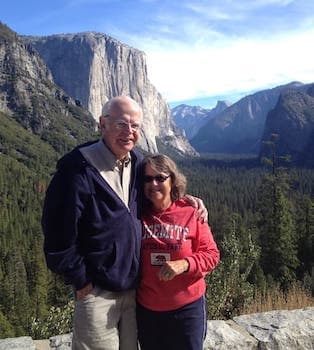
Curated with aloha by
Ted Mooney, P.E. RET
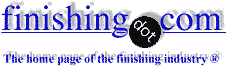
The authoritative public forum
for Metal Finishing 1989-2025
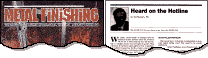
-----
Phosphated Steel Finish Quality
Do any test methods and standards exist for specifying the quality of phosphate finishes? In particular, the amount of excess chemical residue and cleanliness of the treated surface. The current finish on a 1018 CRS mechanical component is too gummy and uneven for its use as a low friction sliding surface, but the phosphate is needed as a paint preparation for the other cosmetic surfaces. Would zinc, iron , or another phosphate be preferable in trying to achieve a slick surface that also adheres to paint well? Also, how the above perform as a substrate for molybdenum disulfide dry-film lubricant?
Brian TremblayOhmeda Medical
1998
The answers to your first two questions are yes and yes, but that does not get to the answer that you are looking for, I think. Zinc phosphate is a crystalline coating and can be rather heavy depending upon the application variables. Iron phosphate is an amorphous light coating that is excellent for most non-corrosion critical applications. (i.e. office furniture and such...) Iron phosphate should perform fine with the lubricant on the non coated areas. Although, zinc phosphate is used as a break in lubricant for many cold forming and manganese phosphate as a break in lubricant for gears and such, they are not used on many "truly cosmetic" parts, unless the coating thickness applies will absorb their surface profiles or inconjunction with a multiple coat system like powder coating over e-coat.
The real question you need to have answered is will it perform well enough under the paint to meet the corrosion requirements that the coating must provide.
What are your paint performance requirements?


Craig Burkart
- Naperville, Illinois
1998
1998
A calcium modified zinc phosphate is quite uniform and is a good paint base. There are a lot of different molydisulfide (dry film lube) types from no bake to relatively high temp bake. Moly disulfide is an excellent lubricant. It is not permanent in a high use application. Phosphate is an excellent base for both the paint and the dry film lube.
Phosphate is an unusual process.It works best when it is worked hardest, assuming that you can keep the temperature up and that periodic additions are made. For truly bad results, make a run in the morning and one on the pm shift on a regular basis.
If you have chemical residue, it is not being rinsed adequately.
Even 1018 needs to be grit blasted. If you are pickling, there is a Ti additive for the rinse, but this is just another portion of the process to maintain or it will go bad and give bad results.
James Watts- Navarre, Florida
Q, A, or Comment on THIS thread -or- Start a NEW Thread