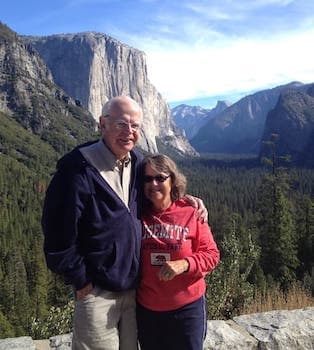
Curated with aloha by
Ted Mooney, P.E. RET
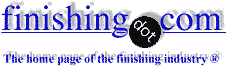
The authoritative public forum
for Metal Finishing 1989-2025
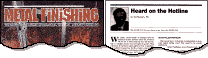
-----
Life expectancy of zinc passivation vs. coating thickness
Sir,
We use CRCA sheets of thickness o,8 mm to 1,6 mm, and once the components are manufactured, we do zinc yellow passivation with proper pretreatment and maintain 12 to 15 microns passivation thickness. But the material is assembled sometimes on coastal areas or sometimes on non coastal areas. There is a customer complaint that the material starts rusting in both the cases after 6 months
(approximately). Now we would like to know for 12 micron thickness of passivation what should be the life of passivation in coastal areas and in non coastal areas. Do we have any remedy to correct ourselves if unknown mistake we are doing. Or do you suggest any different type of metal coating? Why,if so? If pretreatment is done properly can tell us the life of zinc passivation for different thickness on coastal and non coastal areas. We await for your reply at the earliest.
Thanking you Truly yours,
Sheet metal fabrication - Bangalore, Karnataka, India
2003
Unfortunately it's probably impractical to answer how long 12 to
15 microns of zinc plating will last, even when the specifics totally detailed let alone when vaguely described, because the life will be very short and excessively variable. But this thickness (.0003 to
.00038 in.) of passivated zinc plating is probably inappropriate for any exposure to the elements.
Were this sheet metal galvanized instead of electroplated, the zinc thickness would probably be 3 to 10 times greater, and it would becomes more practical to estimate the life expectancy. The sheet metal should probably either be painted/powder coated after zinc plating, or galvanized.
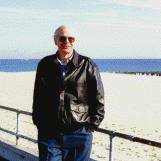
Ted Mooney, P.E.
Striving to live Aloha
finishing.com - Pine Beach, New Jersey
2003
Dear Mr. Sanjay,
I personally believe that 12- 15 microns should not rust within 6 months even in coastal India.
You are not getting your moneys worth or have no way of determining if you are actually getting the thickness.
The base metal is creating difficulties or the platers process is not working well enough.
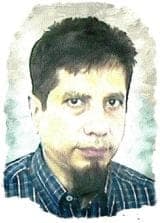
Khozem Vahaanwala
Saify Ind

Bengaluru, Karnataka, India
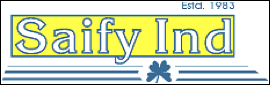
2003
Just to be clear on this, you are referring to outdoor exposure to the elements in coastal India, Mr. Vahanwala? You would know better than me, and I yield to your expertise--but I want to be sure I am not misunderstanding you. Thanks.
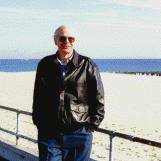
Ted Mooney, P.E.
Striving to live Aloha
finishing.com - Pine Beach, New Jersey
2003
2003
THE REASON FOR CORROSION IN COASTAL AREA IS DUE TO HIGH MOISTURE IN WEATHER.
KEEPING THIS IN VIEW THE PLATED COMPONENT SHOULD BE GIVEN HYDROGEN DE-EMBRITTLEMENT TREATMENT AFTER WHICH THE YELLOW CHROMATIZING SHALL BE HELPFUL IN PASSIVATING THE ZINC PLATING.ONCE HYDROGEN EMBRITTLEMENT IS DONE THERE IS NO ROOM FOR HYDROGEN IONS BEING ARRESTED INSIDE THE METAL. WHICH LEADS TO ABSORB sulfur DIOXIDE FROM THE AIR FORMING sulfurOUS ACID FORMING WHITE RUST AND THEN RED RUST.
HENCE ARRESTING HYDROGEN IONS IN THE ACID PICKLING BATH USING INHIBITORS AND HYDROGEN DE-EMBRITTLEMENT ARE ESSENTIAL FACTS IN CORROSION ENGINEERING.
chemical co. - India
Unfortunately Mr Sanjay has not given us details of what he makes and where it is used. We zinc plate parts for automotive companies from thickness varying from 5 to 15 microns, and I personally make it a point to look at our parts on older vehicles each time I'm near a coastal area.
Whilst I have noticed darkening of all thickness of parts in coastal areas on parts 2 up to 2 years and older, I have never seen rust within 6 months on even 5 micron parts.
Mr Sanjay obviously has plating thickness difficulties!
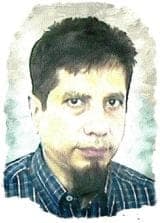
Khozem Vahaanwala
Saify Ind

Bengaluru, Karnataka, India
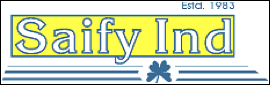
2003
Q, A, or Comment on THIS thread -or- Start a NEW Thread