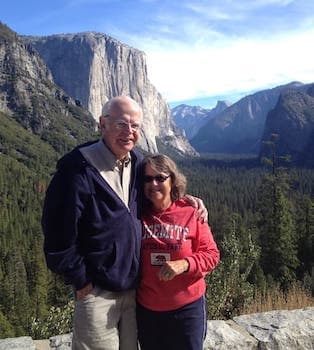
Curated with aloha by
Ted Mooney, P.E. RET
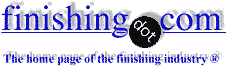
The authoritative public forum
for Metal Finishing 1989-2025
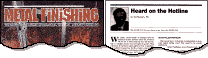
-----
Dow metal H: What/how of Conversion coat
Q. Hi,
What specific chrome pickle process should I use for Dow metal H?
I will be painting afterwards with a 2 part epoxy.
Dow Metal H consists of 90.8% Mg, 6% Al, 0.2% Mn and 3% Zn.
Thanks,
John Morellian antique aircraft restorer - Pittsburgh, Pennsylvania, USA
2003
A. I believe this to be a casting alloy, so use the following (partially from the finishing.com FAQ on the subject): Type II Chrome for treatment for castings:
Pickle solution
sodium dichromate (.2H2O) 24 opg
nitric acid (1.42) 24 fl. oz./gal
sodium, potassium or ammonium acid fluoride 2 opg
balance is water (preferably steam condensate or ion exchange instead of tap)
temperature 70 - 140 °F
Temperature is usually 70 - 90 °F for sand & permanent mold castings, 120 - 140 °F for diecastings. Dowmetal H would be a sand or pm casting. Immersion time is 0.5 - 2 minutes.
- Michigan
Q. What method of precleaning is needed for my magnesium alloy? The parts were manufactured about 60 years ago and were just recently bead blasted by someone. They do not look like they are corroded.
1. Will blasting peen over the metal and cause corrosion to be covered up (can I verify this by looking under a scope)?
2. Did blasting remove the original Chrome pickle process or harm the precleaning since nothing was done prior to blasting?
3. I am going to use the Dow 1 process and then paint with epoxy, what should I do to prep the part with the above mentioned situation?
Aircraft Restorations - Pittsburgh, Pennsylvania
2003
by Dow Chemical Co.
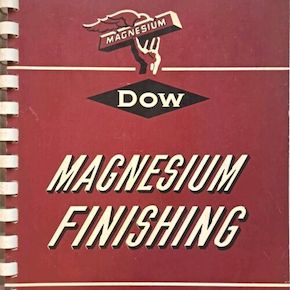
is sometimes available on
AbeBooks,
eBay, or
Amazon
... but if not, you can find libraries which have copies on WorldCat.org
(affil links)
A. John, the Dow process data I already sent to you specified the surface preparation.
Per Dow Magnesium, 1990, "Operations in Magnesium Finishing" Page 16, "Flow Chart of Chemical Treatment No. 1", The first step is Cleaning and they refer you to alkaline soak cleaning. If you only have one piece you may use powder dish washing compound then to make sure send your wife off shopping and run it thru the kitchen dishwasher.
The second step is Cold Water Rinse. Hold it under the outside water faucet until all the cleaning compound is flushed out of the blind holes.
The next step is the Chrome Pickle and you already have the formula. Small quantities of Sodium Dichromate and Nitric Acid should be available from any lab supply house in Pittsburgh.
Then you rinse again, and blow dry with a hair dryer ⇦ this on eBay or Amazon [affil links] .
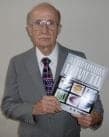
Robert H Probert
Robert H Probert Technical Services

Garner, North Carolina
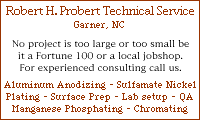
Q. Hello, My name is Matt and work for forging plant in the aerospace industry. We do sporadic runs of medium sized magnesium forgings. There was a span of about 6 years that we had no orders at all, and during that time all the people that were intimately familiar with the process left the company. So over the past year, we've really struggled with getting good adhesion of the dichromate. I've been looking for solutions and found some good information on your site.
We use what appears to be a variation of Dow #1 Type II for castings. I say "a variation", because our recipe calls for Sodium Bichromate, Nitric Acid and Magnesium. The standard practice for us has been to use solid mag chips created during the repair of the forgings to fulfill the mag requirement of the recipe. As you know Dow #1 type II calls for potassium or ammonium acid fluoride (whereas Dow #7 calls for calcium or magnesium fluoride, but no nitric acid). We also use use 10% nitric acid as the cleaning bath prior to dichromating.
The last titrated testing of the dichromate solution revealed that mag content was inconclusive due to other hydroxides being present, most likely aluminum chips. So my question is, what chemical should be used to replace the use of magnesium chips in the bath to prevent contamination from other alloys and other agents? Potassium or ammonium acid, calcium or magnesium fluoride?
Thanks in advance for your assistance.
- Akron, Ohio, USA
February 22, 2013

Q, A, or Comment on THIS thread -or- Start a NEW Thread