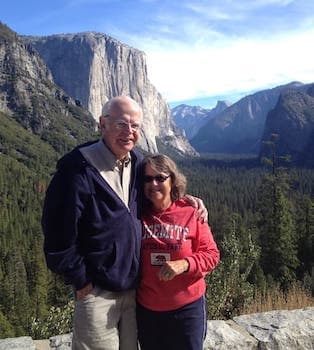
Curated with aloha by
Ted Mooney, P.E. RET
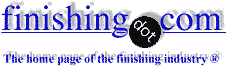
The authoritative public forum
for Metal Finishing 1989-2025
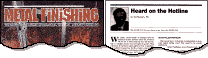
-----
Correlation between accelerated weathering & natural weathering. SAE J1960
Dosage = Irradiance X Time X Applicable conversion factor, (usually 3.6, which gets from joules to kilojoules and from seconds to hours, since a joule is defined as a watt-second).
More simply put:
kJ/m2 = W/m2 x 3.6 x Light Hours
I'm wondering how the 3.6 came to be. I understand why it's there, but why 3.6?
Also, it seems that the yearly sunlight for Florida is low. I have Q-Sun data that shows it to be average 6100 mj/m2 (6100000 kj/m2)
R & D Test Technician - Agawam, Massachusetts
June 30, 2021
A. Hi Walter. Perhaps I'm not understanding your first question, but your equation says you are looking for kJ/m2 (how many thousands of watt-seconds per square meter) when starting from watt-hours. So you multiply hours by 3600 to get to seconds, and divide watt-hours by 1000 to get kw-hours. And 3600/1000 = 3.6. Perhaps labeling it 'light hours' instead of just 'hours' is causing confusion?
For your second question, some sources I checked say the Global Horizontal Irradiance for Florida is about an average of 4.9 kw-hr/m2 per day. Multiplying by 365 days per year I get 1789 kw-hr/m2 per year. Joules or watt-seconds would be 3600X that or 6,438,600 -- which is pretty close to your number. Sorry, I'm not conversant with this stuff, and don't understand why our answer is more than double that of Kenneth and Allen. All I can say in support of ours is that my home is a bit less sunny, with GHI of 4.1 kw-hr/m2 per day, and if I do the same calculation, then add in a 19% efficiency factor for the solar panels it comes out just right.
Luck & Regards,
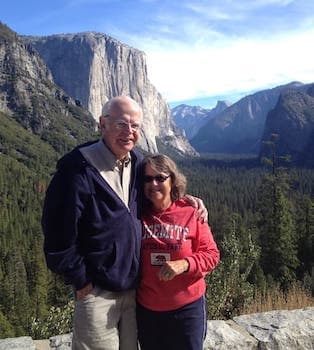
Ted Mooney, P.E. RET
Striving to live Aloha
finishing.com - Pine Beach, New Jersey
July 2021
⇩ Related postings, oldest first ⇩
Q. Does anyone have any knowledge on the correlation between accelerated weathering testing & actual natural weathering testing for UV / Gloss retention / colour retention / chalking?
Example: 3000 hours accelerated weathering = 125 months of natural weathering. Is this close?
Regards,
Ramoo PuruSingapore
1998
A. Correlation between outdoor and artificial weathering devices is very material dependent. Factors that must be considered are light (both quantity and quality), moisture cycles, and temperature.
I don't know if 3000 hours is close to 125 months, but that sounds a bit unrealistic. What type of artificial device did you use? What was the cycle? What was the irradiance used? Commonly known cycles using a Xenon-arc source (the closest match to natural sunlight) require 1500 hours to achieve the same amount of radiant exposure as 12 months exposure in Florida. Degradation amounts may or may not be similar.
Matthew McGreercorrosion testing equipment - Chicago, Illinois, USA
1999
A. 125 months is about 90,000 hours. This is 30 times the 3000 hours of test time. This is too much acceleration by any of the standards. A possible ratio is in the range of 8 to 12. This depends on the test conditions (temperature, humidity, irradiance level, condensation process, humidity, etc). The ratio would also vary according to the material that is being tested.
