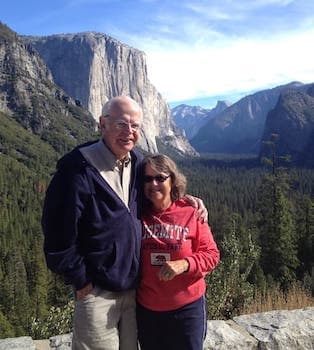
Curated with aloha by
Ted Mooney, P.E. RET
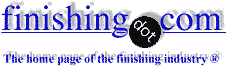
The authoritative public forum
for Metal Finishing 1989-2025
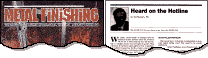
-----
Prevention of corrosion in steam boiler systems
1998
Q. I would be interested in more information about prevention of corrosion in steam boiler systems (including condensate and feedwater) and also in closed systems and cooling towers.
Tracy McConnellA. Corrosion protection in boilers and cooling towers is accomplished by monitoring the conductivity of the water. You might want to find a supplier of the chemicals, such as Garrett-Callahan. They could probably advise you, and maybe get you set up with the proper equipment.
Phil Pace- Tulsa, Oklahoma
1999
A. Tracy,
Contact the representatives of Nalco in Ontario. I am sure they can solve your problem.
Ling
Ling Hao- Grand Rapids, Michigan
1999
2000
A. Tracy, Steam boiler corrosion can be caused by numerous conditions some of which are:
I. BOILERS:
(1.) Dissolved Oxygen:--- Causing localized pitting
(2.) Scale: Mineral or chemical deposits)--- Can result in under deposit corrosion
(3.) Deposition of dissimilar metals:--- Can cause galvanic corrosion
(4.) Overfeed of Chelants and Phosphonates can also result in chemically induced corrosion in boiler
II. FEEDWATER:
(1.) The above can be associated with corrosion in feedwater systems also.
(2.) Low pH can also be a mechanism causing corrosion in feedwater systems. This is especially true if a high condensate return is combined with the use of an acidic oxygen scavenger such as sodium bisulfite. (3.)Erosion corrosion may be experienced in either the suction or discharge piping of the feedwater pump if cavitation is being experiences due to improper pump sizing or possible restriction in the piping.
III. CONDENSATE SYSTEMS:
(1.) The previous corrosion mechanisms can also be experienced in condensate return systems to some degree but the most prevalent type of corrosion is associated with low pH and/or oxygen.
(2.) The thermal breakdown of the alkalinity in the boiler results in the release of carbon dioxide. Since this is a gas it is transported with the steam into the system. Upon condensation, the carbon dioxide will form carbonic acid which will drop the pH of the unbuffered condensate. This acidic condensate will attack the return lines causing a characteristic trough at the bottom of the return line. The corrosion products will in turn be returned to the feedwater and can result in iron deposits in the feedwater tank as well as the boiler.
(3.) If the condensate return tanks are vented to the atmosphere, and don't have vacuum breakers, the cooling and pumping of the condensate can result in the addition of atmospheric oxygen into the condensate return system resulting potential for oxygen pitting corrosion.
These corrosion mechanisms can be addressed by a combination of mechanical and chemical means by an experienced chemical water treatment consultant.
George Nasse- Indianapolis, Indiana
Q. Hello
I need some information for deposit control in high pressure boilers (120 BAR) because now we use phosphate base control and we have deposit and it causes corrosion; if possible send me this information including related chemicals. Thank you.
With best regards,
saeid shahmohammadipetrochemical complex - Tabriz - Iran
2000
A. Hello Mr. Saeid:
Kindly be advised that the Phosphate/Caustic treatment for high pressure steam boilers is delicate and needs some backing of additional products. You should maintain the P2O5/OH- ratio 1/3 at total concentration of 15 ppm. In addition, you have to apply Morpholine and Hydrazine (Steam conditioner & Oxygen scavenger) at a level 5-10 ppm. This is providing good protection and smooth performance of high pressure steam boilers.
Sincerely,
Dr. Efraim Netivpetrochemical industries - Haifa, Israel
2001
2001
A. Saeid and Dr...
Actually for high pressure boilers especially at 120 bar, with a demineralized make-up water, coordinated pH/PO4 treatment is mainly for caustic corrosion protection. Again, the PO4 to sodium (Na) ratio is NOT 3:1 but should be between 2.2 - 2.8 to 1, best at about 2.5 - 2.6 to 1. Running at higher would increase the caustic corrosion as at higher caustic ratio, you'll be at the free caustic region. The pH of the boiler water should also be at 9.1 - 9.8 with PO4 level at about 6 - 12 ppm.
