Becattini
Jewellery - Santa Barbara, California, U.s.a.
2004
Q. Does anyone know: Is it practical to create sheet rhodium of about 50 to 100 microns thick by electroplating rhodium on one side of a piece of copper and then dissolving the copper in acid? Would the resulting piece be made smooth with good structural integrity?
I am interested in creating a general purpose rhodium anode and it seems that rhodium plating solutions are cheaper per gram than buying sheet rhodium. But it also seems that when rhodium is thinly electroplated onto something else it flakes off easily when used as an anode in corrosive solutions (due to imperfections?)
I know that Pt anodes are usually used. I want to study the resistance of Rh anodes.
Hobbyist, Chemist - Bothell, Washington
April 6, 2015
A. Hi Ansel. I suspect that if it were practical to electroform sheets of rhodium, then you wouldn't find the sheets as expensive as you feel they are :-)
You label yourself a hobbyist and a chemist, but you have some electroplating/electroforming experience, right? I only ask because, as they say, you have to crawl before you walk ... and you're asking about a very difficult plating operation where you'd probably want to rely upon significant prior experience.
I would probably make the mandrel from aluminum because it's a lot easier to dissolve than copper.
I don't think I agree with your notation that rhodium flakes off easily when plated onto something else though. Best of luck.
Regards,
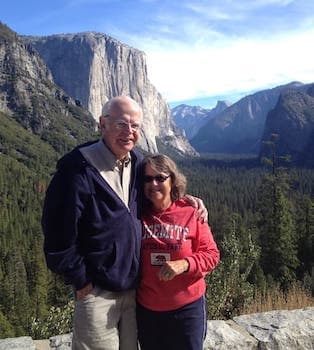
Ted Mooney, P.E. RET
Striving to live Aloha
finishing.com - Pine Beach, New Jersey
P.S.: I removed my suggestion about aluminum mandrels based on subsequent replies.
![]() |
A. About 55 years ago, Sel-Rex Corp patented and then started selling a stress-free proprietary rhodium plating solution called Rhodex. Sel-Rex is long gone but Enthone, Inc. now owns the old Sel-Rex formulations. I just found Rhodex still listed for sale on the Enthone website. - Nevada, Missouri, USA A. Hi Ansel ![]() Geoff Smith Hampshire, England |
Thanks Chris; thanks Geoff.
Regards,
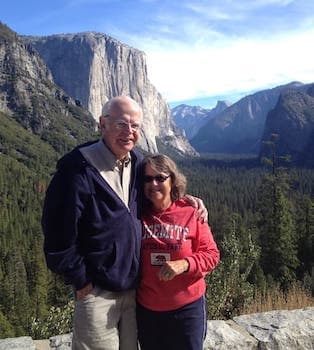
Ted Mooney, P.E. RET
Striving to live Aloha
finishing.com - Pine Beach, New Jersey
Q. Thanks Ted and to you others. Ted, to answer your Q about my experience with plating, I have done some plating. I discovered a new method of Ni-plating that works and provides a clean adherent coating (at least I have not found literature on it) -- consider it proprietary at the moment.
I have Rh plated silverware and I would not say it flakes off in normal use, but I see metallic Rh flake off when I use a plated piece as an anode- or even as a cathode. I can only speculate why. I wonder if it has to do with hydrogen adsorption- or in the case of anodes, perhaps there are flaws in the microstructure of the metal which allow the anodizing process to reach the substrate. I know that a Ni under-plate is recommended. This does not seem to prevent flake-off.
Thanks, if you know anything about this I would be curious to understand more.
Ansel
Hobbyist, Chemist - Bothell, Washington
Q, A, or Comment on THIS thread -or- Start a NEW Thread