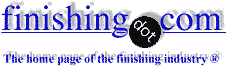
-----
Protection of mild-steel during shipping
I am involved in a manufacturing concern that is producing mild-steel structural components for export. Due to the size and shape of these components, the easiest way to get them into a container for shipping is to bundle several components together with flat surfaces touching. Shipping takes several weeks and includes a crossing of the equator (hot & humid conditions).
The problem is that on arrival at the destination corrosion has taken hold on all the flat surfaces that are in contact with other components. It would appear that capillary action has been responsible to the introduction of moisture to these affected areas.
The current production process involves removing any residual cutting oils with a hot caustic based spray cleaner followed by a two stage rinse (hot town“s water), drying and then a spray coating of a commercially available anti-corrosion coating based on zinc-phosphate and acrylic emulsion resins. The customer removes this coating prior to using the components.
We are considering replacing the caustic cleaner with an iron-phosphate "cleaner/coater" and trying desperately to find a better paint system. The last (expensive) resort would be to include some sort of "Volatile Corrosion Inhibiting Material" in the container. Please comment on these options as well as any other ideas that spring to mind.
- Midrand, Gauteng, South Africa
2003
You might try putting a layer of visqueen plastic (6 mil) between the parts. You might try draping the parts with VPI paper. You might try putting a 1/8 inch separator (wood or metal) between them. Probably the best would be to put trays of desiccant bags in the container. Oiling the part would probably work better and grease still better.
James Watts- Navarre, Florida
2003
2003
One of my specialties is on-site removal of rust inhibitors from mild steel equipment. My experience has been primarily with removing the oil based inhibitors. Some of my customers have tried the light oil and a plastic wrap to lock in an inhibitor rich environment. The results have not been impressive. Same goes for using impregnated paper to protect anything but small parts.
From what I can tell, nothing beats a good old
"Cosmoline" thickened inhibitor. The brands I remove most are: Tectyl (formerly Ashland, now owned by Daubert) EF Houghton (offices worldwide) Coretec based in Minnesota
I have no interest in any of these chemicals. These are just the main players I have known in the past.
Be careful of ultraviolet exposure. Sunlight can bake the inhibitor into the metal and create a bigger problem with the removal.
I design my oil-based removal chemicals to create a non-hazardous waste acceptable for fuels blending. Don't use chlorinated solvents for safety and environmental reasons. I don't like steam cleaner
⇦ on
eBay or
Amazon [affil links]
as they can cause flash rusting.
Good luck on your project.
- Monroe, Louisiana
One more point to consider... be mindful of where your parts come in contact with wood such as the shipping cribbing. We typically see rust only where the metal was resting on wood. I have suggested saturating a thick fabric with inhibitor to act as a gasket between the cribbing and the metal. Just a thought. Hope you can use it.
Todd Turner- Monroe, Louisiana
2003
Q, A, or Comment on THIS thread -or- Start a NEW Thread