In the case of the Xenon arc test, the filter used would again be a determinant of the effects on the sample, while in the case of the QUV fluorescent tester, the median/peak irradiance wavelength of the lamps used would be a major factor in the effects on the sample.
It would be necessary to study the SPD of the lamps used also.
Varadarajan Seshamani- Bangalore, Karnataka, India
2002
Multiple threads merged: please forgive chronology errors and repetition 🙂
SAE J1960 correlation to Florida exposure
Q. Many sources site that Florida's radiant energy exposure for 1 year is approximately 2800 KJ/M2. In the automotive industry, they use the SAE J1960 standard to evaluate weathering of exterior plastic materials by accelerated means. Most engineers involved with this test state that 2500 KJ/M2 is approximately 2 years of Florida testing. Why?
Kenneth BarawRain Bird Corporation - Tucson, Arizona, USA
2004
A. 10-year rolling average measurements of Miami solar radiation, south facing 45-degree inclination, are indeed ~2800 kiloJoules/m^2 @ 340nm per calendar year. It is also true that anecdotal conventional wisdom equates 2500 kJ/m^2 @ 340nm to produce the weathering effects seen in two and sometimes even 3 years of Miami weathering.
First, it is important to understand that the spectral power distribution (light intensity vs. wavelength) of the SAE J1960 test method does not match actual Miami sunlight. The test, which uses a quartz/borosilicate-S filter combination, was developed in the 1970's when "harsher is better" was the prevailing testing philosophy. This test has UV energy at wavelengths significantly below the ~300nm cut-on of terrestrial sunlight (thank the ozone layer), in fact down to about 275nm. Since Planck's law says that photon energy is inversely proportional to wavelength, this low wavelength UV has sufficient energy to cause much more damage to organic materials than sunlight.
While you might think that this would just result in a shorter test time, it has frequently been shown that the SAE J1960 test as written has the potential to change the photo-chemistry of degradation. While this sometimes results in faster same-type degradation (hence the 2-3 yr Miami "equivalent") it can both cause failures not seen in outdoor exposures as well as cause different kinds of changes (some actually less severe!) than will happen in the outdoor exposure. Either way, it can be a non-predictive test for some materials. Some automotive companies have moved away from this test as written and incorporated better optical filter combinations (Boro-S/Boro-S or CIRA/Soda Lime) that more closely match true Miami solar radiation. So when comparing J1960 to outdoors, you're comparing apples to oranges and they don't equate.
One other factor is that this type of comparison, based on a single factor (solar radiant energy) does not take into account the other weathering factors of heat, moisture, etc., and their synergistic effects, which magnify the effects of solar radiation.
While the automotive OEM's and suppliers use J1960 (as-written or modified) for preliminary material approval, they still conduct outdoor testing to validate the interim results and develop models for materials that "correlate" the lab exposure to real outdoor weathering.
Allen ZielnikAtlas Material Testing Technology LLC - Chicago, Illinois, USA
2004
A. The SAE J1960 test does include heat aging (83 °C) and water spray cycles so it should account for some of these other effects you mention. You make a good point about the light source though. Has there been any activity focused on changing the light source and filters to more accurately predict real life exposure?
We use SAE J1960 heavily for automotive and non-automotive weathering as a de facto test to predict long term performance. Automotive OEM's require this. Outside of automotive, perhaps we should be more careful about the tests we choose and the light source/filter combinations.
Still, it's a conundrum when considering accelerated tests like Xenon Arc or even oven aging, to test under more severe requirements to predict performance over very long periods of time (i.e. 1 - 10 years) with a test that is done within 3 - 4 months or sooner. These tests assume the time-temperature superposition principle without taking into account thermo-oxidative effects at higher temperatures, or the deleterious effects of shorter wavelength light (and thus higher energy). We see the same thing in tests like UL 1581 for wire and cable.
