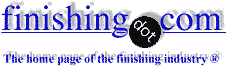
-----
Selection of steel for nitriding
Dear Sirs, Please let me know what steel to be selected for nitriding (EN-42,42B or SS) In a spinning ring, a wire piece called traveller of hardness 630 Hv works at 45 mts/sec. To reduce friction between ring and traveller, the rings are nitrided. Because of the difference in hardness between core and surface of the steel, the ring gets worn out soon. In fact the life of the ring is expected at least 4 years of continuous working.
To reduce the hardness difference between core and surface, we did hardening of basic steel and nitrided. but after nitriding the core lost its hardening as it got annealed while nitriding.How to achieve nitrided surface hardness at 1000Hv and core harness at highest possible so that nitrided surface can withstand constant hammering by traveller. regards sukumar
- coimbatore, Tamilnadu, India
2003
Alloy selection is not necessarily the problem. You can investigate lower temperature nitriding processes, such as plasma (ion) nitriding. These processes can be performed at temperatures as low as 375 C. Having said that, you must select an alloy that can be tempered at a high enough temperature so that hardness is not adversely affected by the nitriding process. EN42 can be tempered above 400 °C and still maintain adequate hardness. Have you investigated other coatings and alloys? Tool steels (D2, D3, A2) with low friction coatings like TiAlN, diamond like coatings (DLC), etc. will have superior core hardness and surface hardness.
Toby Padfield- Michigan
2003
Electroless nickel composites with either diamond or hard particles over a hardened substrate (AISI D2 OR D3) seem to be a good candidate.
Guillermo MarrufoMonterrey, NL, Mexico
2003
Q, A, or Comment on THIS thread -or- Start a NEW Thread