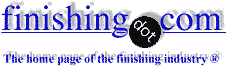
-----
Technology for consistency in very small batch aluminum anodizing
Q. Part of my company's business is involved in fabrication of precision metal components that are then anodised, either black or natural. Our requirement is for an extremely high degree of finish. Our supplier who is very experienced in all facets of anodising, says we are pushing the boundaries. We only require small volume runs, <50 piece, but on regular basis. All batch finishes have to be identical. There in lies our problem of small run size, but consistency between runs is critical (in terms of colour etc).
We have heard that there are "small" anodising plants / equipment available that are ideal for low volume anodising.
The principle of operation is along the lines of an automatic washing machine?
Can anyone throw any light on this topic or point me in the right direction re. people to contact.
For the record, our current supplier is fully supportive of our endeavors and will be assisting us with the technical aspects of running the plant.
Kind regards
Crichton Manson- Christchurch, New Zealand
1998
1998
A. I saw a couple of things that you might be referring to at a Sur-Fin trade show a couple years ago. One was a barrel that pumped the liquid to a small unit, flushed and added the next liquid. It was for barrel plating small (tiny) parts. Anodizing does not lend itself to this type of barrel use.
Another was a remote unit that stored solutions and rinse waters. By reuse of rinses, it saved water treatment.
Neither were truly automatic as they were displayed.
I am a puritan of the old school. To my way of thinking, nothing beats a single tank per solution/rinse. Pumps are a pain (eventually) and the piping is a source of breaking unless great care is taken, such as double piping.
In the USA, rotationally molded tanks ar moderately priced and readily available. It takes up more sq. ft of shop space, but is significantly less prone to cross contamination and other problems of a pumped system.
On a tiny system, pumped spray rinses will not save the money that adding an extra rinse tank per process rinse will (dollar for dollar spent)
A chiller is the mandatory part of hard anodizing and its temp control has to be excellent. On a small system, you might be able to afford a pulsed power supply. Set with the proper operating windows, they are effective. They cost significantly more than a plain old DC power supply, and not many folks are prone to give up values for the windows. If you spent several hundred hours developing the optimum, would you give it away.
Anodizing, especially hard anodizing, is not a "dip it" process for consistent quality and production. Equate it to maintaining machining tolerances to 0.00005 and concentricity to 0.00002 on a turned part with 8-10 different diameters. Once yo figure out how, it is a piece of cake ('til the alloy changes)
James Watts- Navarre, Florida
Q. Dear Sir/Madam,
I would like to request you to please help me to learn about ALUMINIUM ANODIZING.
Bast Regards,
- Dhaka, Bangladesh
November 15, 2010
Treatment &
Finishing of
Aluminium and
Its Alloys"
by Wernick, Pinner
& Sheasby
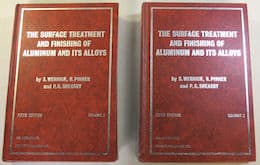
on eBay or Amazon
or AbeBooks
(affil link)
Hi, Sayedur. You can start with our "Introduction to Anodizing". The most complete and authoritative guide to everything involved in anodizing is the 2-volume book, "The Surface Treatment and Finishing of Aluminum and its Alloys". Hopefully this will be available in a library in Dhaka.
A good and practical guide is Probert's "Aluminum How To", although you would probably have to buy that one since I doubt that you will will find it in a library in Bangladesh. Good luck.
Regards,
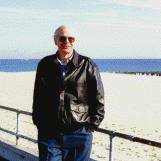
Ted Mooney, P.E.
Striving to live Aloha
finishing.com - Pine Beach, New Jersey
Q. I have successfully run type-2 and am approaching type-3 on a scaled down 2-3 sq.in. sample size in a sulfuric acid electrolyte. My tank uses 1/2 gallon of electrolyte, sits in a 15 gal bath and I can achieve current densities on the order of 100A/sq.ft. My chiller can hold the bath at 40-44° with aggressive agitation and the tank which is approx. 3" dia x 2' vertical is fitted with a bottom aerator, plastic mesh tube, and aluminum foil wrapped cathode. I have achieved heavy type-2 layers under extended process time with commensurate loss of part thickness at a 50 A loading. I believe I only need to fine tune my electrolyte mix to get satisfactory hardcoat. At this time I do not have to meet milspec but that may be a future consideration.
At this point I suspect the 40° limit of my chiller's controller is hampering my efforts. Realizing that oxalic hardcoat allows higher processing temperatures I want to see what kind of results I can get with a mixed bath of sulfuric and oxalic. I would like to raise the bath temp into the 45-50 °F range.
The chemistry of the bath is probably my greatest challenge. For ready availability I am using common chemicals in low volumes: battery acid
⇦ on
eBay
or
Amazon [affil links]
for the sulfuric and wood bleach for the oxalic. Up to this point I have been using a concentration of 2:1 BA to distilled water. I realize this is probably a bit strong but I have had trouble finding any reliable information to use in calculating the actual concentration. I would be happy with a decent approximation at this point.
I suspect that adding 1-5% oxalic acid will allow me to raise the process temperature into the desired range and the color change is not a hindrance at this time. So in the absence of any sort of guidance I have determined that an electrolyte of 1 quart BA, 1 quart distilled water, and 1-1/4 tablespoons of wood bleach
⇦ on
eBay or
Amazon [affil links]
might be a good starting point using a loading of about 50 A/sf. That should give me a concentration of 1% oxalic by volume (0.75% by weight) and and unknown concentration of sulfuric, but dead in the middle of the conflicting recommendations that I have seen, anywhere from 2:1 to 1:2.
It would be great if I could fine tune the mixture before mixing this batch and would greatly appreciate any suggestions. I want to get some acceptable results here before considering scaling the process up to small batch production levels.
Jim
- Florence, Kentucky, US
November 18, 2012
Q, A, or Comment on THIS thread -or- Start a NEW Thread