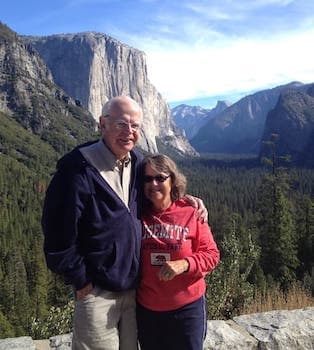
Curated with aloha by
Ted Mooney, P.E. RET
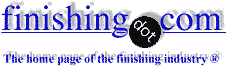
The authoritative public forum
for Metal Finishing 1989-2025
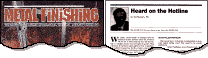
-----
Removal of weld varnish
I would like to remove weld varnish from weldments prior to paint. The traditional methods are abrasive blasting or an acid bath in the pretreatment. Are there any new methods or chemicals that have been proven successful?
Vignes- Deere
1998
We had success removing the weld by products using a needle gun. The gun was air operated, it had steel pins that were moved to and fro at a high rate of speed. The gun made the surface clean and prepared the weld for good paint adhesion.
We also had good luck with a Scotch Brite type material that removed the weld by products and did not have the grinding dust and abrasive issues.
Tyrone Caley- Jefferson City Missouri
1998
There are paste materials that can be brushed on and rinsed off to remove surface oxidation. Most of the products that I have seen are for stainless steel, but these may also work on plain steels. These should be available from you welding distributor. One brand name is Avesta - the same company that makes stainless steel plate materials.
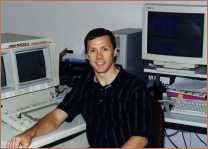
Larry Hanke
Minneapolis, Minnesota
1998
1998
You are right. Not much has been invented lately to remove heat scale associated with welding and other heat related metal fabrication techniques. On the pretreatment side, selecting the correct acid descaler is very important to the success of the pretreatment. It is most important to note that oxide of type will not accept a conversion coating. This will wreak havoc with your paint adhesion.
If you have enough stages to add an acid step to your pretreatment, whether spray or immersion, great. If not, then you may have to consider an off-line descaling operation. The degree of oxide formed will dictate the concentrations, temperatures and times that are necessary to remove it. Also, selection of a correctly inhibited acid and judicious choice of the post processing parameters is necessary to avoid other pitfalls like: rusting and excess metal removal. Sulfuric, Phosphoric, Muriatic? Which one is suitable? Tough call...
You may also need to consider whether hydrogen embrittlement will be a problem for the future use of the part. This will require the use of lesser acids, which can remove scale, but also will not cause H.E.
There are a number of pretreatment companies that can help you make this decision. You'll find them on the finishing.com supplier's page.
Good Luck...
Craig Burkart
- Naperville, Illinois
Q, A, or Comment on THIS thread -or- Start a NEW Thread