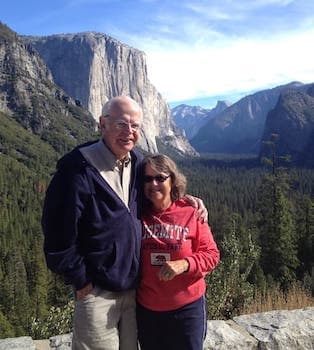
Curated with aloha by
Ted Mooney, P.E. RET
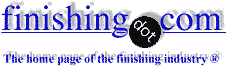
The authoritative public forum
for Metal Finishing 1989-2025
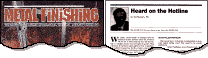
-----
Corrosion evaluation for LASER etched 904L SS
We are a pharmaceutical company that uses 904L stainless steel canisters as enclosure systems for a few of our products. We are looking to LASER mark (via Nd:YAG) the canisters with the lot/ batch number.
The material thickness is on the order of 480 microns. The typical etch depth, per a potential vendor, is ~50 nanometers, with marking "width" of 0.3 mm. No form of passivation will follow the LASER marking process.
My concern lies in whether corrosion will result at the point of etching. During its life, the canister may be exposed to temperatures and humidities up to 90 F and 80%, respectively.
I would appreciate any information that may be provided to allow me to determine whether corrosion may ensue for the laser marked 904L SS canisters. If corrosion is a potential issue, what measures need to be in place to passivate the SS?
Also, if any pertinent literature exists, please let me know.
Kamal NainaniPharmaceutical - Columbus, Ohio
2003
The laser etch area will probably be a corrosion problem for you under these conditions if you do not passivate it. The alloy that you end up with in the etch area will no longer be 904L, and there will be ferrites present.
You can easily passivate it with a citric acid based gel to prevent this. This can be applied only to the laser etch area to prevent immersion of the assembly. We have many customers doing this.
Let us know if we can help.
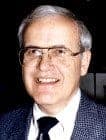

Lee Kremer
Stellar Solutions, Inc.

McHenry, Illinois
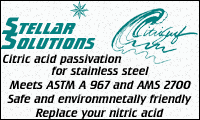
2003
An alternative is to use a laser activated chemical etching process avoiding any temperature induced changes in the machined area.
Peter Bradley- Switzerland
2003
Q, A, or Comment on THIS thread -or- Start a NEW Thread