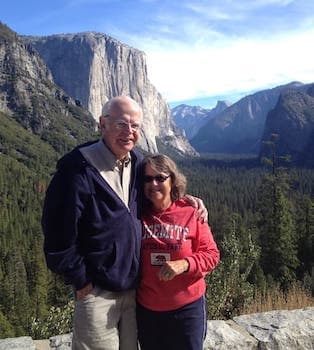
Curated with aloha by
Ted Mooney, P.E. RET
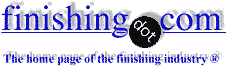
The authoritative public forum
for Metal Finishing 1989-2025
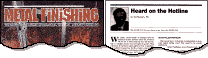
-----
Etching tantalum without embrittlement
2003
My company performs laser micromachining and post-processing services on a variety of metals in flat sheet and tubular form. I am currently working on a device made from commercially pure tantalum. To improve the final product finish after electropolishing, I want to deburr (and remove oxides in the case where an oxygen cover gas is used during the laser processing). After pretty aggressive mechanical deburring, I am trying a variety of chemical etch solutions to achieve this. This leads me to the usual "no-no" solutions for tantalum. The only solution I have thoroughly tested is HF, which in a solution of 25-30% HF in DI H20 descales pretty nicely, but results in catastrophic embrittlement. (Also tried Nitric-HF which overpickles and doesn't descale smoothly, and H2O2-EDTA which is similar...both embrittle a bit but a lot less than HF.)
Does anyone have any suggestions for descaling alternatives that will avoid embrittlement? The next solutions on my list are a nitric-sulfuric blend, 70% sulfuric at 165C (no effect noticed at 1 min), chrome plating solution plus a few percent HF, nitric-HF, nitric-lactic-HF, acetic-nitric-HF, acetic-nitric-sulfuric, red fuming nitric acid, fuming sulfuric acid, sulfur di-(tri-?)oxide, and chlorosulfonic, acetic acid
⇦ this on
eBay
or
Amazon [affil links] -hydrogen peroxide, sodium hydroxide-hydrogen peroxide, peroxide-EDTA. Yuck.
I'm inclined to put off all the HF-containing solutions until last, but that inclination is not based on any reaction analysis of these blends. Should I avoid all hydrogen-containing solutions? Or might some blends of acids somehow prevent this embrittlement? By the way, the mechanical deburring is currently aluminum oxide (which is probably embedded into the surface), but I am planning to attempt steel grit and steel shot, which I can remove readily with HCl before etching the Ta. Maybe I need nitric to dissolve the aluminum oxide
(as noted above, nitric-HF shows less embrittlement, more aggressive etching, overpickled rough surface, less convincing descaling).
To reduce the amount of acid pickling required, I've tried including a KOH bath and a molten sodium nitrate
⇦ this on
Amazon [affil link]
bath to loosen things up, but KOH also embrittles Ta, and neither step seemed to really shorten necessary acid time. If I could get the surface completely descaled without acid pickling, I would, to improve surface finish and reduce the chemical overhead.
Thanks,
- Mountain View, California, USA
Tantalum and Titanium both start with "T". This is what I told a defense contractor that wished to make "detonation shaped projectiles." Good tank killers. They missed the humor. Both are refractory group elements. Keep the HF/HNO3 ratio at least 10:1. We use other means but not HF, which I consider initials for a name not a chemical, is bad stuff!
Jon Quirt- Minneapolis, Minnesota
2003
June 3, 2008
I'm concerned about the use of an oxygen cover gas. Ta should be welding in inert gas as it will oxidize readily at +650-700 °C.
www.rembar.com/Tantalum.htm
The above link has some cleaning recommendations
- Ames, Iowa
Q, A, or Comment on THIS thread -or- Start a NEW Thread