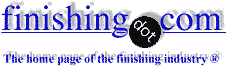
-----
Plating Copper for high temperature use
Hi, I need to cover a copper heater plate with some kind of protective plating to keep it from oxidizing and falling apart on me. This piece will be operated up to 600 degrees C (over 1000 F) for hundreds of hours at a time.I have heard that a nickel plate is a good idea.
Can anyone tell me if this is correct? Does it have to be electrolytic or electroless? How thick a plating is required? What will happen to the nickel plating over time at these temperatures - will it turn black or will it also disintegrate? Should I consider any other type of plating (don't think I can afford gold!)
- st. paul, minnesota, usa
2003
Electrolytic nickel from a modified Watts bath is the coating of choice for the copper plates used in molds for continuous casting of steel. It outperforms chrome in that application up to 10 times. Its coefficient of thermal expansion, ductility, low internal stress and chemical inertness is ideal at temperatures of up to 1550 °C. Obviously, the plates are huge and the coating is sometimes as thick as 0.250". You probably need no more than 0.002 or 0.003". A final topcoat of decorative chrome will protect the nickel from tarnishing in air.
Guillermo MarrufoMonterrey, NL, Mexico
2003
Nickel plating is correct. I suggest sulfamate nickel solution because it will result in the lowest possible stress and the greatest ductility, equaling copper. So that the difference in thermal expansion takes place no damage will be done, i.e. no cracking of the deposit. a chromium flash is also a good suggestion. sulfamate nickel requires sulfur depolarized anodes and a large anode area. follow the instructions of the supplier.
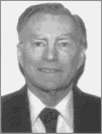
Don Baudrand
Consultant - Poulsbo, Washington
(Don is co-author of "Plating on Plastics" [on Amazon or AbeBooks affil links]
and "Plating ABS Plastics" [on Amazon or eBay or AbeBooks affil links])
2003
Ignoring cost, would there be any performance advantage to using a gold top-coat or is chrome still the way to go for an application like this?
Cristobal Bedoya- Boston, Massachusetts, USA
May 17, 2011
Hi, Cristobal. It probably depends on the exact meaning of "like this" :-)
Gold has tremendous chemical resistance, far greater than chrome, but it is neither as hard nor as slippery. Gold can diffuse into (alloy with) other metals like copper, especially at high temperatures, thus losing the properties of gold.
Regards,
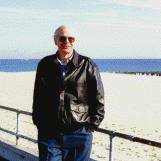
Ted Mooney, P.E.
Striving to live Aloha
finishing.com - Pine Beach, New Jersey
May 17, 2011
Q, A, or Comment on THIS thread -or- Start a NEW Thread