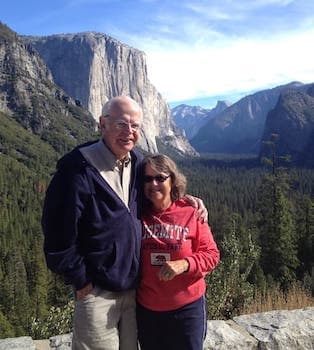
Curated with aloha by
Ted Mooney, P.E. RET
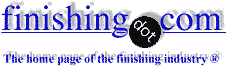
The authoritative public forum
for Metal Finishing 1989-2025
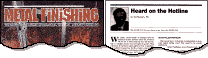
-----
Premature 304 SS diesel fuel tank failure
We have been building stainless steel fuel tanks in-house for over three years. Recently, we had a couple of occurrences of tanks rupturing near welds holding baffle platers to the tank sides/bottoms. We had been using 304 plate with 308L electrodes (SAW). The tanks are well secured and do not flex. Is there a possibility that the tanks are cracking because of the weld (it. too much heat, improper electrode, etc.), or because the welds were not passivated? Also, we have been using the same tank material with 316 wire (GNAW) for the past two years or so. The welds are very dark. Is this an indication that the welds should be passivated? Where the baffles are stitch-welded to the sides/bottoms, one can see deformation of the .125" tank material due to heat. Would one normally expect to see this - is the heat too high?
Randy Guimond, CUTa boat mfgr. - Escuminac, New Brunswick, Canada
2003
It sounds like you could have a few problems occurring here.
First, you always should passivate any stainless steel welds or you are asking for difficulties in any humid or corrosive environment. The weld is always the weakest area (corrosion-wise) due to a complete change in the alloy in the heat affected zone.
Second, it sounds like you probably have a differential expansion problem in the weld area, but you need to go to a welding consultant about that.
Third, you state that you made a couple changes in the way you weld the tanks. You need to go back to what you know works. Have you changed the source of the steel? There is quite a bit of questionable steel that we are hearing about coming from some areas of the world.
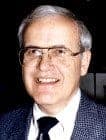

Lee Kremer
Stellar Solutions, Inc.

McHenry, Illinois
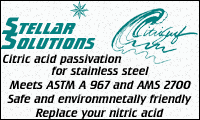
2003
Corrosion and ultimate failure at weld areas is quite common. Make sure mating metals are free of oil before welding, consider belt polishing weld areas and then electro-polish to remove sub-surface contamination. You should see significant improvement. If these tanks are large and complex, consider welding some test samples and subjecting to salt spray testing to compare.
Also consider a higher grade material such as 316 SS if it meets other metalworking characteristics you need.
- Chicago, Illinois, USA
2003
My guess is you have a stress problem. You can relieve it with heat treat or by electropolishing. Deformation near the welds would indicate you are introducing stresses that should not be there.
Dan Weaver- Toccoa, Georgia
2003
Get your electrodes tested, the chemistry could be a bit screwy. It is also possible that the ferrite content of the weld pool is too low (less than ~3%) which can promote hot cracking of the weld during cooling.
Low ferrites usually can occur as the result of undesirable welding parameters or insufficient ferrite forming alloying additions in your consumable.
Probably best to send it into a metallurgist to do a failure analysis on it.
He or she should be able to give you a root cause of failure.
- Roxby Downs
2003
Q, A, or Comment on THIS thread -or- Start a NEW Thread