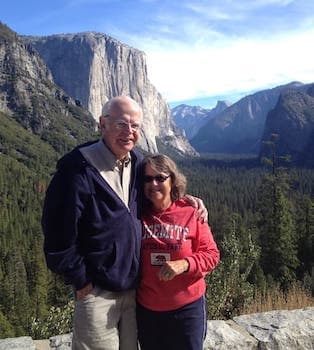
Curated with aloha by
Ted Mooney, P.E. RET
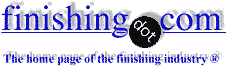
The authoritative public forum
for Metal Finishing 1989-2025
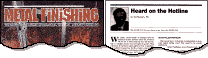
-----
Nickel plating is peeling off nickel
Q. I'm doing bight nickel plating in guns...but plating keeps peeling up like laminated on to my gun...can someone please help me, I'm doing electro Cleaning and surface activated and copper before nickel.
Hobbyist - Temecula, California
June 23, 2024
A. Hi Victor,
There are probably 101 reasons why plating may peel, and the necessary first step is to determine what layer is peeling from what layer. This thread is about the causes of nickel plating delaminating from nickel plating.
We appreciate the photo but due to background color, reflections, etc., I can't tell whether there is any copper color there. Have you looked at the underside of the blisters, and the remaining surface under the blisters, and determined that there is no hint of copper anywhere?
If there is no copper color to be seen anywhere in this blistered area, the problem is almost surely current interruption, which makes it time to tell us about your power supply and your racking or contact methods. But if there is any copper showing then this posting appears under the wrong topic and we'll move it before continuing :-)
Thanks & Regards,
Ted Mooney, P.E. RET
Striving to live Aloha
finishing.com - Pine Beach, New Jersey
⇩ Related postings, oldest first ⇩
Q. Hi guys!
I'm having some problems with my tiny caps, that go in to making of a fuse. The substrate is brass, plated with copper and then bright nickel. The nickel peels off over nickel. There is no break in nickel plating. The nickel portion remaining in contact with copper is very thin (2-10 microinches). The nickel portion peeling off is thick (100-200 microinches). If you have faced similar problems or have some knowledge about this please send to me your inputs. Thanks in advance for your valuable help.
Regards,
Pravin AagasheConsumer Electronics Mfgr. - Bombay, India
2003
A. You need to give more information about your nickel solutions.
You say that there is no break in the nickel plating - do you mean in the application of current or in the actual deposit?
If you are using two nickel layers and the first one contains any additives such as brighteners or levelers, this can cause poor adhesion of the second layer, unless it is adequately activated.
More information please.
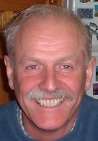
Trevor Crichton
R&D practical scientist
Chesham, Bucks, UK
A. Trevor's observations are correct. The most likely cause though is that there is a loss of electrical current or electrical contact during the plating process. This would lead to the nickel deposit becoming "passive" and any consequent nickel deposition would not be fully adherent.
Joseph Garnertrade platers - Corby, Northamptonshire, England, U.K.
![]() |
Q. Actually I am working in semiconductor company. I have many doubts in this fields, so please consider my questions & clear them. My questions are - India 2005 A. Hi, Lakshmanan. Regards, ![]() Ted Mooney, P.E. Striving to live Aloha finishing.com - Pine Beach, New Jersey |
Q. We have a process that we dip a rotating basket with brass pieces in a solution tank. Attached to the tank is a anode and cathode with a 9 vdc running at 90 amps. Our parts seemed to be getting a double plating and is flaking. Have any ideas what we can look at?
Thanks,
Paul Porter,Jr.Deland, Florida U.S.A.
2006
A. Are the parts "leaded brass" ? If so you require special service preparation. Clean-rinse-50% Fluoboric Acid -rinse -optional fluoboric acid copper plate -rinse - nickel plate.
The lead forms an insoluble in the regular acid dips normally used for plain brass (sulfuric or hydrochloric). The lead does not form an insoluble with fluoboric acid. So the acid dip change alone may help. However, the lead could also form an insoluble before it got plated in the slow plating barrel. When nickel plate bridges lead oxide - it peels. Ideally, you would first strike in fluoboric acid copper and then your nickel solution would not "see" lead because it would be covered by bonded copper.
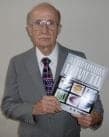
Robert H Probert
Robert H Probert Technical Services

Garner, North Carolina
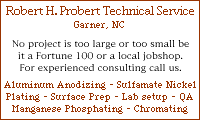
A. You give very little information about your process or conditions, so anyone answering is shooting in the dark. Firstly, what is the surface area of your parts; secondly, what type of nickel are you trying to electrodeposit; thirdly what are your conditions; fourthly what pretreatments are you using; fifthly, what is the brass substrate? Taking the caveat that we haven't a clue about your process, I can only suggest the following.