The other issue I have with SAE J1960 is that it does require oven aging at 83 °C for most of the test cycle. Some polymers undergo heat degradation that cause yellowing or darkening not at all due to UV. When this test temperature is lowered to 63 °C, the effect of discoloration is much less pronounced and we can focus mostly on the UV effects.
Advanced Polymer Alloys - League City, Texas
2006
Multiple threads merged: please forgive chronology errors and repetition 🙂
Q. Hi,
I'm a new member in these testing matters. How can I determine the duration of the accelerated weathering test according to SAE J1960?
automotive - Malaysia
2006
2006
A. The duration of the testing is usually specified by the OEM or Tier 1 supplier that requires a certain dosage (usually expressed in kJ/m^2 @ 340 nm). You can use the following formula to determine the duration (in time) for that test:
Dosage = Irradiance X Time X Applicable conversion factor, (usually 3.6, which gets from joules to kilojoules and from seconds to hours, since a joule is defined as a watt-second).
More simply put:
kJ/m2 = W/m2 x 3.6 x Light Hours
You must also factor in time for dark cycles.
It is possible that you are wanting to know if there is some sort of "acceleration factor" with this test method. In other words, "How many hours of SAE J1960 equals one year of real-world exposure?" This is much more complicated, since the only way to truly answer this is to say that "it depends on the material tested." The only real way to determine it is to perform actual natural weathering tests in conjunction with the accelerated tests to determine the levels of correlation and acceleration for your particular type of material. At some point, you may be then able to extrapolate out to longer periods of time. But doing that carries certain risk.
Hope that helps.
corrosion testing equipment - Chicago, Illinois, USA
Multiple threads merged: please forgive chronology errors and repetition 🙂
Q. I'm also having hard time knowing the correlation between natural and accelerated weathering. If the Xenon-arc source requires 1500 hrs to achieve 12 months exposure in Florida, what was the intensity or amount of radiance in the place? In the Philippines, this relation would not be the same because of the difference in radiant intensity -- am I right? 12 months exposure in the Philippines might be lesser or greater than 1500 hrs in the xenon-arc source. Please help me find a correlation between natural and accelerated weathering especially for sealant test because currently it's my thesis. Please help me find the answer.
Jaymes Mendoza- Manila, Philippines
February 4, 2009
Q. What is the correlation between accelerated weathering testing & actual natural weathering testing for woven PP fabric if I test for 200 hours using QUV B lamps?
Engr. Md. Mehdi HasanFIBC Manufacturing - Dhaka, Bangladesh
October 11, 2018
Q. Hi I have a plastic wood composite product and I am having difficulty in acquiring a proper artificial weathering test. This depends on the test conditions (temperature, humidity, irradiance level, condensation process, humidity, etc.) The ratio would also vary according to the material that is being tested using a Xenon-arc source
Some agencies are claiming that 3000 hours = 10 years
Can someone clarify this for me as I would need the product to last 10 years or more without showing signs of aging.
Plastic Recycling / Meltin Vaste - Auckland New Zealand
September 6, 2019
A. Hi Eric,
Is the wood being exposed, naturally, in the horizontal or vertical position as this would influence the amount of Xenon exposure hours to replicate 10 years? For example if we applied stripes to the roof of vehicle, exposed in Florida USA, we would expose for 6000 hours whereas these same stripes applied on the sides of the vehicle, in same environment would be exposed to 3000 hours SAE J2527 exposure conditions to replicate 3.5 years natural weathering in these conditions - Florida is a region 3 climate zone. I think that New Zealand is a climate zone 2 which means, for the same weathering hours, on the same vertical plane, your 3000 hours would translate into longer actual durability period. You should speak to a company like Atlas Weathering or Q-Sun who have experts in this field. Gary
- UK,London
October 12, 2019
Readers --
Please see also Thread 16994, "Xenon and Carbon Arc Weathering Standards SAE J1960 & J2527"
Q, A, or Comment on THIS thread -or- Start a NEW Thread