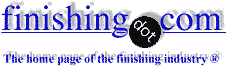
-----
Is the chromic acid rinse necessary for phosphate coating?
We are currently performing Zinc and Manganese Phosphate coating threads to prevent galling. My question is if the final chromic acid rinse is necessary for my application or can I just do a final rinse with fresh water.
Josh Bourgeois- LAFAYETTE, LOUISIANA, U.S
2003
Final chromic acid rinses are obviously of some value; people would not have used them for decades if they weren't. But I think it's fair to say that while iron phosphate desperately needs a chromic final rinse or equivalent, it is much less of an issue with zinc and manganese phosphate, and that it's quite possible that a DI final rinse will suit your needs, especially if you can dip the parts in water soluble oil.
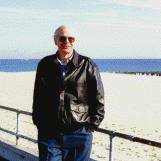
Ted Mooney, P.E.
Striving to live Aloha
finishing.com - Pine Beach, New Jersey
2003
And you are not phosphating to a specification.
James Watts- Navarre, Florida
2003
First of two simultaneous responses --
Phosphate coatings form as crystals on the surface of the substrate. Sometimes there tiny pits or holes where the crystals have not covered. The purpose of the chrome is to act as a sealer. Under controlled conditions, salt spray, the addition of the chrome gives twice or more hours of corrosion protection.
Ronald ZeemanContinuous Colour Coat - Brampton, ON, Canada
2003
Second of two simultaneous responses -- 2003
From the look of your address and the nature of your question, are you phosphating OCTG (oilfield threads like couplers pin ends and ancillaries). Or have I put 2 and 2 together and got 5 (has been known). If you are phosphating OCTG gear, generally all the specifications I have on file such as VAM, TENARIS, FOX etc, do not require a chrome rinse.
Though the best thing would be to ask your customer for a copy of the spec or the relevant spec no.
Regards,
- Lowestoft, U.K.
The chromic acid rinse is highly suggested to use depending on your specific application. The final chromated rinse serves 3 important functions.
1. it serves as a temporary rust preventer for short term storage.
2. it dries the part very fast, much faster than any hot water rinse.
3. it makes the surface of the part slightly acidic, which is the best situation for the adhesion of paint bonding, if thats what you plan on doing. in order for it to work correctly, you only need a very small amount for it to work. (i.e. 1 pint(5% solution)) for every 400 gallons)staining may occur if you have the temp too high. you should go as low as possible w/out impeding drying. 160F is a good temp.
- Nanticoke, Pennsylvania, USA
2003
Hi Joel, Regarding your Point #2, can you explain why a part treated with a chromic acid rinse would dry more quickly than one rinsed with water? I've never heard of a such a thing. I would think that speed of drying would be mostly dependent on the temperature of the rinse.
George Gorecki- Naperville, Illinois
2003
I have heard that there are products that can be used instead of chromic rinse baths, with the same purpose and final performance, but with less danger both to personnel and environment. Can any of you suggest some of this products?
Manuel Pindado- Madrid, Spain
2003
We cannot print recommendations of specific proprietary products here, but most metal finishing process suppliers offer them. They are common enough that you can simply ask for a "chrome-free final rinse" and everyone will know what you are talking about. Hopefully some of our advertisers will contact you about their offerings.
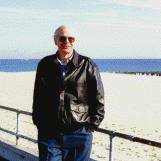
Ted Mooney, P.E.
Striving to live Aloha
finishing.com - Pine Beach, New Jersey
2003
Q, A, or Comment on THIS thread -or- Start a NEW Thread