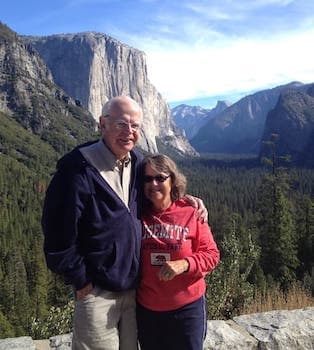
Curated with aloha by
Ted Mooney, P.E. RET
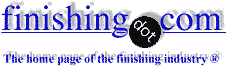
The authoritative public forum
for Metal Finishing 1989-2025
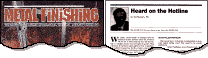
-----
What is root cause of rust on a powder coated steel cabinet?
Q. My company sells electronic equipment which is housed in steel cabinets. The steel cabinets are formed by a sheet metal company and sent to a powder coater. The powder coater uses the following steps:
1. Alkaline cleaner
2. Tap water rinse
3. Iron phosphate
4. Tap water rinse
5. Dryer
6. Powder is sprayed on
7. Painted parts are sent through oven where the paint is cured.
The problem is paint is blistering on some cabinets painted 7 months ago. The paint is easily scraped off in these areas revealing rust. Here are the facts:
1. The rust almost exclusively appears in either the front face or back face of the cabinet - not in both and not in other locations
2. This fabricator and painter make other parts for us (during this time frame) and none of those parts has the problem.
3. A metallurgist examined a sample piece and says there is no evidence of subsurface rust - implying the rust developed some time between cabinet fabrication and powder coat application
Both the fabricator and the painter say that they inspect for rust and that this was not the case with these parts.
So... what in the forming or powder coat process could cause rust on a particular surface (but not others) on one type of part but not all parts? The only theory to date put forward by the powder coater is that the orientation of the cabinets (hung horizontally) coupled with a slower-than-normal line speed allowed a concentration of iron-phosphate along the front (or rear) of the cabinet and that surface flash rust became worse over time when exposed to the heat/humidity of the warehouse where they were stored.
The problem: we have a cabinet from the same batch from that vendor which has been in a temperature controlled environment with the same problem (although not as bad) as well as a cabinet from December which shows no problem.
Also, our former powder coater hangs the cabinet horizontally and has a similar powder coat line and has never had this problem. Any help is appreciated.
Scott Tschetterelectronics manufacturer - Lynchburg, Virginia
2003
A. Hi Scott,
I think the problem is related to the lag time between the chemical pretreatment steps and the powder coating process. Your first paragraph implies that the pretreatment and the powder coating are performed by different companies.
An iron phosphated steel surface is a surface that is ready to be painted as soon as possible. A phosphate coating has very little inherent corrosion protection. The longer the time between the phosphating operation and the painting step, the better the chance of surface rust forming. Despite what anyone involved says about inspecting the parts for rust, it is never a good idea to let unprotected parts that have been phosphated sit around unpainted for very long.
The fact that some parts display rust and others do not may not have anything to do with the process. It is not unusual for fabricators to make different parts from different sources of steel. While the steel sources may appear to be similar, they will not necessarily behave identically in a corrosive environment.
The powder coater's explanation does not hold water. A part with a larger amount of conversion coating will not be more likely to corrode than a part with less coating. The fact that the parts were exposed to heat and humidity before painting tells you everything you need to know. An iron phosphate coating is not expected to prevent corrosion in such an environment. An iron phosphate coating is a pre-paint treatment.
The lag time between phosphating and painting needs to be decreased. The ideal situation is to find a job shop that will phosphate the parts and powdercoat them in one operation.
George Gorecki- Naperville, Illinois
A. Hi Scott,
What George Gorecki has suggested is very correct, the lead time between the pretreatment and the Powder coating should be reduced..... but here, I would like to suggest you one more thing which I am sure will work for you and that is instead of Iron Phosphating , go for Zinc Phosphating, which will give you more time between the pretreat and the coating.
Best wishes,
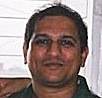
Atul Bhide
jobshop / applicator - Mumbai, India
A. Scott,
One possibility that has not been mentioned is that, during the pretreatment process, it is quite common for conveyor lines to be stopped (loading, painting, unloading issues - workers falling behind). If a line stoppage occurs, the damage to parts in the pretreatment process will vary greatly depending on what "stage" the parts are at. This may explain why some parts are okay, while others processed at the same time are suspect. Parts "drying down" between stages is my suspicion. Washers are typically hot, humid chambers and dry down occurs sometimes within 30 seconds or less, so a part caught between stages during this line stoppage is at risk. If a part experiences this, there will be deposits of chemical dried and hardened on to the substrate that can affect paint adhesion. I personally have seen line stoppages that last for minutes, so imagine the possibility for issues in a situation like that!
The problem here, is that if the spots or deposits are not recognized prior to powder coating, the finished product may not exhibit any evidence of the issue - cosmetically they often appear okay. The problems are often not discovered until the item is the customer's hands when the paint adhesion fails.
