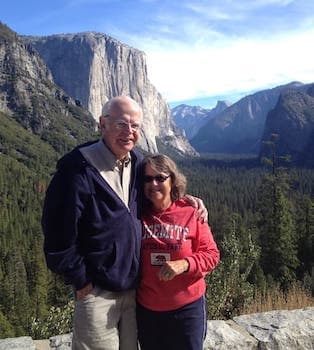
Curated with aloha by
Ted Mooney, P.E. RET
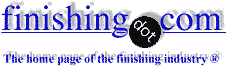
The authoritative public forum
for Metal Finishing 1989-2025
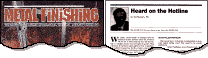
-----
Can a slightly harder part promote hydrogen embrittlement?
Hi,
I have a trunnion made of 1018 steel. There is a specification to
"case harden .003 - .008 deep to RC 43 - 53". We recently discovered that the case hardening was under spec. (47 @ .002, 41 @ .004, 28 @
.006, 92HRB @ .009)The plater is required to bake the parts within one hour for 4 hours. This has not changed. The supplier was asked to make the parts to spec. Now they are cracking at 110" lbs torque. The torque spec is 120" lbs min. and the parts can usually take much more. A picture from the lab does indicate voids between the grain boundaries.
Is it possible that the change has created a hydrogen embrittlement issue, or should we suspect that the parts were not baked properly and the harder part had nothing to do with it? Is this level of case hardening unusual in the industry?
Thank you for your interest,
metal forming - Chicago, Illinois
2003
Hi Kelly!
I must admit to some confusion. Is your 1018 part only being case hardened, or is it case hardened and then electroplated? The fairly common case harden callout you mentioned, "case harden .003 - .008 deep to RC 43 - 53", sounds like a carburize or ferritic nitrocarburize, either of which would give you a hard case, neither of which would cause hydrogen embrittlement. Are they cracked when you get them back from the heat treater / plater? A penetrate inspection, a common nondestructive technique, would tell you. Is the core hardness OK, or are they now through hardened? That would be hard to imagine with 1018 of any size, but perhaps your steel has changed, or perhaps your part is quite thin. I'm also not sure what you describe when you mention "voids between the grain boundaries". Carbide necklace, perhaps? Your heat treater could tell you for sure. True voids means something is pretty screwed up. The trouble is that I can think of a number of things that can go wrong, so I'll need more information to narrow the possibilities down.
Good luck, and write back soon!

Lee Gearhart
metallurgist - E. Aurora, New York
2003
2003
Thank you very much for your reply. Our steel is actually falling into the 1010 category and is .060" thick. After that it is formed into a trunnion (a sort of hollow "T" shaped part with ID .250") it is sent to heat treating. The parts are carbonitrided.
I recently found out that our supplier's heat treater was interpreting our spec as case harden .003" to .008" with surface hardness 43-53 HRC. We asked them to make the part so that the .003"
- .008" would have the required 43 - 53 HRC hardness. The heat treater began to make the parts so when measured at .008" we would have 43 -53 HRC.
The parts are then sent to the plater for zinc plating with yellow dichromate. The plater is required to plate and bake parts within 1 hour @ approx. 400 F to relieve the hydrogen. During use, inspection discovered that 50% of these parts were cracking at 100" lbs. to 136" lbs torque. (Spec is 120" lbs min). They are not cracked upon delivery.
The parts are not "through hardened". We do not have a specification for core hardness. Our problem is that we do not know if the change in heat treating (which essentially made a harder part) created the problem or if something got screwed up during baking at the plater to relieve hydrogen.
Is case hardening to this level, with this thickness of metal considered "too much" by industry? My reference to the "voids in grain boundaries" are in regard to the SEM photo we got from the lab showing the area at the crack.
I hope this makes things clearer. Please let me know what you think.
Thank You Much! Kelly
metal forming - Chicago, Illinois
hello Kelly,
I believe the material has varied carbon content from 0.10% to 0.18%. If you use proper 1018 material having carbon between 0.16% to 0.20% you will get a higher core hardness (about 30 hrc to 40 hrc) this will give you a much higher torque, and also it should be baked before yellow passivation to relieve hydrogen . In your case the part is breaking due to lower core hardness (lower strength). The question of breaking by hydrogen embrittlement is when you have a core hardness higher than 30 hrc.
forged fasteners - Mumbai, India
September 4, 2010
Q, A, or Comment on THIS thread -or- Start a NEW Thread