Deposition with demin. water is unlikely unless you have iron corrosion. This can be tackled using dispersants added into boiler.
As for oxygen control (obviously, elimination of oxygen would eliminate corrosion cell), dosage of oxygen scavengers such as hydrazine (suspected carcinogen) or hydroquinone, should be based on the residual dissolved oxygen level - below 5 ppb in the boiler make-up water is acceptable.
If steam is being condensed, at the point of condensation, the pH would be low due to the presence of carbonic acids (from the CO2 in the steam). This would drive the pH down and will cause corrosion in the condensate lines and equipment. The best way is to use amines to neutralize the pH and further bring it up to at least above 8.8. The feed rate would be targeted to get pH of above 8.8 in the condensate water.
Boiler chemical treatment is tricky and can SERIOUSLY pose damages to boilers and subsequent equipment. You should get advice from chemical specialty company in this field, such as GE Water and Process Technologies (formerly known as Betz).
Regards.
Gansad- Malaysia
A. There are some questions [and responses] about boiler corrosion. (Mc Connell 1998, Pace 1999, Hao 2000, Nasse 2000, Saide 2001, Netiv 2001, Gansad 2001). In the discussions no attention has been given to the corrosion resistance of the carbon steels. I did a lot of corrosion research on boiler corrosion and erosion. Of course, for an existing boiler you cannot change the carbon steel quality but in case of failures you can do something. Besides for existing boilers you can get a feeling of the corrosion sensitivity of the boiler if you analyze samples of the failed tubes.
Best regards,
W.M.M. Huijbregts- The Netherlands
2001
A. There shouldn't be much concern of corrosion on steel if the surface is clean, low levels of dissolved oxygen and no critical excursion in causticity or acidity.
There is also a test called Deposit weight density test of boiler tubes, to see over time the weight of corrosion products and deposition per unit area on tubes. This is destructive to the specific tube but can save the plant before waiting for accidental tube ruptures (before tube metallurgical analysis can be done).
Regards,
Gansad- Malaysian Borneo
2001
A. Dear Mr. Saeid Shahmohammadi,
If you use a phosphate stabilizer to boiler feed water then you should not face a calcium phosphate precipitation. Such phosphate stabilizers are polymers with good dispersency performance on Iron oxides , Ca and Mg compounds as well as Silica.
Kind regards,
Borzooyeh Saki- Tehran, Iran
2002
A. To minimize deposition in your high pressure boiler, please ensure to maintain the below recommended water characteristic of your boiler operating at 120 bar:
Feed water: Demin water with pH 8.5 to 9.5, total hardness should be ND (not detectable.
Boiler water: Na3PO4 (Sodium Phosphate) 3 to 10 mg/li or 5 to 15 mg/li as PO4- (phosphate), caustic alkalinity 5 mg/li as CaCO3, total dissolved solids 100 mg/li max., chloride 5 mg/li as Cl- max.
I hope this would help.
water treatment - Dammam, Saudi Arabia
March 7, 2009
Q. Dear readers,
I want to know the analysis of Gas CO2 in Demineral. Water? The responder can tell about the Method of analysis, from ASTM Method we recommended. Thank you for your attention.
Yours sincerely,
Said Iskandarfertilizer - Palembang, Indonesia
2003
Q. My boiler header have reducer in size & (5) elbow & expanders in the pipe size near the fixing in steam header; all of this in (6) m long pipe. My boiler has tube corrosion nowadays.
K-al-Shammry- Riyadh, Saudi Arabia
2004
Q. How will be calculate the dissolved gas % in boiler water as well as feed water?
k.dhakshinamurthy- Chennai,Tamil Nadu, India
2005
Q. I would like to know about the prevention of the following in a Y-160 Babcock and Wilcox boiler (w.p. 37 Bar, 02 drum, natural circulation, superheat control):-
1. internal corrosion - inside the tubes causing pitting,scab pitting,galvanic corrosion, crazy cracking of tube, thermal corrosion, etc.
2. external corrosion - in uptakes, economizer, externally in tubes.
Mumbai - India
2006
April 7, 2008
A. Dear Harsh In order to ensure reduction in the boiler corrosion, following aspects are very important
(a) Use of correct water, as specified by the OEM
(b) Use of correct grade of fuel and additives if any recommended.
(c) Ensuring correct PH value and salinity in side a boiler.
