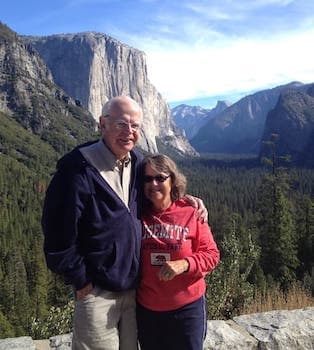
Curated with aloha by
Ted Mooney, P.E. RET
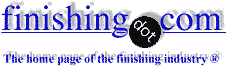
The authoritative public forum
for Metal Finishing 1989-2025
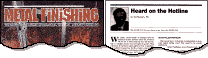
-----
How can I prevent stainless steel welds rusting in sea water
I have designed a trolley which carries diving equipment and stays on while the diver is underwater. It is made from 316 stainless steel tubing and has many welded joints.
The trolley was bead blasted to remove marks made by welding and also give a nice matte finish.
After 3 sea dives, all joints have become coated in a light rust.
Will pickling instead of blasting prevent this?
diving school - Bedford, Bedfordshire, United Kingdom
2003
Stainless steel welds need to have two things done prior to service in salt water environments: one is oxide/scale removal, and one is passivation. Mechanical methods like bead blasting or chemical methods like pickling are used for oxide/scale removal. Passivation is separate task, and should be done after descaling has taken place. Pickling uses a mixture of nitric acid and hydrofluoric acid, whereas the separate passivation step uses nitric, citric, or another oxidizing substance.
My recommendation would be to continue using the bead blasting for descaling, and then have the welded assembly properly passivated. Look into the newer citric acid treatments that are available (read some of the replies by Lee Kremer of Stellar Solutions [a finishing.com supporting advertiser]. The last thing to keep in mind is that 316 is not necessarily immune to corrosion in seawater. Type 317 or 904L have better pitting resistance and are used when long-term exposure is a requirement.
Automotive supplier - Michigan
2003
Toby is correct in all respects. One of the questions I had is what are you using for the bead blasting? Make sure that it does not contain any iron or is not used for blasting any iron parts prior to use on the stainless steel.
Is it a TIG weld? This is best for corrosion resistance usually. Salt water will eventually cause some corrosion on the welds, even if the weld was done correctly. The welding operation will change the alloy in the heat affected zone. If done correctly you should get more than 3 uses without rust. Also, you should be sure that they rinse the equipment well with fresh water after each use. This is normal procedure for any diver, so we assume that they are doing this.
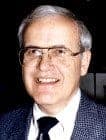

Lee Kremer
Stellar Solutions, Inc.

McHenry, Illinois
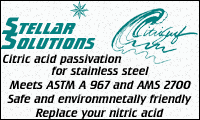
2003
Hi Terry,
Go and have a gander @ # 19760 in the archives.
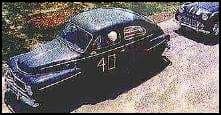
Freeman Newton [deceased]
(It is our sad duty to advise that Freeman passed away
April 21, 2012. R.I.P. old friend).
2003

this text gets replaced with bannerText
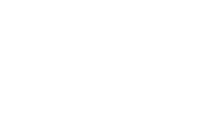
Q, A, or Comment on THIS thread -or- Start a NEW Thread