I hope this helps. At the very least, it is one more thing to discuss with the powder coating shop.
Regards,
Eugene Betke- Canada
Q. Thanks to all for your input. I need to clarify what I wrote. The sheet metal fabricator does not prep the cabinets for paint. The parts are shipped to the powder coater with standard water-based mill oil coating on them. The powder coater has one line with alkaline rinse, tap water rinse, iron-phosphate, tap water rinse, dry, paint application, bake. Days or a week may pass in between shipment of parts from fabricator to powder coater but once the painting starts there is no break. The line rate is about 6 ft/min. I took another trip to the powder coater and their best guess now is that contaminated rinse water left residue on the parts during the final rinse before drying. We sent samples to a lab and Cl, K, and Fl were found in the sample that is rusting. They suggest changing the orientation of the hung part to improve rinse off and using RO water at the final rinse.
My questions are these:
1. They use tap water (non-DI water) for everything else - why are only my parts rusting and not other parts for other customers?
2. The conductivity of the rinse water is measured twice per day and recorded. Their upper limit is 1100 micro-mhos. The logs show that the days in question the conductivity measured between 500 and 800 micro-mhos. If the tap water is the culprit, why are the conductivity levels not elevated?
Thanks to all for your thoughts and opinions!
Scott Tschetter [returning]- Lynchburg, Virginia
A. Scott,
Your powder coater may have some other contributing factors as well as a tainted rinse....I suspect you are getting some drying off between stages at the slower lines speeds and at times the rinses may contain a excessive amount of alkalinity (over 200 ppm) and / or high chlorides (over 75 ppm) that could contribute to the bubbling or lift of the paint film. Keep in mind that the conductivity can read 800 one day and be fairly decent and the next day be really bad at the same conductivity. Sodium salts register a different conductivity level than a calcium or magnesium salt or a oil or surfactant. Ask the powder coater if he can accurately determine the carryout water volumne and makeup volumne along with the amount of counterflowing rinse water from the first two stages and I think you might start seeing some potential contributing factors to this problem. Last but not least, could these cabinets have a hinge assembly that could weep any residual oils that might not be cleaned out 100% and under a high heat typical in a powdercoat curing oven?
Brian Lamphron- Sioux Falls, South Dakota
A. Scott,
From a powder Mfgr. point of view we would check that the substrate is clean - clean the item using a different process (just for comparison) i.e. a solvent. Check film weights - cabinets are difficult beasts - too many corners i.e. faraday cage effect. Monitor stoving time and temp using special equipment (ask your powder supplier to borrow one). Then place this special cabinet along with normal items ex powder coater and see if there is any improvement. Certainly we would recommend Zn Phos or a special waterborne primer.
Terry HicklingBirmingham, United Kingdom
Quantify allowable time for phosphate pretreatment to remain bare before powder coating
Q. Hi
As per the details given, comparing to Iron phosphating, time lag between phosphating and powder coating in zinc phosphating is more. Can you please quantify the time duration permitted for both Iron and zinc phosphating processes?
- CHENNAI, INDIA
December 21, 2015
A. Hi Theyaga. I hope someone will be able to quantify it for you, but I doubt it. Phosphating in this sense is not a final finish and is not intended to be anything but a pretreatment in the process of powder coating. Some shops, especially if they use HCl for any reason, are extremely corrosive environments; other air conditioned shops without aggressive acids are quite benign environments.
Letter 34839, "Zinc phosphating for 72 Hour salt spray test endurance" expands upon the issue of corrosion resistance of phosphates, and seems to suggest that if you are still able (in this age of RoHS) to use a chromate dip after phosphating, you may be able to get a satisfactory life to meet the issue of temporary rust prevention without rust preventative oils. Good luck.
Regards,
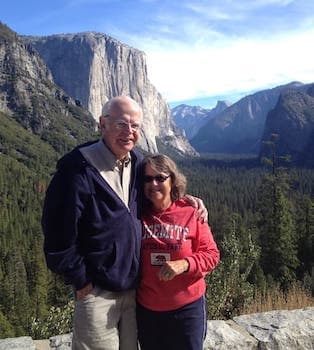
Ted Mooney, P.E. RET
Striving to live Aloha
finishing.com - Pine Beach, New Jersey
Powder coating rusty at the top of the metal enclosure
Q. My client recently send me a photo of our enclosure with rusty surfacing after powder coated.
We have not encountered this issue before and I would like to hear your input pertaining to this.
I am considering the environment factor. The placement of this cabinet is outdoors and it is exposed to rain and sun. My client sent some photos and it seems like water is stagnant at the top of the cabinet and rust can be seen to resurface. Furthermore, the powder coating at the edge of the cabinet also chips off and rust is visible.
I have read through some of the thread posted and I have consider the possibility of the processes could be one of the problems. However, I spoke to the powder coating guys, they claim that the enclosure is exposed to the rain water.
My question is: would rain water being stagnant cause the cabinet to rust? Or is it possible that the powder coat layer is insufficiently coated on the cabinet?
sales - Malaysia
June 13, 2017
A. It's my opinion that powdercoating isn't a form of corrosion protection for outdoor use.
Given that all paints are porous, including powder applied coatings, then rust will form eventually in weather exposed steel.
