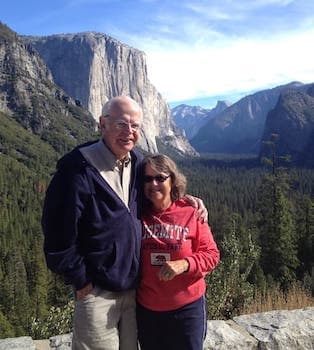
Curated with aloha by
Ted Mooney, P.E. RET
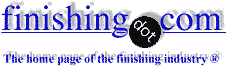
The authoritative public forum
for Metal Finishing 1989-2025
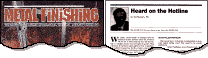
-----
Stripping aluminum deposits from Ti Impellers
I have titanium impellers with aluminum deposits melted on at high speeds. The titanium is 6AL4V. The aluminum is an abradable coating on the impeller shroud. It is a 12% silicon alloy with dispersed polyester, placed their by metal spray operations. When a malfunction occurs, the impeller can collide with the shroud, the aluminum is then abraded off and melts on to the impeller dues to its high rotation speed (+30,000 RPM). We've tried stripping this off with NaOH solution, it seems to work but doesn't fully remove the aluminum. Aluminum should dissolve quickly in this solution. Possibly a protective oxide was formed on the aluminum, blocking the affect of the NaOH, but this is the "cold" side of the engine. Any ideas on how to get rid of the aluminum without hand finishing or damaging the Ti? No acids - H2 embrittlement.
William B [surname deleted for privacy by Editor]repair and overhaul of commercial turbine engines - Phoenix, Arizona
2003
William,
I used a cycle consisting of the immersion in NaOH and a light glassbeading of the affected area to successfully remove the aluminum deposit. The customer was satisfied and there was no hand finishing required.
inspection services - Phoenix, Arizona
2003
What any of us think is worth absolutely nothing! You are working on engines regulated by the FAA.
You also must comply with the OEM's standard practice.
Free lance thinking must go thru your engineering department and meet all of the FAA requirements before there are any trials on other than permanently scrapped parts, by serial number.
- Navarre, Florida
2003
I'm sure that is very true, Jim, and sound advice. I would only extend it to say that while few parts are as critical as FAA parts, a plater needs to use caution about "freelance thinking" on many parts. If you are not the engineer who accepted responsibility for the soundness of a design, you may not know what is important and what isn't. Although few designs need as slim a safety factor as aircraft components, and few parts are as life-critical, there is always the possibility of weakening or contaminating a component, and the customer must know what you are doing on anything other than scrapped parts.
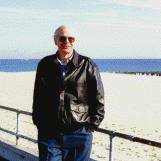
Ted Mooney, P.E.
Striving to live Aloha
finishing.com - Pine Beach, New Jersey
2003
2003
William,
Some feathers were obviously ruffled but I am sure that you know that any processing of aerospace hardware must be accomplished to certain standards and guidelines. You getting engineering approval was assumed in my response. I did this process for 10+ years for a Major, Prime Engine manufacturer in Phoenix. Assumption is that you will get engineering buy-off after experimenting with a scrap part. Also all appropriate metal testing will be done to ensure no weakening of the base material. I know that typically this process was done on impeller and impeller blades from test engines that had been destroyed (obviously) and that the removal was done primarily so that a clean surface could be obtained for penetrant testing.
Good luck,
inspection services - Phoenix, Arizona
The feathers were not really ruffled. The letter sounded like one that you might get from the production floor. Some places have people that want to "help" or make their job easier. I doubt it this letter came from any level of the company that was aware of FAA and OEM requirements.
James Watts- Navarre, Florida
2003
Q, A, or Comment on THIS thread -or- Start a NEW Thread