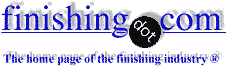
-----
Deburring for a grinding purpose
Currently in our metal finishing process, we use stainless steel brushes (8" diameter, braided, running at 1000 rpm) to remove burrs from an edge grinding process (double-bevel knife blades). However, the issue is that stainless steel brushes are wearing out quickly which is adding extra cost and downtime to our process. We have tried using carbon steel brushes with the same characteristics as above, but have found that they leave a "blackening" near the tip which is considered unacceptable. Does anyone have any alternative (and inexpensive) ideas for deburring?
Thanks in advance.
Tom Beyreis- Wheeling, Illinois, United States
2003
There are still a lot of unknowns here. Are the parts or the wheel in a fixed position?
If so, that may mean that there is non-uniform pressure on either the part or the wheel.
I'd check that out first.
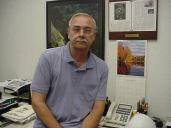
AF Kenton
retired business owner - Hatboro, Pennsylvania
2003
The grinding wheel apparati are remaining stationary while the blade is fed through (except when the grinding wheel wears away at which point the grinding wheels are moved closer). The feed rate of the material ranges from 1-4 ft/min, and the grinding wheels are spinning at a constant 3000 rpm. One possibly important note to add is that the burr "chips" are similar in shape to that which would be produced in a milling operation (i.e. wide and in a coiled shape).
Thanks in advance.
Tom Beyreis- Wheeling, Illinois, USA
2003
For a quick answer, I think the question of wear is relevant to pressure and the other wheels. Meaning, try to replace your wire wheel with a non-woven wheel and compare results. You may want to stay with wire, but the test will give you a comparison. I lieu of a wheel system, you may want to try a guilotine fixture type approach where you insert the blade into a fixed die/mold that causes the edge of the blades to drag across the edges, almost like a knife sharpener,
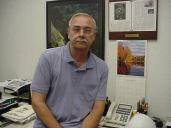
AF Kenton
retired business owner - Hatboro, Pennsylvania
2003
We have tried the dragging method, but have had fairly unsatisfactory results (i.e. even though we're using a light force on the blade, the marks produced show a horizontal surface finish against the vertical main grind). I have been reading about pressure washing to remove burrs in machining operations, but feel like the cost may be too great. First, am I barking up the wrong tree trying to find something like this? Second, am I wrong that the cost may outweigh it's usefulness? Any other ideas? I appreciate the response so far.
Thanks.
Tom Beyreis- Wheeling, Illinois, USA
2003
You are right about a water system and pricing, but lets get back to the drag system. Instead of metal on metal, did you think or try a hard felt cotton system?
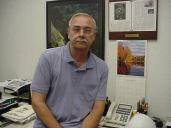
AF Kenton
retired business owner - Hatboro, Pennsylvania
2003
We have not tried using any type of cotton or felt system. I have successfully been able to remove a good majority of the burrs by "slicing" the blade through a piece of paper, so your advice may work. I will set up and run a few tests and let you know the result. Thanks!
Tom Beyreis- Wheeling, Illinois, USA
2003
Q, A, or Comment on THIS thread -or- Start a NEW Thread