(by the way, "powdercoating" doesn't define the coating, rather it defines the method of application. What was the polymer that was applied?)
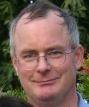
Geoff Crowley
Crithwood Ltd.
Westfield, Scotland, UK
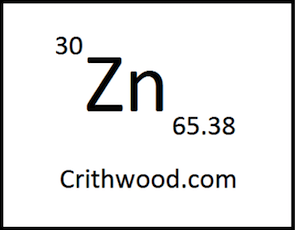
A. Hi Cynthia. If they sent you pictures for evaluation, and you're asking others to assist you in the evaluation, it would probably be best to supply those pictures :-)
I partially agree with Geoff. Powder coating per se is not a proper treatment; you need pretreatment such as phosphating, and possibly an electrocoat primer, before the powder coating. Because of the chipping and rust, I suspect inadequate (if any) pretreatment. Good luck.
Regards,
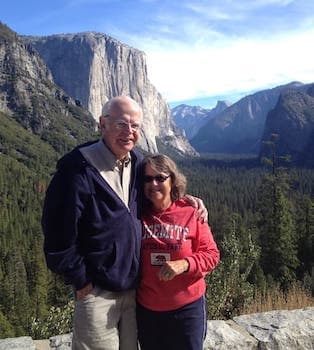
Ted Mooney, P.E. RET
Striving to live Aloha
finishing.com - Pine Beach, New Jersey
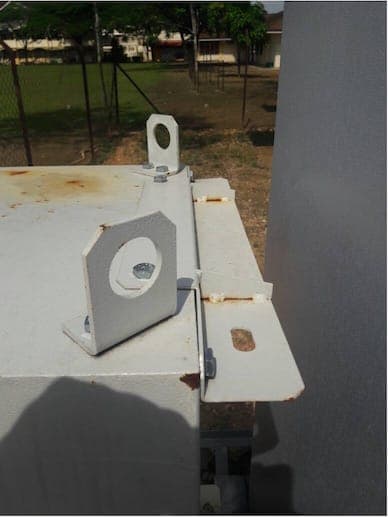
Q. Hi Ted,
Here is the photo.
The process of the treatment includes the phosphating and water cleaning for cleaning. We don't have the electrocoat prime process.
Please take a look at the photo below. The top cabinet has water patches and it seems the rust is more apparently around that area.
What do you think caused this?
sales - Malaysia
July 5, 2017
Hi Cynthia. The pretreatment and powder coating were obviously not up to the job of protecting this surface in this exposure condition. Whether it would have held up for interior exposure in a climate controlled room would only be a guess, and how it was supposed to be exposed may be part of your contract documents but I can't guess. It's possible that salt, industrial fumes, lawn fertilizer, or something else accelerated the corrosion.
Still, I tend to doubt that this finishing was adequate for much of anything. Sorry, just my guess. You probably need to do the finishing to specific specifications which might include accelerated corrosion testing.
Regards,
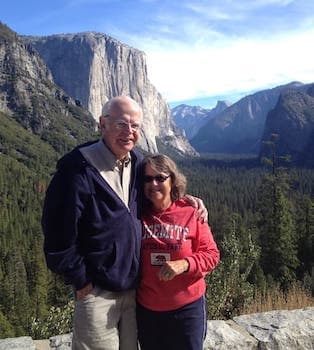
Ted Mooney, P.E. RET
Striving to live Aloha
finishing.com - Pine Beach, New Jersey
A. It's a poor (inadequate) specification that's been used here by the looks. Appears to be a single coating powder applied textured polyester.
That won't stop rust in this fabrication. Its made worse by the design. There are overlapping areas of steel unwelded (bracket to right) where the coating will not be present leaving exposed steel to water weeping in between. The bolted connection presumably were after coating, not so bad.
But in any case, this is a porous coating, not water impervious, and not giving any electrolytic protection so inadequate. Possibly done to a price, but with a short sighted view of cost.
If colour is required, then a multi-coat system with at least one coat containing zinc.
If aesthetics not so important then hot dip galvanizing would be a cost effective solution.
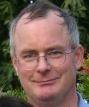
Geoff Crowley
Crithwood Ltd.
Westfield, Scotland, UK
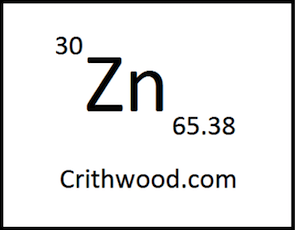
A. Adding to the above responses, it looks like the cabinet has a lot of sharp edges. One coat of powder will not fully cover sharp edges, leaving bare steel on the sharp edge. If you can file these down, it will help.
I would make sure the parts are blasted if they contain mill scale, phosphated, then use a zinc rich epoxy powder primer followed by polyester topcoat. Total coverage should be at least 8 mils to cover the edges.
- Rochester New York
July 29, 2017
Q, A, or Comment on THIS thread -or- Start a NEW Thread