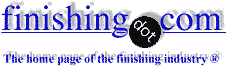
-----
Sulfuric Acid Anodize Rinsing Problems
Q. Hi,
We have a little anodizing shop that mainly does sulfuric acid anodizing Type II and Type III. We have a double immersion rinse following SAA, both are cascading. We have not had any problems necessarily but I am trying to get better control of our process.
I am curious if there are any rinse water requirements or monitoring that may need to be done. MIL-A-8625 / MIL-PRF-8625 [⇦ this spec on DLA] does not call out any rinse water requirements. Boeing's SAA spec calls out 350 ppm max which would be very difficult to maintain on the primary sulfuric rinse. Our flow would exceed our limits.
What are some other recommended rinse water requirements or guidelines?
Chris Culp- Vancouver , Washington, USA
2003
A. Read Ted's article on rinsing at this site. The cheapest rinsing is done by having a third rinse tank, counterflowed. Saves a massive amount of water at a relatively small installation cost. If you were really worried about the first rinse tank after the anodize, you could install a pH meter, but readings a few times a day would be a lot cheaper. Low pH paper would work. I do not like broad range paper, except for the crudest of work. If you do install a third tank, the pH in the first tank after the anodize tank will drop. You definitely would not want to let a rack of anodized parts set in it over break time or when the seal tank was backed up.
James Watts- Navarre, Florida
2003
A. While I agree that Ted wrote an excellent article, I'm a very FIRM believer in a DI spray rinse after dip rinsing. This insures that only very clean water gets transferred into the next process step. A lot of the tap water is very high in silicates, calcium, etc.
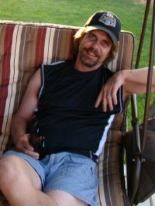
Marc Green
anodizer - Boise, Idaho
2003
October 16, 2008
Good point, Marc. Thanks.
Regards,
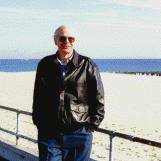
Ted Mooney, P.E.
Striving to live Aloha
finishing.com - Pine Beach, New Jersey
Final Neutralization Rinse for Sulfuric Acid Anodize needed
Q. A final acid neutralization rinse is needed for MIL-A-8625 / MIL-PRF-8625 [⇦ this spec on DLA], TYPE II, CLASS 2 coatings before our final Deionized Hot Water Rinse and parts Drying process steps. I thought about a hot/warm sodium, or potassium, bicarbonate hot soak @ 1 oz/gal, but no experience on use or possible side effects of introducing a neutralizing bath. Reason being that aluminum parts have braze welds with tiny pores and crevices that have trapped acid. Unfortunately, we cannot use chromic acid anodizing. Maybe someone has used and controlled a similar neutralization solution.
Tom AndersenAnodizing - Balto., Maryland, USA
2005
![]() |
2005
"The Surface
Treatment & Finishing of Aluminium and Its Alloys" by Wernick, Pinner & Sheasby ![]() on eBay or Amazon or AbeBooks (affil link) A. I'm not sure what you want to neutralize. If you're worried about sulfuric acid, they you should use dilute (5%) nitric acid after double rinsing after anodize. I know this sounds counterintuitive, but it works. Alkaline materials should be avoided since they will 1) precipitate metals. and 2) may damage the anodize coating. ![]() Jeffrey Holmes, CEF Spartanburg, South Carolina A. Bicarbonate makes for a good controlled pH rinse as it is a buffer, so the pH tries to stay under 9. - Navarre, Florida 2005 ---- |
Maintenance of pH of rinse water
Q. My concern is the maintenance of our rinse water after anodizing. Can I use sulfuric acid to reduce its pH? The specs required is between 5.5 to 8. How does everyone dealing with anodizing maintain their rinse water pH to its required level?
I appreciate any help or advice I could get.
Thanks,
Nila O. Par- Winnipeg, Manitoba, Canada
2003
A. After sulfuric acid anodizing, the pH in the rinse gradually lowers, so you would like to raise it, not reduce it. You could use lye or a similar caustic, but now you are forming sodium sulphate salt in the tank. You do not want to rinse with a "salt" water rinse. If you have multiple rinse tanks, you can let the first one get a rather low pH because later rinses will take care of it. You can NOT leave parts in that rinse tank for any extended time as it will slowly eat the anodizing off. If you only have a single rinse tank, you will use quite a bit of water to keep the pH within limits. If you do not, you will mess up your seal or dye tank pH which IS a problem. Can you add another rinse tank or split the existing one into two cells. Read Ted's article on rinsing.
James Watts- Navarre, Florida
2003
Q, A, or Comment on THIS thread -or- Start a NEW Thread