1) you have an intermittent cathodic connection resulting in a break in current and subsequent delamination of the nickel;
2) do a Hull cell test to make sure the nickel bath is behaving correctly;
3) ensure the plating bath is in spec as far as temperature, pH etc is concerned;
4) ensure your cleaning procedure is correct and in spec;
5) make sure your brass is not leaded - if it is you will see black streaks underneath the peeling nickel and on the brass.
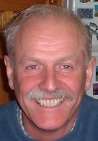
Trevor Crichton
R&D practical scientist
Chesham, Bucks, UK
A. Hi Paul. You've been offered a very good list of possibilities. But I would add one more. If the parts you are plating are very thin and light it is possible that instead of tumbling over each other and remaining in contact as they are supposed to, they are being conveyed to the top of the barrel and then fluttering down with contact broken. I have seen this broken contact cause laminar plating which peels -- the answer in that case was simply to seriously reduce the barrel rotation speed.
Luck & Regards,
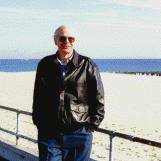
Ted Mooney, P.E.
Striving to live Aloha
finishing.com - Pine Beach, New Jersey
Bubbles in barrel Nickel plating
Q. Hi,
We are facing bubble issue in our Ni plating process.
The base metal is mild steel and we do semi-bright Nickel plating by barrel method.
The components are small in size like nails.
After plating we found lots of bubbles on the surface. As a part of manufacturing process, we send these components inside a furnace and after this also we found bubbles.
When we analysed, we found organic contamination could be a possibility, because when we did cut section, we found the bubbles are between nickel layers.
We prepared a new nickel bath without any organic additives (no brightener and no other additives) and the result were found to be good. But after few trials, we now see small bubbles again.
Could you please help to identify the root cause?
Thanks
Neel
Plating shop employee - Bangalore, Karntaka, India
July 20, 2016
A. Hi Neel. Laminar plating is usually caused either by organics (which you have ruled out), or by current interruption. Current interruption can be caused by a rectifier defect (which you may be able to check) or by make-and-break contact (which is an inherent part of barrel plating).
My suggestion, without seeing your plating line, is to try to reduce the speed of barrel rotation. This will allow the parts some additional opportunity to slide over each other while remaining in contact, as opposed to being swiftly carried to the top of the barrel and then have to swim their way back down to the bottom to regain contact. I have seen this suggestion work and would appreciate feedback whether it works for you. Thanks.
Regards,
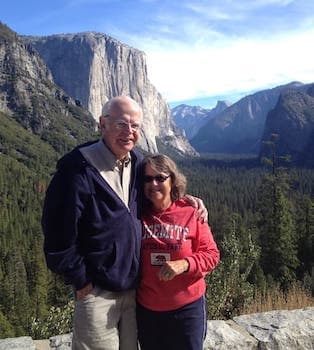
Ted Mooney, P.E. RET
Striving to live Aloha
finishing.com - Pine Beach, New Jersey
A. Hi Neel,
I agree with Ted. Try to maintain component contact with the cathode by adjusting the rotational speed of the barrel. Sodium lauryl sulphate as a wetting agent can also be helpful in aiding sliding of the parts. This is a high foaming surfactant and can cause foaming problems. So beware: add a little and wait to see the effect before adding more.
One further point: Nickel is more inclined to become passive and hence blister during breaks in electrical contact if the pH is high. I suggest running at a pH of 3.5.
Harry
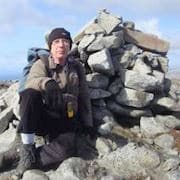
Harry Parkes
- Birmingham, UK
Thanks for your suggestion. Yes I will check this point and provide you feedback on your suggestion.
Also I will try to attach some pictures of the defect to understand this defect better.
Neel
- Bangalore, India
July 27, 2016
Tip: Readers want to learn from Your Situation 🙂
(little can be learned from abstract questions, so many readers skip them)
Q. How to calculate current running in tank in electroplating in ASF?
Ani sharmaNew in electroplating field - Baddi, India
February 4, 2022
A. Hi Ani. I am not sure that I understand your brief question, but ASF means amperes per square foot. It is a measure of 'current density', the total current flow divided by the surface area of the parts. For example, if the rectifier reads 80 Amps and the total surface area of the parts you are plating is 2 square foot, then the ASF = 40.
Luck & Regards,
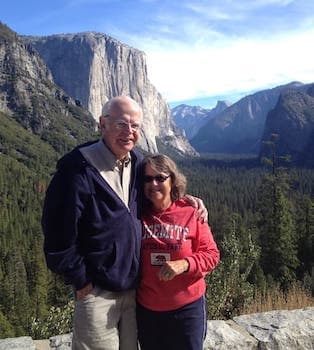
Ted Mooney, P.E. RET
Striving to live Aloha
finishing.com - Pine Beach, New Jersey
Tip: Readers want to learn from Your Situation 🙂
(little can be learned from abstract questions, so many readers skip them)
Q. Dear,
Kindly confirm for how many minutes of electricity failure during nickel plating can be tolerated, or what to do after electricity discontinuity on parts.
