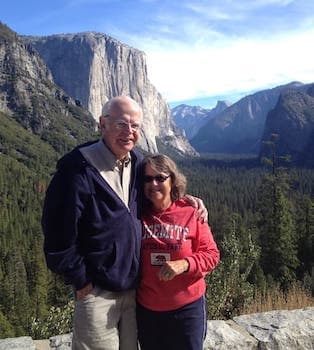
Curated with aloha by
Ted Mooney, P.E. RET
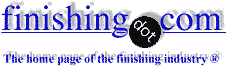
The authoritative public forum
for Metal Finishing 1989-2025
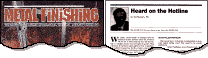
-----
Green staining in Cold sealing of Anodized Aluminum
I am a production engineer from an anodizing plant in Malaysia. Presently, I am facing some problems in sealing quality on the anodized aluminium. For example, greenish color appeared on the 25 micron thickness Natural anodized aluminium after cold sealing process. I had forwarded this problem to my chemical supplier. According to him, if the cobalt content in the cold seal chemical is less, then greenish color will be appeared.
After consulting the chemical supplier, we had added some cobalt into the sealing bath, and the result shown that greenish color disappeared. However, recently we want to replace the existing cold seal chemical to another one, namely product CS2. According to CS2 supplier, their CS2 did not contained any cobalt inside, so I am wondering if I use this CS2 product, does it give a greenish color on to my 25 micron natural anodized aluminium?
I understood that ion sulphate is not good or will affect the sealing quality. However, presently, I am using two type of cold seal chemical, one containing nickel fluoride, and the other one contained nickel sulphate. If you in my situation, which type of cold seal chemical you will use and why ?
In cold sealing process, what parameters play an important role? Solution pH or chemical content? Nickel or fluoride play important role in sealing process.
Thanks
Heng Kam LIM- Malaysia
1998
April 5, 2009
Dear LIM
I am a Chemical Engineer and I have been working with cold sealing for 3 years now in an Anodizing plant down here in Abu Dhabi.
Well you have some interesting questions about the Cold Sealing process...
The ideal method to prevent the greenish color from forming on your Nickel Cold sealed anodic layer is by Cobalt Acetate - and this is usually done by replacing 10% of the nickel by Cobalt which is more then enough to shade the greenish color and the good news is that Cobalt also will aid in Sealing process and acts just like Nickel. And if you are interested to know, the greenish color that is obtained is the color of nickel which indicates that your sealing is OK. Some suppliers are using in there cold sealing formulations some dyes to shade this greenish color, but this is not recommended especially if the Anodized part is to be exposed to sunlight for long periods of time during service - since the dye will fade with time and the greenish color will reappear.
As for the parameters of Cold Sealing - all parameters are important: Fluoride / Nickel / pH / Temperature / Immersion time / Anodizing Parameters / Anodic Layer thickness.
for example at Highest range of fluoride and pH / with minimum Nickel concentration /at high temperatures will give you the shortest immersion times required to obtain a good sealing.
I prefer to work with Nickel Fluoride because it is easier to control and the bath life is longer. As for Nickel sulphate - if you insist on using - then better use Ammonium Fluoride for regulating the fluoride better then other chemicals like potassium fluoride
⇦ this on
Amazon [affil links]
or Sodium Fluoride. It is to note that Qualanod puts restrictions on sodium, potassium and sulphates in the Cold Sealing Bath.
I hope that I was of Assistance to you and Good Luck
aluminium finishing - Abu Dhabi, UAE
Q, A, or Comment on THIS thread -or- Start a NEW Thread