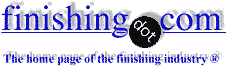
-----
Sulphate formation from selective plate of tin over copper
Help!
My company is using a selectively plated tin/copper strip. Half of the strip is bare copper. The other half is tin plated over copper. We are having trouble welding the copper half. After analysis, there seems to be a little bit of oxide, but more importantly there seems to be a "thick" copper sulphate ⇦ on eBay or Amazon [affil links] layer (50 Angstroms). Does it make sense that the sulphate layer would cause the welding problems? Also, the plating process uses MSA as the activator, could this be the source of of the sulfur for the sulphate formation? Is there another way to plate the tin without causing sulphates to form on the copper side?
Matt Stevens- Cambridge, Ontario, Canada
2003
copper sulphate is quite soluble in water. As you described it, it should be zero problem to put a bunch of them in a plastic pail, fill it to the top with a good grade of DI water. The next morning, empty the bucket, blow the parts off with clean oil-less air and use them.
I was not aware that you could weld copper. Traditionally it is brazed or soldered. For solder, the oxide of copper is removed with flux or abraded or it is difficult to solder. Brazing should care less and welding should care even less.(if possible)
James Watts- Navarre, Florida
2003
First of two simultaneous responses --
I am not sure what you are actually doing; what are you welding together, two bits of tin plated copper?. Technically, welding is the localised melting of two or more metal components to join them together. Brazing uses a lower melting point metal (or alloy) to join two or more pieces of metal together, whilst soldering is really a lower temperature version of soldering. Both brazing and welding are susceptible to surface cleanliness, but welding can tolerate quite high surface contamination because both the metals are usually melted by a high temperature (Just think of welding a supertanker together!). A "thick" layer of sulphate (50 Angstroms) in reality is not very thick - it is typically about 15-20 atoms thick. This will almost certainly not be continuous. Hence I am not convinced that the 50A layer of copper sulphate is the main source of your problem, but it is a symptom. Clearly there is an issue with sulfur and oxygen being present, but I wonder how you ! analysed such thin layers - I suspect you have used Auger, or something similar. I just wonder if you have a solder or braze wetting problem due to inadequate cleaning. This can be overcome by a good anodic clean in 10% sulfuric acid, or even a simple abrasive cleaner. There are numerous fluxes available for brazing and soldering and lots of solders have built-in fluxes. If I have got the wrong end of the stick regarding this problem, I apologise, but perhaps more operational detail is required.
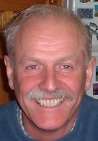
Trevor Crichton
R&D practical scientist
Chesham, Bucks, UK
2003
Second of two simultaneous responses -- 2003
Sounds like you are tack-welding or splice-welding TO strip off a reel. Anyway, the copper sulphate must be forming up on the copper due to a really bad post process rinse step. 50 Angstrom is sparingly thin, most tack welders can punch through that easy, and arc-type splice welders certainly can. But to test this theory, emery-cloth burnish the surfaces and alcohol wipe them prior to weld to see if a surface contaminant is actually the problem. If so, then its definitely poor rinsing & poor post treatment. Usually these processes exit the Tin plater, DI rinse, light back-etch to remove thin mask bleed, rinse, then wet right into an anti-tarnish dip, DI rinse, and hot air dry. Any one of these processes could cause post-process corrosion. I used to use a trick that worked very well. I ran the bare copper raw material through an anti-immersion process (Lea-Ronal) normally used right before a silver spot plating process. Just put it into one of the empty tanks before the Tin bath but after the activator baths. Tin plates out fine and the copper never tarnishes, even on a hot-plate test.
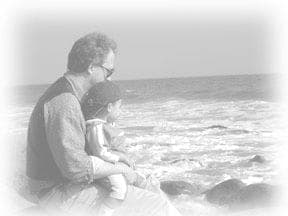
Dave Kinghorn
Chemical Engineer
SUNNYvale, California
Hello folks,
Thank you very much for your feedback. To answer the questions, these strips are formed and overmolded and then the copper "windows" are ultrasonically welded to thin copper strips. Since the copper thickness is very thin, it does allow easily (usually) to this form of welding. All in all, I think we have found a solution to reduced the sulphate contamination and it seems to be solving the issue. What we have done is added a rinse/pickle step in the plating process after the plating.
Thanks again for all your input.
Matt Stevens- Cambridge, Ontario, Canada
2003
Q, A, or Comment on THIS thread -or- Start a NEW Thread