(d) Slow initial steam raising process, which is generally accelerated for timely steam requirements.
(e) Preservation of boiler Not in use is the most important and often neglected part.
(f) Correct amount of additives for dousing and the proper flushing through of the residual sludge will ensure greatly reduced pitting inside and proper cleaning of the tubes outside will ensure lesser carbon deposits, hotspots and thus reduction in pitting.
The economizer areas are generally more sensitive to acidic corrosion and this is more prominent in the initial steaming conditions when the flue gases are are lesser in quantity and they are at low temperatures by the time they come in contact with the economizer elements. This causes sulfur in the fuels and moisture to produce acid and the deposits cause the damage.
The bends and the weld seams are also more susceptible to corrosion as the depositions are higher in these areas and also the stress concentration is far more than in the straight tube part.
Since galvanic corrosion is more to do with initial selection of material for boiler erection, I would not dwell much on this.
Hope I have partly answered your question.
- New Delhi, India
Q. Hi
In our power plant, we use hydrazine to reduce corrosion but we have a proposal to change hydrazine to carbohydrazid. We want to know if it is possible or not?
- Iran
August 13, 2008
April 21, 2017
A. Dear mrs Sahar Taghi pour
REACTION:
N2H4+ O2 => N2+ 2H2O
DECOMPOSITION REACTION:
2N2H4+ HEAT + 2H2O => 4NH3+ O2
CONTROL LIMITS:
RESIDUAL N2H4 AT ECONOMIZER INLET Hydrazine
Hydrazine
ADVANTAGES:
1-DOESN'T CONTRIBUTE TO TDS
2-TRUE RESIDUAL TEST
DISADVANTAGES:
1-POOR REACTIVITY WITH LOW TEMPERATURE
2-EXPENSIVE COMPARED TO SULFITE
3-SUSPECT CARCINOGEN
4- REQUIRES SPECIAL HANDLING / FEED EQUIPMENT
5-DECOMPOSES TO NH3 WHICH CAN LEAD TO COPPER CORROSION
Carbohydrazide
Indirect reaction
(N2H3)2CO + H2O =>2N2H4+ CO2
2 N2H4+ 2 O2=>4H2O + 2 N2
Decomposition
(N2H3)2CO + H2O =>2NH3+ N2+ H2+ CO2
1 ppm Carbohydrazide liberates
15 ppb NH3
14 ppb CO2
The results indicated the suitability and efficiency of Carbohydrazide oxygen scavenger as an alternative to hydrazine in SWCC high pressure boiler provided the concentration of residual hydrazine (decomposition by-product of Carbohydrazide) is maintained at levels between 30-40 ppb in the feedwater.
- No harmful degradation by-products were found.
- Carbohydrazide was found to be a good oxygen scavenger at a concentration dose rate of0.7 ppm.
- Optimized dose rate resulted in maintaining the boiler chemistry with in design limits.
palayandeh AB - Tehran, Iran
Q. Dear Sir,
We have two high pr. boilers and want to preserve them for eight months.
Last year we did it by filling the water through hydrazine and not measure anything during the preservation; it is right or not?
Please update the right practice for that.
Rakesh
- kota, India
March 26, 2009
A. Dear Rakesh,
Always Check pH, Silica, Conductivity, Total Hardness before entering any types of water in Boiler & pH should be maintained by adding morpholine (as per pH 8.5-9.0)
Regards
- MP
April 2, 2010
March 27, 2011
Q. Dear sir,
My plant is fuel oil thermal power. I am chemically treating boiler water.
I have a problem I want to ask about. pH of make up water for boiler (economizer water) this is low standard is 9.0. Should we increase NH3 or N2H4 to increase pH of boiler water?
I want to know limit of NH3 and N2H4 in corrosion of boiler?
Please give recommendation to solve this matter?
Best regards,
Kiet
chemical engineer - Vietnam
Q. Dear sir,
I am a mechanical engineer and I am sailing in tanker ships for last 4 years. During this time I found in my ship when I use to collect feedwater for testing the pH and other test. I found the boiler feedwater to be red in colour. I use to give blowdown to the boiler. The scumb as well as the bottom blowdown, but didn't find change. Please tell me how can I make the water colourless. How much blowdown shall be made.
employee - MUMBAI INDIA
September 20, 2011
A. Dear amit sawant,
Red feed water could be caused by too much oxygen in the water. Please check your de-aerator. Oxygen should be taken out in deaerator. Keep steam pressure 0.1 bar in the de-aerator.
