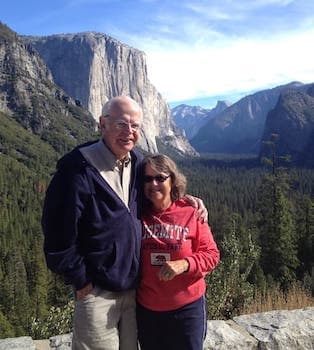
Curated with aloha by
Ted Mooney, P.E. RET
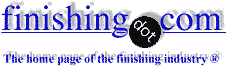
The authoritative public forum
for Metal Finishing 1989-2025
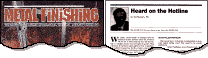
-----
High Temperature Nickel Coating for Carbon Steel
2003
Q. I was given a spec from
http://www.tcnj.edu/~rgraham/barrett/manual1-A.html.
This says that nickel plating is good to an operation temperature of 1100 °F, but when I contacted a local nickel plater, they told me that the nickel will become brittle at 600 °F and would not quote.
I am a buyer not a plater, so I rely on the expertise of my vendors.
We have carbon steel Belleville washers that need to withstand 650 °F operation temp.
What do you recommend?
heat exchanger mfgr & other skids - Houston, Texas
----
Ed. note: Sorry the referenced link is now broken.
A. I don't know about electrolytic nickel but electroless nickel will withstand that temperature. You may experience some yellow discoloration at that temp.
Todd Osmolski- Charlotte, North Carolina, USA
2003
![]() |
A. The steel industry uses heavy sulfamate nickel plate over copper (doped with Zirconium and Chromium) cooling flumes to start cooling molten iron just before it goes under the hot rollers. Surely that application is more severe than yours. ![]() Robert H Probert Robert H Probert Technical Services ![]() Garner, North Carolina ![]() 2003 A. Hi Liz, Switzerland 2003 |
A. Conventional brighteners are responsible for that embrittlement.
Sulfamate is the best option when high stress or temperature is expected.
Dull Watts nickel (no brighteners) can be a good compromise with price.
This is the same bath used by decorative plating except that no brighteners are added to it.
High carbon steel, fully hardened and exposed to heat and constant deformation requires an engineering coating.
Choose the finest specialized plater you can afford.
G. Marrufo-Mexico
Monterrey, NL, Mexico
Q. I have an application for a 36000 brass part that is going to be heated to 300 °C (572 °F).
The part needs a hard coat to protect it from abrasion and also for aesthetics, and it also has fairly tight tolerances, some dimensions are ± 0.0005".
I believe hard chrome would survive but may need post machining. What other plating would survive this temperature and how would the appearance change? I have some parts I can heat up to 'suck it and see' but would like to pre-empt the outcome if possible.
Would nickel chrome or even nickel plating survive?
- New Castle
March 22, 2013
A. Hi Peter. We appended your inquiry to a thread which explains that nickel plating is a good hard surface for this application. To my knowledge oven racks are nickel plated as a commodity item; I don't think your application will be a challenge. Good luck.
Regards,
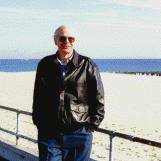
Ted Mooney, P.E.
Striving to live Aloha
finishing.com - Pine Beach, New Jersey
March 25, 2013
Q. Thanks for the response. The actual spec being proposed is "Electroless Nickel per MIL-C-26074 [⇦ this spec on DLA], Grade A, Cl 1". I think this should be fit for this purpose. I have read that it should be Grade B for copper based alloys, or is Grade A ok for Brass 36000
Peter Foster [returning]- New Castle
April 25, 2013
Color fading after heating Nickel plating
June 16, 2017Q. Hi,
Need your help.
We are doing Nickel plating (galvanic method) for one of our components (made of low carbon steel). Thickness around 6 microns. We are facing some issues on this.
After the plating the parts will be sent to a furnace for the assembly process.
The temperature at this furnace is around 870 °C and the parts will be in furnace for 45 mins.
Recently we are getting some green colour deviation on the top and bottom surface of the parts after the furnace test.
Do you have any idea on this?
Neelakandan MurugaiyanBuyer - Germany
A. Hi,
Try to do a post-treatment rinse in 1 percent nitric acid before heat treatment. I think it comes from the nickel solution. Can it also come from dirty rinses after nickel plating?
I never heard this before. Regards and please let us know.
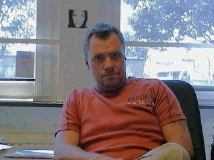
Anders Sundman
4th Generation Surface Engineering
Consultant - Arvika,
Sweden
July 13, 2017
Q. Hi,
Thanks for the feedback. I will try this method and write back.
But also is it nickel oxide (nickel burnt at higher temperatures). Or what is the color of nickel oxide or nickel after such high temperatures? Will it be black or green?
- Bamberg,Germany
July 16, 2017
Dear Neelakandan,
The greenish deposit is as result of insufficient current supply to that particular area caused by the insulative layer of base metal (carbon) or the overall contact issue.
Regards,
Parkunan
FREELANCE - SHAH ALAM, MALAYSIA
October 11, 2017
Q. I have copper Heater Blocks which are heating upto 325 degrees C. Which are used for plastic part heating. To protect the top layer I want do nickel plating on that. Will it withstand at that temp.
Please guide me.
Thanks for your valuable inputs..in advance
International Engg. Sol. Co.Ltd. - Bangkok, Thailand
August 8, 2017
Why did electroless nickel turn green when heat treated?
Q. Why colour turned green after heat treating the electroless nickel parts at 1000 °C?
During auto catalytic method, nickel metal is deposited over the pre-parts. Does the Ni metal contain any sulphate or chloride?
I've 15 years experience in Electroplating - Bangalore, India
September 1, 2017
Hi Chellappan. Please e-mail a photo of the defect to and tell us what the substrate material is, and whatever you can tell us about the processing conditions; high, low, or mid-phos, etc. Thanks.
Regards,
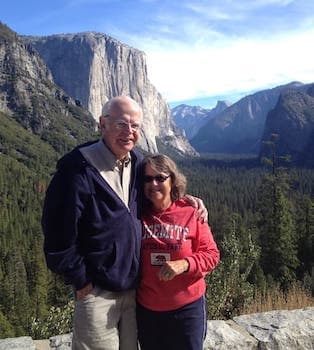
Ted Mooney, P.E. RET
Striving to live Aloha
finishing.com - Pine Beach, New Jersey
A. EN is heat treated for 1 hour at 400 °C.
It cannot withstand 1000 °C


Sara Michaeli
Tel-Aviv-Yafo, Israel
October 10, 2017
A. The melting point of Electroless Ni-P system should at 890 °C; at 1000 degrees it should have melted.
Peng liu- dongguan. china
November 24, 2017
Q, A, or Comment on THIS thread -or- Start a NEW Thread