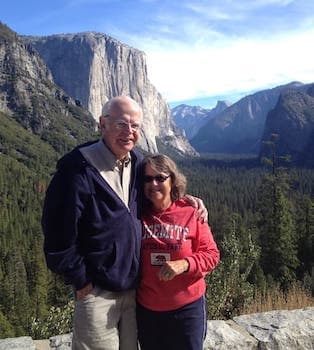
Curated with aloha by
Ted Mooney, P.E. RET
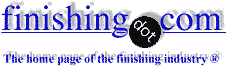
The authoritative public forum
for Metal Finishing 1989-2025
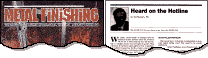
-----
Nickel-plating stainless
1998
To All:
I would like to effectively barrel nickel-plate stainless(304) steel parts and would like some recommendations. Currently the parts are peeling and blistering in a few areas on the surface. I am not sure if the part is oxidizing prior to nickel plate or is passive(not receiving a good contact in nickel strike). We utilize nickel sulfamate chemistry and a woods nickel strike bath. The part is electro-polished prior to plate and also receives a cathodic clean, so the part should be clean. I wasn't sure if the process needed a stainless steel activate prior to nickel strike and what the chemistry would consist of. Any recommendations would be appreciated and thanks in advance.
Dave BernardiniNo. 1 of 2 simultaneous responses:
1998My 2 cents worth is that it absolutely needs an acid etch/activate. Electropolish will make the surface very passive, it is frequently used in lieu of passivation and reportedly does a superior job.
Since you are going into a woods strike, my choice would be a 20 - 50% hydrochloric dip. Stronger is quicker, but corrodes everything around it. You might consider cathodic or periodic reverse current at a lower strength.
James Watts- Navarre, Florida
No. 2 of 2 simultaneous responses:
1998Dear Dave ,
Boy oh boy you have some problems , firstly the electro - polishing is producing a PASSIVE layer on the surface and must be removed before any plating is attempted , the whole purpose of electropolishing S/S is to obviously polish & deburr it but then to restore the oxide layer which gives the S/S its "Stainless" properties .
Secondly the very nature of the barrel plating process itself will produce more rejects plating S/S than conventional steel .
Activating S/S can be achieved in a bath of 10% HCl ( hydrochloric Acid )which has a means of reversing the current , start anodically & finish cathodically using about 10 Volts .
However whatever you try will give high reject rates just because of the barrel process , better results will be achieved with Racking the parts if possible
regards

John Tenison - Woods
- Victoria Australia
1998
I agree with John that barrel SS is more complicated to activate than rack parts. In order to plate in barrel , you need to activate it in the strike for a longer time (about three times as ling as for rack).
There are a lot of formulations for nickel strike solutions and it probably depends on the SS itself. My recommended formula is : 120 g/l Nickel chloride plus 10% v/v hydrochloride acid.


Sara Michaeli
Tel-Aviv-Yafo, Israel
Another thing to look at is the EXACT type of SS. Customers had a horrible tendancy to tell me that it was 304 SS, neglecting to tell us that it was a free cutting one, and exactly which one. The additive to the alloy can make it very difficult to activate and may require a special activating acid.
Even tho you are buying certified material, from the same lot number, sometimes it is not. A sad fact of life. In critical operations it can make a significant difference.
James Watts- Navarre, Florida
1998
Q, A, or Comment on THIS thread -or- Start a NEW Thread