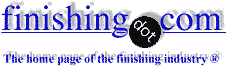
-----
Painting over electrogalvanized/chromated steel.
1998
I have any interesting problem. We are trying to apply a coating over a formed steel part. The material is purchased as electrogalvanized with a clear chromate conversion coating steel. Through punching and folding some surfaces are burnished and may have the chromate removed. I am having adhesion problems in some areas of the panel. I have some hypothesis to the problem but need proof.
1) The fabricator is using a forming oil (organic, and we are degreasing). By degreasing could we be leaving a residue behind, sulfur, chlorine etc..?
2) The galvanize may have lead in it. Could the process leave a lead smear and would this cause a problem?
Thank you for your help.
Wes MillerNormally it is a bad idea to have a chromate conversion coating between the zinc plating and the paint. Chromate films are used as parting agents! So, I would suggest starting at what we can be nearly sure is a trouble point, rather than searching for other possible trouble points.
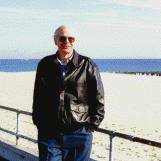
Ted Mooney, P.E.
Striving to live Aloha
finishing.com - Pine Beach, New Jersey
1998
I agree with Ted. The chrome is a starting point of the problem. Any surface without uniform surface profile and pretreatment will provide differing adhesion characteristics. It is difficult to answer your questions without knowing which parts areas are incurring the adhesion loss.
We have been over the chrome thing several times this year. You cannot pretreat a steel/zinc surface properly for painting that has chromate on it. The chromate will not accept the pretreatment.
If you are just cleaning/degreasing the metal before painting, then the surface profile or degree of cleanliness could be part of the problem. I will note here that both electrogalvanized and nickel flash steel have a property that allows mill oil to get into the grain of the plate (electrostatic and van der waals forces at work) that do make these steel types harder to clean than regular CRS. a mildly acid cleaning step or iron phosphate at lower pH 3.5 to 5.0 generally works better than alkaline cleaners.
As far as evaluating fabrication oil samples, that procedure is fairly simple. Request a sample of the fabricating oil from your fabricator. Paint the oil onto a flat test panel with a small paint brush. Let the oil cure over the weekend or over several days, then degrease the panel. After cleaning rinse it with water and observe the surface for water beading up on the surface. This is called the "water-break" test. If water beads up on the part, then it is not clean.
You may also wish to process the panel as you normally would with your parts and then paint it to check for adhesion. If it comes out fine then there is nothing wrong with that oil. If on the other hand there is adhesion failure, then you need to go back to your fabricator and suggest that he find another forming oil that will be more easily cleaned. The other alternative would be to change your process to be able to clean that oil.
One of the problems of this scenario is that your fabricator could be using 15 different oils, thereby multiplying the effort and time in the testing. The other problem is that fabricators are changing oils all the time. Will you be notified by your fabricator that they have changed their process? Will the change produce a problematic outcome for your painting operation?
The way around this is to establish an "approved" list of oils that your fabricator can use. Obviously, these are the oils that you can clean from the parts. They are responsible then for qualifying any "new" materials to the list.
I may have gone too far there, but hope it helps in some way...
Good Luck.
Craig Burkart
- Naperville, Illinois
Powder coating on HDG has become a very popular finish for security fencing in the UK. The biggest problem for the powder coater is the removal of chrome passivation and or white rusting (Zn Oxides). The most effective solutions have been found to be those based on approx. 4% PHOSPHORIC ACID. Customers of mine have been using this solution ahead of Zn Phosphate for 12 years with no serious failures reported. The solutions performance is enhanced with other additions and we sell it as a proprietary blend.
Ian Rogers- Wrexham. UK
1999
One of our customer to whom we supply Electro Galvanized Steel Sheets have lately complained that they are having adhesion problems & reported to us that a independent test conducted by their paint division revealed a anti finger resin coating which was not allowing proper paint adhesion. Supplying mill's MTC are showing they are only phosphated & Unoiled as per JIS G3313 SECC, with E16 / E16 zinc coating.
Customer has requested that future supplies should comply with spec JIS G3313 SECC, Chrome Free & Lightly Passivated.
Having read some of the responses posted by other people on this site, would lightly passivated pose a problem for painting. Customer hopes to achieve 1000hrs of SST after powder coating.
Currently they are de-greasing, cleaning, phosphating, cleaning & then powder coating their end product ( enclosure boxes ).
Any help in determining the correct spec would be highly appreciated.
- Dubai, United Arab Emirates
November 12, 2008
Q, A, or Comment on THIS thread -or- Start a NEW Thread