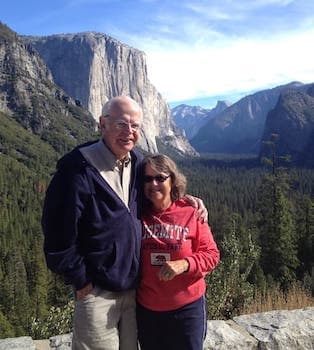
Curated with aloha by
Ted Mooney, P.E. RET
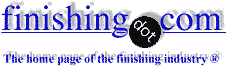
The authoritative public forum
for Metal Finishing 1989-2025
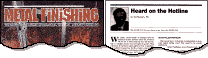
-----
Experiencing a color shift when sealing anodized parts
We experienced from batch to batch a color shift during the sealing process. We use a nickel sealing salt at 96 C with pH at about 5.8. This black dye used is from Japan at a low concentration to produce a titanium shade. We do not have problems on dyeing but when it comes to seal problem starts there. Anybody has experience on such a problem and what are the reasons? What should we do to improve the situation?
S. Y. Yuen- Hong Kong, China
1998
there are a number of things that can cause leaching of dye into a nickel acetate sealing bath. if your seal bath contains a surfactant (and it probably does if it is a commercially available product) then this is a likely culprit. check with your supplier on this issue.
it is important to keep in mind that nickel salts will always leach some amount of dye from your parts. maintaining a proper coating thickness and dye bath chemistry will help eliminate differences between one batch and another. and finally, the dye you are using is not designed to deliver the color you want. using a lower dye concentration will cause inconsistencies in the color that are not visible until after the part has been dried, and these inconsistencies may be independent of your seal bath. I would suggest you try a dye or dye combination designed to deliver the color you are after. contact Clariant Corp. in Charlotte, SC (or is it NC?) as they are the leader in dye manufacturing for anodized aluminum.
Gerald Janssen-coil anodizing - Streamwood, Illinois, USA
1998
Color matching is difficult, and requires very good process control of the anodizing process to start with because small changes in concentration of the electrolyte, temperature and current density, as well as ramp rate parameters affect the anodic pore dimensions and thickness. Then one needs to work with the customer to develop two samples which reflect the acceptable range of color. One sample is a light sample and one a dark sample and anything between the two is acceptable. Of Course both the process house and the customer have a set of these samples. That said, because the dye bath and the seal work in combination, with color impregnated and color leached out, usually a beginning production run of the day will be used to determine both the times in the dye and in the seal. Those times will change sometimes hourly, and when very critical appearance dye parts are to be run, the dye and seal times may need to be established from batch to batch! Naturally, both the dye bath and seal parameters need to be maintained very tightly.
Ward Barcafer, CEFaerospace - Wichita, Kansas
1998
1998
Mr. Janssen and Mr. Barcafer have stressed very important points, which many of us have learned through experience, and I believe the root problem is trying to dye parts grey with a dye that is designed for black (assuming that titanium refers to a metallic grey color.)
Experienced color matchers know this, but here is a factor to consider in case you are a novice- the proverbial comparing apples to apples. When you say you have no problems with the dye, I hope you are comparing apples to apples, that is, comparing wet parts to a wet standard, or dry parts to a dry standard. The water on parts as they leave the dye rinse will make the parts darker than they will look when dry, especially if the parts have a matte finish. It's basic optical physics where the water turns normally refracted (scattered) light into reflected light from a glossy surface.
Checking the actual in-process color vs. your color standard(s) can be done in two ways: several shops I have been in take an air hose and blow-dry a part or small section of a large part to check color vs.standards. Naturally the blow-off air must be completely oil-free. The other way is to compare two wet surfaces. A well-sealed color standard may not wet very well, plus the constant wetting can eventually change the color of the standard. I used to get around that by applying a water-white clear lacquer to half of one surface of my color standards. The lacquered surface has the color of a wet part. You may later need to worry about yellowing of the lacquer, but color standards need to be retired periodically for new ones anyway.
Another factor in matching colors: it goes without saying to do the color matching in a well lit area, but also consider that the color match should be done under the same light conditions as the lighting conditions where your customer will be looking at the parts. Colors can match under fluorescent lights, but can look different under incandescent or natural lighting. A prime example of this phenomenon is the color comparison between the old integral colored anodize and two-step electrolytic colored anodize. When the two-step process first broke into the market, there were many arguments over color matching.
As the two previous letters state, one can expect some degree of leaching in any seal, and you may find it beneficial to establish a "before seal" color standard slightly darker than the final color.
Phil Johnson
- Madison Heights, Michigan
An addition to Phil's comment.
We had a significant argument with a customer. Finally went to his place and looked. The cause of the difference of opinion was we used cool white fluorescent tubes set high, and they used warm white set lower. It made a big difference in what showed up. Replacing one bank of tubes solved all of the difference of opinion.
James Watts- Navarre, Florida
1998
Although you mentioned that your sealing bath operating with pH 5.8. I do suggest that you better recheck your bath pH control. As far as I concerned, if your bath pH is too low, less than pH 5.0. Fluoride (might be part of the formulation) is too aggressive and at this moment, it would attack the boehmite film and eventually deteriorate the colour. Besides that, I also like to suggest that the sealing water quality have to be checked. If the sealing water quality is too bad, for example, silicate content is too high, more than 10 ppm, the sealing process is not efficient as the result, the color leached off.
Lim Heng Kam- Malaysia
1999
Q, A, or Comment on THIS thread -or- Start a NEW Thread