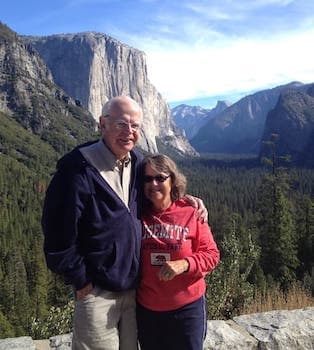
Curated with aloha by
Ted Mooney, P.E. RET
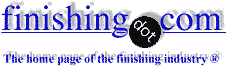
The authoritative public forum
for Metal Finishing 1989-2025
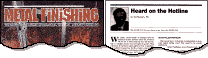
-----
CORROSION-RESISTANT BLACKENING PROCESS?
WE WANT TO BLACKEN CAST IRON AND MILD AND SPRING STEEL PARTS. WE CURRENTLY USE SODIUM NITRATE TO COLOUR THE MATERIAL BUT ACHIEVE A BLUE FINISH.
WE ARE LOOKING FOR BLACKISH FINISH ALSO THE SAME SHOULD BE CORROSION RESISTANT AS IT WILL BE WORKING IN MACHINERIES.PLEASE HELP US TO ACHIEVE BLACK FINISH.
-MANUFACTURING SMALL MACHINERY PARTS. - KOLKATA, WEST BENGAL, INDIA
2003
You should try cathodic electro deposited coating. It will give you 20 microns of dry film thickness which can sustain 1000 hours of salt spray test (astmb633.htmlb117.html" -->. It will give a semi glossy black surface.
adv.
For sample coating on your components, you can contact us. Hope this helps.
Mohali, Punjab, India
2003
2003
A PRE TREATMENT PROCESS SHOULD BE TAKEN CARE OF FOR CAST IRON COMPONENTS. A DESCALING BATH CONSISTING OF 200 GMS \ LTS OF caustic soda ⇦liquid caustic soda in bulk on Amazon [affil link] AND 20 GMS \ LTS OF POTASSIUM PERMANAGNATE SHOULD BE USED TO DESCALE THE CAST IRON AT 70 -80 °C.AFTER THIS THROUGH RINSING AND HCl ACID PICKLING WITH INHIBITOR AT 1% ON ACID VOLUME SOAKING FOR A MINIMUM PERIOD OF 30 MTS IMPROVES THE SURFACE. NOW KEEP 1% CAUSTIC SODA SOLUTION AT BOILING TEMP. 70 °C AND THEN GO TO THE BLACKENING BATH WHICH CONTAINS CAUSTIC SODA 650 GMS \ LITRE , SODIUM NITRITE , 200 GMS \ LTS SODIUM NITRATE 150 GSM \ LTS AND SODIUM CYANIDE 1 GMS \ LTS. THE TEMPERATURE SHOULD BE 135 - 145 °C WITH EFFERVESCES BUBBLING OUT IS THE RIGHT TIME TO INTRODUCE THE COMPONENT FOR BLACKING AFTER 1% CAUSTIC HOT DIP. DON'T WIPE OFF OR RINSE AFTER BLACKING ( OXIDISING ) . FINALLY APPLY DIESEL 25% + CUTTING OIL 75% DIPPING SHALL IMPROVE THE SURFACE TO GIVE A SMOOTH AND BEST FINISHING. THERE IS NO NECESSITY FOR THIS OILING BATH HEATING.
C PRAKASHAMchemical company - KOLKATTA, CHENNAI, INDIA
Q, A, or Comment on THIS thread -or- Start a NEW Thread