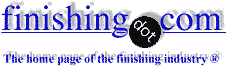
-----
Reducing stress in electroplated / electroformed Nickel film
2003
I have a problem with electroforming cantilever type structure by nickel on Cu seed layer. Electroplated Ni is bended after release structure. Cantilever size is 500 µm x 500 µm x 3 µm and we use Ni sulfamate bath because it has less initial stress than watt bath I know.
Sulfamate bath consists:
saccharine 4 g/L
Ni sulfamate 500 g/L
H3BO3 30g/L
NiCl2 20 g/L
Plating condition is: Anode Pt plated Ti net Temp 50 °C Current density 0.5 A/dm2 Mechanical agitation DC plating Cu seed layer is formed by thermal or sputtering.
Is it because initial stress of plated Ni?
If so, please let me know the way of reducing stress.
Any suggestions would be greatly appreciated.
student - Seoul, South Korea
-- first of two simultaneous responses
Make up a bath without the saccharine and try it. A normal make up of sulfamate will be around a +500 to +2,000 internal stress.
The amount of saccharine that you are adding is probably taking it to a -5,000 or worse. It takes testing with a contractometer to know where you are.
Stress tabs will give you a decent idea also and cost a lot less. Stress is quite temperature dependent.
You should be around 130 to 140 °F unless you have better data.
- Navarre, Florida
-- second of two simultaneous responses
You do not say if the bending is compressive or tensile. Your plating conditions suggest the nickel could be compressive stress, but your comments suggest it is tensile.
The 4 g/l saccharin should give you compressive nickel with a hardness of about 500 Hv, assuming no other additives are present, but the more important presence of chloride will give you a tensile deposit.
Why are you using platinised titanium anodes - it is much cheaper to use sulfur depolarized nickel and this will help keep your bath in specification. Inert anodes result in a loss of nickel from the electrolyte coupled with the possible oxidation of bath components.
Since you are using inert anodes, you do not need to add chloride; this alone will increase the tensile stress of a nickel deposit and is usually only used to assist in the dissolution of nickel anodes.
Furthermore, if you use SDP nickel anodes in a sulphamate bath, you do not technically need chloride present. However, many electroplaters and/or electroformers prefer to add about 10 g/l just to be safe.
I would also suggest you increase your boric acid to at least 35 g/l and preferably 40-45, especially with inert anodes. Your temperature is OK but you should be able to increase the current density to at least 2 A/dm2 without any real harm.
I would also suggest a filtration rate of 8-10 tank volumes per hour and, obviously, no in-line carbon treatment as this will take out your saccharin.
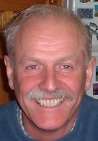
Trevor Crichton
R&D practical scientist
Chesham, Bucks, UK
Q, A, or Comment on THIS thread -or- Start a NEW Thread