QA - Delhi
March 14, 2022
A. Hi Anil. Earlier on this page I related a case of defective nickel plated parts where there was no electricity failure, just extremely thin parts being barrel plated and fluttering down instead of remaining in contact because the barrels were rotating too fast. On the other hand, in duplex nickel plating there is an unavoidable electricity break in moving from semi-bright to bright nickel plating.
So I don't think there is an exact time limit ... rather the situation is that current breaks should be held to a minimum, seconds rather than minutes, so that laminar plating does not result.
Please tell us your actual situation -- what is happening or what you are planning but unsure about -- rather than posting hypotheticals. It is very difficult to suggest whether to strip the parts, not knowing what the substrate is or how critical they are (medical/aerospace vs. decorative), or to try to re-activate them, or whether to simply scrap them. If your follow up is shorter than my response, it's probably too short :-)
Thanks & Regards,
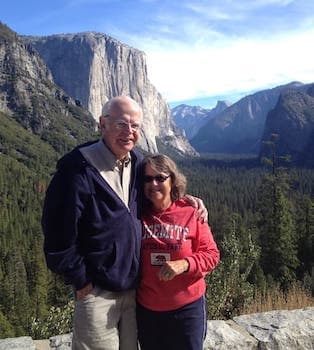
Ted Mooney, P.E. RET
Striving to live Aloha
finishing.com - Pine Beach, New Jersey
Q. Hi Mooney,
We are facing electricity failure (Discontinued) during Nickel plating at our supplier sometimes up to 5 minutes (Electricity again come after 5 min) parts in the copper tank or in Nickel tank currently we are scrapping as sometimes we face Ni peel off.
Kindly suggest for how may seconds / minutes of electricity failure (Discontinued) parts can be accepted where defect will not be there.
Head QA - Noida India
A. Hi again. All I can say is that current breaks are a well known cause of laminar nickel plating that peels off, and 5 minutes is a very, very, long time. It doesn't surprise me at all that the plating is laminated.
The Canning Handbook seems to suggest that if the current break is noticed immediately it might be possible to just etch the existing plating instead of having to strip it.
Other readers may offer their estimates of how long the power can be off, but for myself I think those current breaks absolutely must be fixed rather than asking precisely how terribly wrong something can be allowed to be before it must be fixed :-)
Luck & Regards,
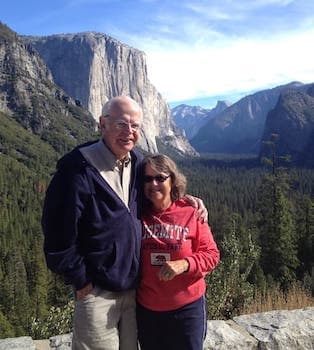
Ted Mooney, P.E. RET
Striving to live Aloha
finishing.com - Pine Beach, New Jersey
Q. Hi,
I am new in this plating industry and currently we are facing peeling of nickel over nickel. Only the ends and edges of holes of the second coat after shot peeling (at 0.014 A and 8 min) is peeling.
We also did shot peening to the first coat (stainless steel is the metal base) and peeling after shot peening was not observed, only for the second coat.
Both coats were plated with the same sulfamate nickel solution (pH = 4.7), 5 to 7 µm are the thickness of the coats. Have you ever plated nickel over nickel and then applied shot peening? What could be the cause of peeling of only the ends and edges of holes of the second coat after shot peening? How can we avoid this?
Thank you
shop employee - Lima/Peru
May 16, 2022
A. Hi K. The first problems is probably that you can't plate regular nickel plating onto stainless steel; you need a strike bath.
The second problem is that you shouldn't plate nickel onto nickel except immediately. Why is it necessary to do the nickel plating twice instead of once?
It's possible that the problem is worse at holes and edges due to burning or accumulation of brightener organics, etc., but I think the more pronounced problem at holes and edges is a canary in the coal mine rather than the specific problem to be addressed/
Luck & Regards,
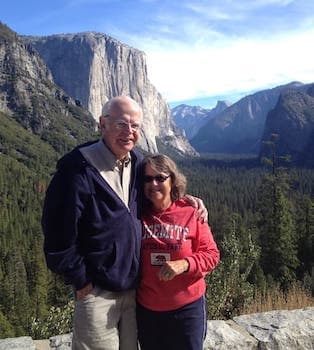
Ted Mooney, P.E. RET
Striving to live Aloha
finishing.com - Pine Beach, New Jersey
Q, A, or Comment on THIS thread -or- Start a NEW Thread