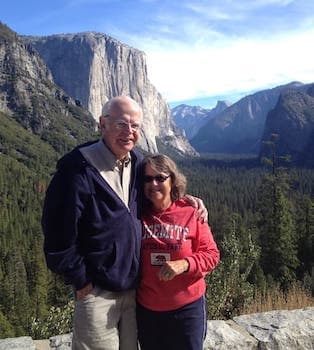
Curated with aloha by
Ted Mooney, P.E. RET
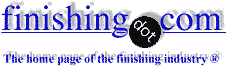
The authoritative public forum
for Metal Finishing 1989-2025
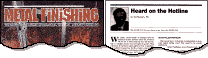
-----
Plastic tank welding, tips
2003
I wish to build my own chemical tanks for processing PCBs. The tanks will be small (25 liters) compared to standard industrial sizes and used for basic operations such as acid copper plating, alkaline cleaning, through hole metallization, and copper etching. I own a Leister hot air welding tool and have plenty stock of 1/8" and 1/4" PVC sheet, plus triangular welding rod.
Would anyone recommend the best way to start learning how to weld PVC for DIY tank building ? Of the several hours or so I have played around it sure showed me how far away I am from doing anything looking like a professional weld seam, especially in tight corners. I have the patience and interested in learning some of the skill.
My second question relates to temperature rating of standard PVC tanks. The maximum temperature I will encounter is 55° C (131° F). Can PVC survive this temperature or will this require polypropylene ? I've been told PP is more difficult to weld than PVC using manual hot air tools so I wonder if anyone will recommend me against building tanks from PP.
- Melbourne, VIC, AUSTRALIA
2003
Adam,
First of all, I'd go to the local library and see if they have or can get some books on welding thermoplastics.
Then try LARAMY. They, too, have welding guns BUT they also have a super little booklet on welding. I believe that you can buy it from them.
That 131° C is getting too close to PVC's max 140° F ... you could just get away with it if the tanks were well made (and had reinforcers in the right places)
But wherever possible, BEND, don't weld. See the archives for # 8169, perhaps #8691 and #11097.
Lastly I'd consider using a MOULDED Pe tank which is supposedly good for 150° F ... where there are no stresses!
Welding is an art. I'd think that welding PVC is much harder than welding Pe or PP. With the latter, many people just use the speed tip but with PVC you'd have to much more careful using a speed tip.
Lastly, with any thermoplastic welding, the most important bead (weld) is the first one, the so-called root bead, normally made using 1/8" dia rod because, as you might know, you normally should have about a 1/l6" gap between the sheets when welding ... thereafter one uses a heavier bead, say 3/l6 ... I've seen extruder welders uses which put on around 3/8" weld bead in one pass ... but the root bead comes first.
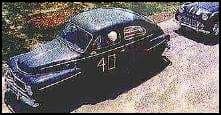
Freeman Newton [deceased]
(It is our sad duty to advise that Freeman passed away
April 21, 2012. R.I.P. old friend).
Q, A, or Comment on THIS thread -or- Start a NEW Thread