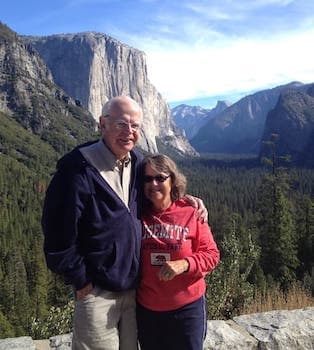
Curated with aloha by
Ted Mooney, P.E. RET
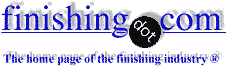
The authoritative public forum
for Metal Finishing 1989-2025
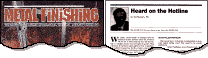
-----
Low friction finish for steel auger in sand
2003
Have an application where will have an auger blade slowly moving in sand. Looking for a very low friction coating, which is also highly abrasion resistant. I'd prefer to use a low carbon steel blade
(low cost), with some finishing or coating. We have tried this in the lab with a dry film lubricant over a polished piece of steel - the lubricant quickly wore off, and sand starting sticking to the steel, which resulted in high friction forces.
Thanks for your help,
- Springfield, Virginia
Some people feel that everything is going to be coated with diamond-like carbon one day, so your study should include that
(although you'll probably find that it costs 100x too much). Vapor-deposited chromium nitride or maybe titanium nitride are possibilities, as is electroless nickel with diamond particles. But in the end, I think you'll find that the sand is so abrasive, so tough on the auger, that no matter what you coat them with it won't last long, and you'll do one of two things: plan on frequent recoating with rather thick hard chrome plating because it's practical and inexpensive and low friction, or figure out how to live with the higher friction of plain low carbon steel.
That my two cents worth. But maybe we'll hear from someone who actually knows what they're talking about :-)
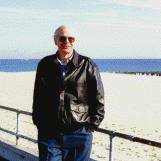
Ted Mooney, P.E.
Striving to live Aloha
finishing.com - Pine Beach, New Jersey
2003
Sorry to disappoint Ted, but just another opinion from the peanut gallery... Have you investigated thermal spray coatings like tungsten carbide? The tungsten carbide particles are usually deposited with a nickel or cobalt binder, and the coating is quite hard and wear resistant. The US military is investigating these types of coatings to replace hard chromium, due to environmental concerns.
Toby Padfield- Michigan
2003
Correction: I meant to say low alloy carbon steel, not low carbon steel, since heat treating by carburization or similar process has been done on somewhat similar applications (oil drilling bits, etc.).
The point is, and I think Guillermo Maruffo previously made it while talking about a different application, that hardening can extend to a greater depth than practical coating thicknesses, so sometimes just hardened steel will outwear an exotic finish.
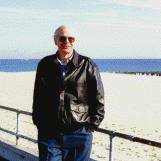
Ted Mooney, P.E.
Striving to live Aloha
finishing.com - Pine Beach, New Jersey
2003
First of two simultaneous responses --
Toby,
I considered that also, but I do not think that it will have the level of smoothness that he appears to need. HVOF or the detonation process might work and would be more robust than a high energy plasma coating. It would be worth a try. It might require a lot of hand grinder time to polish it out. Eventually, the sand will do the deed.
- Navarre, Florida
2003
Second of two simultaneous responses --
Am I missing something? Why not hard chrome? Shotpeen steel first to give compressive stressed layer.
Jon Quirt- Minneapolis, Minnesota
2003
Thanks for the quote Ted. Indeed, dimensional and geometry control certainly are the clue here. If he needs to tightly keep a certain thickness, width, angle or whatever, little advantage will he find in a thick coating or deep hard case treatment and thin coatings will soon surrender no matter how hard. On the other hand if he can live with, say 0.005"-0.010" or even more of wear, then probably a thru hardened D-2 blade can make it. Another possibility would be to braze solid tungsten carbide inserts over the edge, pretty much like concrete drill bits.
Guillermo MarrufoMonterrey, NL, Mexico
2003
Thermo-diffusion zinc galvanizing has a very hard surface (3400MPA) due to zinc-ferrum alloy which is formed in the diffusion process. Also the coating is very uniform and is used for corrosion protection of precise laser cut plates which are assembled to 4 wheel-drive with no requirement for hand grinding of holes practiced in hot dip galvanizing. The diffusion cause deep penetration of coating into surface layer with no spalling of coating in operation.
Zvi Lahat- Israel
2003
Q, A, or Comment on THIS thread -or- Start a NEW Thread