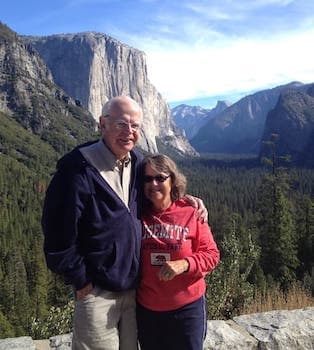
Curated with aloha by
Ted Mooney, P.E. RET
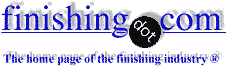
The authoritative public forum
for Metal Finishing 1989-2025
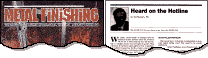
-----
EN deposition on cast iron
I am trying to electroless nickel plate cast iron. Although thorough sand blasting had been done before coating, the coated part still cannot survive more than 2 hours of humidity test (40C, 90%RH). Would like to know if there are any way to improve the corrosive resistance. However, the electrical conductivity have to be retained.
Julia Chow- Kwai Hing, NT, China
2003
2003
Julia,
Please see if the pretreat cycle can be improved with a Dilute Sulfuric 10 percnt dip for 1 to 2 minutes followed by rinsing before EN.
Check the EN bath for speed and ensure you get sufficient thickness. Check your plating standard and stay close to the prescribed thickness level.
Check the porosity of the deposit by dipping ij copper sulphate ⇦ this on eBay or Amazon [affil links] solution after plating.
If there is porosity ensure you make up a new bath and check the results same way FIRST.
I hope this helps. Regards.
No red spots means there is no porosity.
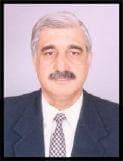
Asif Nurie [deceased]
- New Delhi, India
With deep regret we sadly advise that Asif passed away on Jan 24, 2016
Sounds like the EN is too thin and is still porous and/or discontinuous. Try putting a thicker coating down. It would help if you gave us more information about your current process, then we don't need to guess.
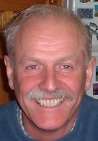
Trevor Crichton
R&D practical scientist
Chesham, Bucks, UK
2003
Dear Mr. Nurie and Mr. Chrichton,
Thanks for kind advise. I was coating to thickness 10~15 microns and check thickness every time on dummy with the run. Here is my pretreatment process : Solvent degrease, alkaline clean at around 60C by soaking ~3 minutes + ultrasonic degrease 2 min, Acid dip ~2 min. Rinsing between process and acid/alkaline are commercial products. Please kindly comment and recommend improvement.
Best regards,
Julia Chow- China
2003
Certainly 2 Hrs is very low for an EN plated part. Hopefully you can solve the problem by increasing the thickness. If not, consider an underplate of acid copper over a suitable protection strike (alkaline copper or nickel). Acid copper deposits have excellent microthrowing power and will easily cover up or "bridge" pores, small inclusions and free graphite.
Guillermo MarrufoMonterrey, NL, Mexico
2003
15um of electroless nickel should be adequate, so it looks like the problem is a discontinuous coating caused by pores and/or inclusions. Good cleaning is essential and I would suggest anodic etching in 30% sulfuric acid. This will cause a carbon smut that must be removed by keeping the etching going whilst oxygen is produced. This will leave the surafce clean and hopefully contamination free. If the cast iron is very porous, you may benefit from a low cyanide copper plating, although generally electroless nickel should cope with this problem.
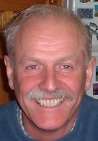
Trevor Crichton
R&D practical scientist
Chesham, Bucks, UK
2003
2003
Dear Julia,
You can perform the Ferroxyl Test for Fe based substrates.
25g potassium_ferricyanide
[affil links].
15g Sodium Chloride.
Make up to one litre with DI water.
Clean the part and immerse for 30 seconds. Pores in the EN deposit will show as blue spots.
Some questions that spring to mind are:
1. How many MTO has the solution done.
2. What is the P content of deposit.
Personally, I'm always inclined to pickle for as short a period as possible with cast materials. My feeling is if you over pickle, carbon (as graphite) can sit on the surface and stop deposition. This can be very difficult to remove from pores already in the substrate.
Jonathan Timms- Hong Kong
Q, A, or Comment on THIS thread -or- Start a NEW Thread