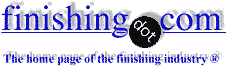
-----
Effect of welding St. St. to mild steel on megayachts
2003
My company builds steel luxury yachts and management is suggesting to weld stainless steel directly to the steel hull. For example stainless steel pipe overboards, and anchor recesses in the hull.
It is proposed that the anchor recess will be highly polished.
1. What impact will this have on the corrosion in seawater?
2. What is the best type of stainless steel to use in order to maintain a high quality surface finish?
3. What can I expect to happen to the surface finish of the highly polished stainless steel after some weeks/months being in contact with the seawater?
a yacht builder- Perth, Western Australia
When you say stainless steel I am assuming you mean 18/8 type austenitic steel. As there is a significant galvanic potential between mild steel and austenitic steel the mild steel will corrode without protection. However, if you already have sacrificial protection for the mild steel it will be OK.
Buffing of the stainless steel will not affect it's corrosion resistance as the protective oxide layer will re-form quickly. With time the stainless steel will become dull and will need re-polishing. A lacquer or varnish on the polished surface would help maintain a polished look for a longer period, although it might damage easily.
A suitable grade that is weldable and has good marine corrosion resistance would be 316L.
One thing you should consider is that it might not be possible to weld mild steel to austenitic steel due to the differences in thermal expansion/contraction rates. During cooling after welding there is a strong possibility the weld will crack.
Sounds like you need the services of a metallurgist.
Best of luck and don't forget management always have the best ideas.
John Hetherington- Montréal, Québec, Canada
2003
As you already know, it is not a great idea to weld the two together for a number of reasons. If you have to do it, you could electropolish and passivate the surface of the ss parts to impart the best corrosion resistance for the longest time. I agree that a coating on the stainless can only be long term problems unless the coating is permanent. If it starts to peel it will be a mess to clean up. I also agree that whatever treatment you give it will never be permanent, and that 316L is the minimum grade to be resistant to salt water in these conditions.
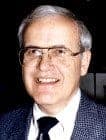

Lee Kremer
Stellar Solutions, Inc.

McHenry, Illinois
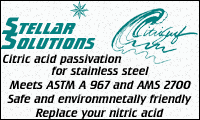
2003
January 8, 2010
May background is mechanical engineering, but I am not a welding expert. BUT I have owned a steel yacht and sailed it around the world.
Some stainless to mild steel stick welds done 30 years ago are sound, some not. The mild steel will always corrode in preference to the stainless. You can minimise this by ensuring that paint from the mild steel is carried over the weld onto the stainless. The difficulty is to get the paint to stick reliably to the stainless. All stainless on a boat should be a close to mirror polished to minimise rusting of the surface.
The British Stainless Institute recommended to me that the stainless surface finish be dulled for about 25 mm (or more) back from the weld so that, after the welding, the paint has a chance of sticking, and maintaining an integral barrier to stop sea water acting as an electrolyte at the interface of the 2 metals.
Stainless should be 316L.
- Sydney, NSW, Australia
Q, A, or Comment on THIS thread -or- Start a NEW Thread