Hopefully it helps you.
electro mechanical engineer - jakarta, dki, indonesia
April 27, 2012
Q. Dear Sirs,
I have a steam boiler CFB type. The steam is to be used to drive a turbine generator. Physically check the piping, steam drum condition seems to be already corroded due to no maintenance during construction time. It will be cleaned by chemicals according to manual prior to test run. Any ideas how to check (on the spot) or is there any equipment or test kit available for testing the concentration of HCl, phosphate, ferrous/ferric ion?
How do we judge that the cleaning time has been enough and the result is ok?
Best regards,
- jakarta, dki, indonesia
April 27, 2012
Q. For how long the DM water filled non-drainable parts [Platen super heater and reheater] of newly erected high pressure utility boiler [158 kg pressure] can be kept safe without using any of the boiler preservation techniques?
Kalwinder Sran- Bathinda, Punjab, India
May 3, 2012
Q. Is it possible for any stainless steels to survive corrosion under steam at around 1500 °C? And if so, how long? Thanks...a graduate student.
Ed Mausolf- Las Vegas, Nevada USA
May 7, 2012
Q. Sir, I am a chemist in a sugar mill. Last season we faced a problem. Our semi kestner condensate pH found 4.5 to 5. Therefore feed water pH was also down. So please study our problem and answer me.
Bhaskarpatil- Madhya Pradesh, India
July 4, 2012
Q. Dear Sir,
I'm working as a Boiler operator with Guddu thermal power station Pakistan. Our Boiler is super critical water tube boiler having steam generation capacity 680T/h ,boiler drum working pressure is 150 kgf/cm2. Sir how much time I can put it under weight preservation? waiting for your valuable answer sir. thanx
thermal power station - Guddu.Kashore Pakistan
September 27, 2014
Corrosion of new boiler in operation
Q. Dear All,
My newly installed 5 Ton boiler is giving dark brown blow down water.
We have done an alkaline chemical wash in the beginning. Then we drained the chemicals and started the regular chemicals with Phosphate, Sulphite, and alkalinity builder. Yet boiler blow down is still dark brown.
Our chemical supplier is recommending to change sulphite to hydrazine. Will this rectify the boiler corrosion issue?
Nimesh N [last name deleted for privacy by Editor]- Sri Lanka
January 17, 2016
A. Hi Nimesh.
I look after a boiler and we add a protective chemical mix to ours.
The solution is brown in colour, having tannin as one of the chelating ingredients. When we analyse the water from the boiler, part of the assessment of the state of the water is the fact that the water is brown in colour, If it looks like murky tea, or here in the UK a pint of bitter, (warm beer) then the dosing is about right. So depending on the type of boiler dosing chemical this is not necessarily a problem. The scale that builds up in boilers tends to be brown anyway. So as long as the pH of the water is around 12, the TDS is about 2000 to 3000 ppm and the caustic alkalinity is around 800 then all is well. If you are still concerned, you can always get the inside of the boiler inspected by a qualified and registered expert to check for cracks, or thinning of the fire wall or tubes. He will be able to put your mind at rest.
Also as you say it is a new boiler, so it should be fine.
But be certain with an expert on site opinion.
Best regards
- isle of Man Great Britain
January 18, 2016
October 13, 2016
Q. Dear Sir,
We have a low pressure fire tube boiler, We are Getting Very Red colour blowdown water. This red colour is getting after We did the cleaning of Boiler with Hcl cleaning.
The procedure is like this
1) Shutdown the boiler and Next opened the top cover , then poured chemical solution Name is Universal chemical (UC55),
2) After closing the Man way started boiler and Heated up slightly,apprx 70 degree centigrade.
3) Then shutdown the boiler and leaved for 8 hours,
4) then opened the blowdown valve, Drained all water and also opened the bottom man way , Removed some scale where ever possible, then flushed the boiler drum inside with Raw water.
5) Then closed top and bottom manway ,Started boiler.
6)From that day onwards we are getting Very red Colour, Before chemical cleaning we got only light pink colour water, but now getting very Red or may be it looks like Dark brown colour,
So pls help us to Solve this problem.
Here Feed and blow down water samples are attached
Feed water : pH 7.5, Hardness 16, PO4 0.50, conductivity 8.3
Blowdown pH 11.8, Hardness 144, PO4 180, TDS 1792.
Fertilizer ltd - Visakhapatnam,Andhrapradesh, India
Q, A, or Comment on THIS thread -or- Start a NEW Thread