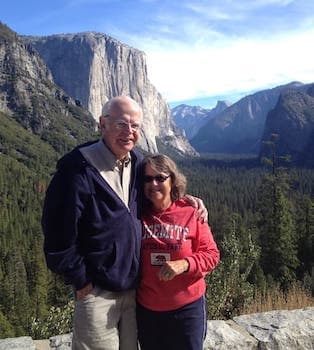
Curated with aloha by
Ted Mooney, P.E. RET
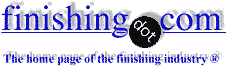
The authoritative public forum
for Metal Finishing 1989-2025
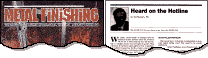
-----
Tin Plating Problems: black spots in random locations
Q. I found some black spots as group in acid-based tin plating process using barrel method. Distance between black spots approximately 0.1 mm. May I know the reason for black spots? I suspect soaking process while cleaning copper alloys due to oil contamination. Oil dirts are not cleaned properly. What is method to validate degreasing process? I Checked density flow thermometer to validate density of soap cleaning method. Any other suggestions please to resolve this black spots issue ?
ThamizhinianEmployee - India
November 24, 2024
⇩ Related postings, oldest first ⇩
Q. We are tin plating brass sheet with a nickel undercoat. These parts go through a DI water wash prior to shipment. We have seen black spots appearing in random locations on the part. Any ideas as to what this may be? Thanks for any responses.
K Link- Little Rock, Arkansas
2003
A. Hello K. In addition to plating problems, "tin fretting" can be caused by mechanical jostling of parts together, and it produces black spots. Do you see these spots happen before any such jostling?
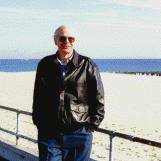
Ted Mooney, P.E.
Striving to live Aloha
finishing.com - Pine Beach, New Jersey
Q. These spots seem to form in the presence of water with no motion.
K Link [returning]- Arkansas
A. Dear Sir:
What you have is plating bath contamination.
Joel Garcia- McAllen Texas.
A. How thick is your nickel undercoat? If it is less than 5 microns, it could be porous, thus exposing the brass substrate to any post-nickel treatments. Are you using an acid or alkali tin plating bath? This could make a difference. Do you melt the tin to brighten it or deliver it as plated? If you are heat melting it and you have porous nickel, you could well be forming a copper-tin intermetallic in the pores and this will be a dark colour. I presume you put the nickel down as a barrier layer to prevent migration of the tin into the brass and this is enhanced by elevated temperatures, so is there any connection here? Pretreatments to the nickel could cause attack on the brass. Does your process have any sulfides or sulphites that could attack either the copper or the nickel to produce dark sulfides? I hope these suggestions may stimulate some thought for you.
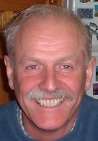
Trevor Crichton
R&D practical scientist
Chesham, Bucks, UK
Tin plating turns yellow with time, and blackens when heated
Q. Dear Sir,
We have had problem at the surface of a tin plate. When heat at about 200 °C is introduced to the surface, it will turn black and not shiny. Besides, it also turns yellow by just leaving it for a few months. I would like to know what are the possibilities that cause this to happen? Thanks in advance.
Best regards,
Lau Lai Kuan- Ipoh, Perak, Malaysia
2003
A. Heating tinplate is not a good idea once it has been flow melted. Tin melts at 232 °C; you are very close to it melting. Furthermore, tin diffuses into the base steel in tinplate to form a black alloy (FeSn2). Whilst there is some free tin available, the only alloy formed is FeSn2, but once all the tin reservoir has been used, you can get a range of alloys (FeSn, Fe2Sn3, Fe3Sn2). The rate of diffusion is relatively slow, but above its melting point, the tin goes in much faster. The rate of diffusion follows Fick's 3rd law of diffusion. I reckon you are using a very thin layer of tin on the base steel and allowing it to remain at this high temperature for too long. By the way, this alloying process is very important in generating the corrosion resistance that is normally associated with tinplate. The yellowing of the tin is probably due to oxidation of the tin.
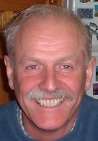
Trevor Crichton
R&D practical scientist
Chesham, Bucks, UK
Q. We are exporter of Engine Components manufactured from Steel with one side coating of copper alloy i.e. Cu 80%, Sn 10% , Pb 10%. After plating the component our product gets tarnished from inside i.e. alloy side. We need a very very thin coating which is drying, colourless, and retain the tin plating finish for about 1 year. We don't want to apply any oil which gives wet finish. We need a product which has the properties of repelling the water.
Neeraj MaheshwariManufacturer of Auto Parts - Agra, Uttar Pradesh, India
2004
A. Hi Neeraj. There are benzotriazole ⇦ this on eBay or Amazon [affil links] based tarnish inhibitors for copper, and chromate based tarnish inhibitors for tin, which would be almost immeasurably thin.
One well known brand name is Tarniban from Technic.
Unfortunately, your problem is not quite clear to me. This object is first plated on one side with a Cu-Sn-Pb alloy? Then both sides are tin plated and the the Cu-Sn-Pb alloy side starts tarnishing? Or is just one side (the inside?) plated at all and you are unconcerned with the bare steel side?
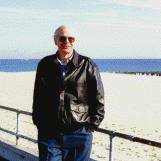
Ted Mooney, P.E.
Striving to live Aloha
finishing.com - Pine Beach, New Jersey
Q. Hi I'm Sandesh ,
We are Manufacturing & supplying Heat Sinks for reputed electronic companies.
We are facing problems of Black spots on our tin coated components & are not getting soldered.
We have got thousands of rejected components because of Black Stains.
How to rework these pieces ?
Kindly some one help on this regard.
manufacturers of heat sinks for electronics - Bangalore, Karnataka, India
2004
A. It sounds like excessive brightener. Get your supplier involved. In the meantime, use a dip in alkaline cleaner after tin plate. Another possibility is copper contamination of the tin bath, and a third possibility is filthy rinse water.
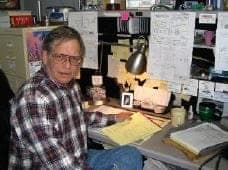
Jeffrey Holmes, CEF
Spartanburg, South Carolina
A. Mr Sandesh. Tell us more about the materiel you plate tin on. If it is copper you must use a nickel layer first then tin because of the diffusion between copper and tin.
Regards
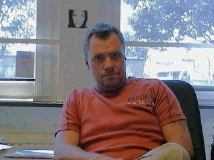
Anders Sundman
4th Generation Surface Engineering
Consultant - Arvika,
Sweden
Anders is correct. You must give more details of what you are plating and how. The Internet is a wonderful thing, but as far as I know it has not yet been able to achieve telepathy or mind reading. Tin will migrate into lots of different metals, including copper and iron. Anders has described the problem with copper; the problem with iron is that it forms a dark grey alloy that becomes more apparent when the tinplate is heated.
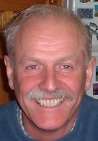
Trevor Crichton
R&D practical scientist
Chesham, Bucks, UK
You can also use copper as a barrier coat.
Chris Snyderplater - Charlotte, North Carolina

this text gets replaced with bannerText
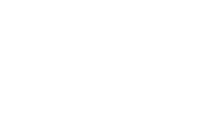
Q, A, or Comment on THIS thread -or- Start a NEW Thread