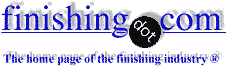
-----
Corrosion Protection processes for type 7050 Aluminum -- Akadize process?
Q. Good morning,
We are trying to determine which coating system would provide better resistance to general corrosion for a weapon system. The part is aluminum 7050, and the choices are anodizing alone (MIL-A-8625 / MIL-PRF-8625 [⇦ this spec on DLA]), vs. chemical conversion coating (MIL-C-5541) + primer TT-P-1757 [⇦ this spec on DLA] ) + topcoat paint (MIL-E-11195). I thought I heard something about anodizing being best for 7XXX alloys, for corrosion resistance.
Thanks for any information you can provide.
Marc PepiNAVAIR - China Lake, California, USA
2003
A. The corrosion resistance provided by anodizing is highly dependent on layer thickness, use of a sealing treatment, and presence of cracks/fissures/unsealed pores. For the aggressive environment that naval vessels/aircraft/etc. must face, a traditional protective system would comprise the following:
1. anodic treatment (chromic acid, sulfuric acid, etc.)
2. sealing with sodium dichromate
3. painting (primer + topcoat)
It is highly unlikely that an anodized layer alone could match the corrosion protection of the conversion coating + primer + topcoat. There is some data (Metalast website) that shows Type II anodic layer + sealing with Anoseal 1000 on 7075 produces salt spray resistance > 4000 hours. This is similar performance to conversion coating (MIL-C-5541) + primer (MIL-PRF-23377 [⇦ this spec on DLA]) + topcoat (MIL-PRF-85285 [link is to free spec spec at Defense Logistics Agency, dla.mil] ) as reported by Anderson & Webber (NAVAIR China Lake): http://dodconf.swri.org/2003Papers/Anderson.pdf
I'm not an expert in this area, so hopefully some others will reply with their knowledge.
Toby Padfield- Michigan
2003
! Thanks for the info, Toby!
Marc PepiNAVAIR - China Lake, California, USA
2003
You might also want to consider the Akadize process. Akadized components have withstood more than 1700 hours of continuous exposure to salt spray, suggesting a potential salt atmosphere life of 300 years. Akadized aluminum has an exceptional ability, also, to resist attack by corrosive gasses and liquids.
Linda Hughes- Santa Fe Springs, California
2003
Hi, Linda.
I see that you are with the supplier of this proprietary process. Please tell us basically what it is. Is it a proprietary anodizing process, a chromate-like conversion process, a PVD coating, a primer, or what? We work hard to keep this site technical and free of ads, and it gets hard to do that and keep it spam free if people post that their proprietary process may be the answer without telling us what their process involves :-)
Thanks!
Regards,
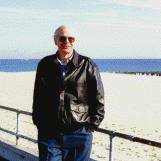
Ted Mooney, P.E.
Striving to live Aloha
finishing.com - Pine Beach, New Jersey
I need any information I can get on the finishing process for aluminum called Akadize.
Chris N [last name deleted for privacy by Editor]- San Marcos, California
2000
I am a Manufacturer's Representative for a company offering the Akadize process, which can give you superior aluminum qualities that should meet your needs.
Tim Reilly- Huntington Beach, California, USA
December 29, 2011
December 30, 2011
Hi, Tim. As you can see, we merged Chris' inquiry and your response into an existing similar thread to minimize duplication.
You say it "should meet your needs" although Chris hasn't yet said whether he needs a conductive or a non-conductive coating, so which is Akadize please? :-) Linda apparently didn't see my earlier request, but now that you have, please tell us the basics of what kind of process it is.
Is it conductive or non-conductive, especially applicable to type 7050 aluminum, RoHS compatible, for example? Can it be primed and painted? What are the dimensional implications, etc. This site is for camaraderie and public technical info exchange. Thanks!
Regards,
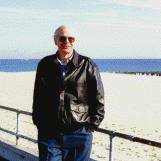
Ted Mooney, P.E.
Striving to live Aloha
finishing.com - Pine Beach, New Jersey
March 1, 2012
Below is some additional information on the Akadize process:
- It is an oxidizing process similar to anodizing, using a proprietary chemical solution combined with electrical current.
- Oxidation is denser and harder than anodized surface.
- Exceeds Mil-A-8625F requirements.
- Original trade name was "Banadize"
- Roots go back to the space program/NASA ~40 years
- Different alloys have slightly different reactions.
- Not compatible with powder coating or painting.
- Huntington Beach, California, USA
Tim,
Akadize, Banadize is compatible with painting.
- Santa Fe Springs, California USA
April 28, 2012
Q, A, or Comment on THIS thread -or- Start a NEW Thread