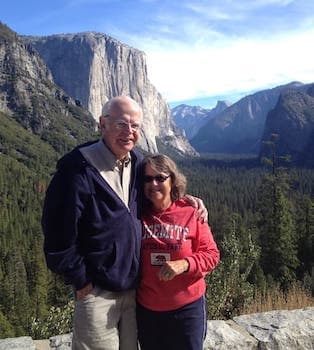
Curated with aloha by
Ted Mooney, P.E. RET
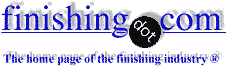
The authoritative public forum
for Metal Finishing 1989-2025
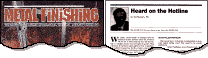
-----
Zinc-phosphate pretreatment of galvanized steel
2003
We have a number of paint and pretreatment lines at facilities around the world. Our products are indoor and outdoor sheet metal enclosures.
Metals used are aluminum, galvanized steel and stainless steel. I would like to clarify the detailed specification for the optimum zinc phosphate pretreatment stage for galvanized steel prior to powder coating, for outdoor applications.
Specifically, for the zinc phosphate stage, what is the recommended temperature, concentration, duration, method of application, and any other relevant parameters of this process?
Thanks
Mike Cross, APWelectronics enclosures supplier - Southampton, Hampshire, U.K.
2003
A. Hi Michael,
First let me ask you why you use galvanized steel in your product then you make a zinc phosphate pretreatment and powder coating for it? This method is not good in the quality and the cost because the galvanized steel not good in phosphate pretreatment (zinc or iron phosphate), it is used for steel. Zinc layer will make many problems in phosphate stage. The adhesion and surface quality of powder coating will be not good with these kinds of steel so you must make one method from two not more. First if you must use galvanized steel in your product so you must strip the galvanized layer then make zinc phosphate and powder coating (not recommended) or you change the galvanized steel to normal steel or EK2, EK4 steel then make zinc phosphate and powder coating without any problem. Let us talk about dipping zinc phosphate stages for this kind of phosphate use for normal steel by this sequence:
1- chemical degreasing tank (5-7% 60-80 °C, 5-10 min)
2- chemical degreasing tank (3-4% 60-80 °C, 5-10 min)
3- hot water rinsing
4- cold water rinsing
5- activation tank (to activate the surface before phosphate tank)
6- zinc phosphate tank 3-5 % 50-55 C 2-4 min; from time to time you must remove the sludge from the tank
7- cold water rinsing
8- passivate tank
9- cold water rinsing
10- hot air dryer.
All technical date according to your chemical supplier and data sheet, and quality of your steel (corrosion, more oils). Finally, for outdoor product you can use polyester powder
Thanks,
Aly Gomaa- Cairo, Egypt
Q. Sir, please mention chemical names in respective tanks then it could be complete.
Mohan KrishnaEfftronics - Andhrapradesh, India
May 13, 2018
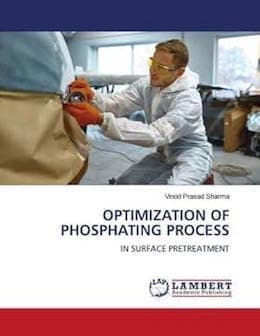
avail from AbeBooks, or Amazon
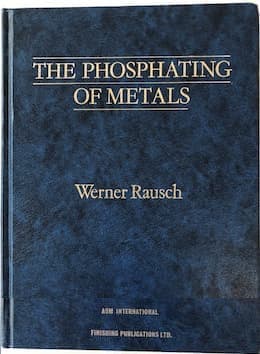
avail from eBay, AbeBooks, or Amazon
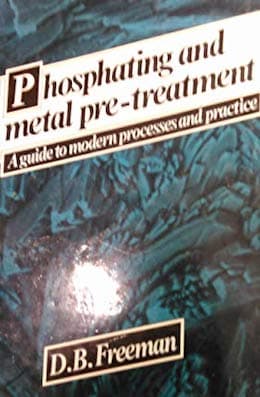
avail from eBay, AbeBooks, or Amazon
(as an Amazon Associate & eBay Partner, we earn from qualifying purchases)
A. Hi Mohan. I think you might have misunderstood Aly, but he suggested that you go to your phosphatizing chemical supplier with information about your steel (how much rust and what kind & amount of soils it has on it) and they will give you the list of their proprietary chemicals and operating conditions appropriate to it. There are numerous suppliers specializing in this, which you can find by googling for "zinc phosphate process supplies" including multinational companies like Chemetall, DuBois, and Henkel.
Is your application for galvanized steel or plain steel? If you want to make up your tanks with commodity chemicals (which most professionals do not do), you would need to start with a pretty deep understanding of the chemistry of zinc phosphatizing, not a list of some chemicals which sometimes work after a fashion under some conditions for some phosphatizing shops.
As an aside however, I disagree with Aly's premise that galvanizing plus phosphatizing has no place for powder coated materials. Galvanizing does in fact offer excellent corrosion resistance under powder coating for some applications, for example in rough service where the powder coating may get deeply scratched; zinc phosphatizing is required for proper adhesion between the galvanizing and the powder coating. Good luck.
Regards,
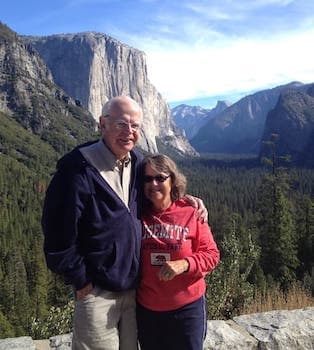
Ted Mooney, P.E. RET
Striving to live Aloha
finishing.com - Pine Beach, New Jersey

Q, A, or Comment on THIS thread -or- Start a NEW Thread