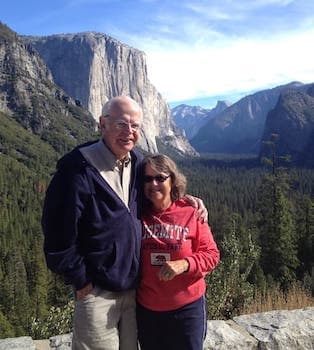
Curated with aloha by
Ted Mooney, P.E. RET
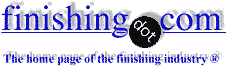
The authoritative public forum
for Metal Finishing 1989-2025
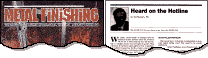
-----
Nickel Sulfamate Electroforming
1998
Q. Hello all,
First of all I'm a new inductee to the electroforming process. I have acquired my new duties not by education but buy default. I have been shown the overall process from beginning to end and discovered thru research of my own that certain aspects of the process have either been distorted or just misunderstood by the individuals that have passed it down, thus making it a bit of a black art!
The first problem to overcome was the condition of the 540-gallon nickel sulfamate tank. After being instructed by Macdermid chemicals to dummy plate, and the use of carbon filters over a four-day period, and also the addition of snac-am to address the stress levels of the solution. Also the addition of snap for proper pH levels in the ranges of 3.8 to 4.2. Prior to that I was experiencing pitting and separation from the mandrel or master as we call it.
We are starting from a photo light UV polymer material that is being sprayed with silver nitrate and reducing agent mixture. Some of my problems were originating at that point because of H2O mixtures being incorrect. The silver was lifting off and peeling from time to time causing bad image spots off the polymer. I think this was due to improper mixture ratios which were too concentrated. After discovering just how accurate this procedure is for reproduction I found out the limitations of the polymer and how porous its properties are!
Another problem is the formed nickel I'm producing has a heavy tarnished look to it. Any suggestions as to the tarnishing? I was told by MacDermid that the end result should come out with a mirror finish to it. After many attempts it wasn't happening. That's when I found out about the polymer and its porous tendencies. I tried a test and it confirmed my suspicions by taping part of the polymer with a nonorganic tape that has a smooth finish, the end result was half with a mirror shine and other half a dull porous look. Does anyone have any suggestions as to any polymers with a less porous finish that would still allow the image transfer?
Let me take this time and say that without the help and guidance from MacDermid Chemicals and a man name Levern (Vern for short!), I would be even more lost than I am now! Thanx in advance for any comments or suggestions that anyone might have!
Fritz
Fred Stenzel1998
A. "snac-am", no such animal. Snap-am is sulfamate nickel anti pit, air mechanical. It controls pitting, not stress. Air mechanical is for heavy agitation and is used rather than regular snap which foams badly under those conditions. A stalagmometer is required to control anti pit level. Wire rings can be used on plain snap.
Snap does not control pH, SNAC, sulfamate nickel acid compound which is sulfamic acid is used to lower the pH. A properly operated tank will always rise, requiring acid to lower. A pH of 4 is desired. 4.0 ± 0.1 is not hard to maintain if it is attended to daily. Lower than 4 slows down the plate rate. Higher than 4 plates a little faster, but tends to cause problems.
Separation from your mandrel could be caused by stress or difference in the coefficient of expansion of the two materials. No adhesion from bad prep will also cause it. Porosity of the material has to be looked at. Normally, it would cause a problem or surface roughness of the plate or it could be picking up chemicals from the prep tanks and leaching out wherever possible causing terrible adhesion.
Heavy tarnish, I will interpret as darker plate. This could be caused by dissolved silver or copper or cadmium or a few other metals. This will normally be darker in lower current density areas.
There is a serious problem with sulfamate nickel if it comes out like a mirror. Proper parameters will give a nice bright matte or satin finish. ASF, agitation and temperature will affect the look some. Not knowing the shape of your part, it is difficult to comment on why tape appeared to give the results that it did.
One thing that could cause apparent porosity is pH. The boric acid is a buffer in the solution to control pH in the diffusion layer, a couple of millionths thick layer of solution surrounding the part. Plating tends to raise the pH significantly which forms nickel hydroxide which looks dark and porous in the normal plate. Check the pH procedures. A shocking amount of people do not properly care for their pH probe, so it gives wrong answers. Leaving the probe in nickel solution will allow nickel ions to permeate the frit giving a green look to the solution surrounding in inner "tube". This messes up the chemical reaction; that gives a bad pH reading. The pH of a hot solution is not valid unless you calibrated the probe at the same temp. Constant exposure to high temp shortens the life of the probe also.
Recheck your boric acid level. I guess that it is low.
Try to get copies of the old Barret papers or reprints that Allied Kelite did. Jerry Lightenen authored numerous papers on sulfamate nickel in his days with AK. Sorry Jerry, I forgot how to spell your name. I am sure that all of this passed to MacDermid when they took over AK. I disposed of mine when I moved and sort of retired.
James Watts- Navarre, Florida
A. Stochastic +"diffusion-layer" "normally"-current density areas . . model in Mathematics, that being Mathematical (statistical) Models to analyze the "epitaxial": diffuse-layers for Chemical-Engineers to normally be left unsearched in too many 'results' in or with current search-algorithms for the density of epitaxial-layers and related areas of research.
Neil Pattersen- California, California
2000
Q. I recently did some electroplating of Ni onto stainless steel surface. In some instances I got "sandy areas on my mandrel. What causes those? I am new to the field.
Dr. Razi HassanAlabama A&M University - Huntsville, Alabama
2000
Preventing loss of silver in Nickel Sulfamate bath
Q. Hi, I was wondering about the deterioration of silver spray photoresist coated glass laser is already in the tank. Sulfamate Nickel was the electroplating process.
mohammad torabi- tehran, Iran
December 23, 2013
A. Hello,
I would make sure normal filtration is adequate. After a few filter tube changes, install a carbon pack (filter) and run for 2 hours then another carbon filter for the same time period. If the silver from the photoresist did not dissolve into the bath these measures should work. If there is silver in solution dummy plate at a low current density 3-5 ASF for 4-6 hours. After dummy plating the bath should get a full analysis to ensure any organic additives are within range.
Process Engineer - Malone, New York, USA
December 31, 2013
adv.
"The Sulfamate Nickel How-To Guide"
by David Crotty, PhD
& Robert Probert
published Oct. 2018
$89 plus shipping
Q, A, or Comment on THIS thread -or- Start a NEW Thread