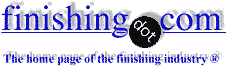
-----
Air Tube Frequent Failure
Hi, We are facing a serious problem in the air compressor unit in utility plant, our compressors are three stage impeller. All the three stages have Air/Water cooler with same in design the air passing in the tube side and the water passes through the shell side, the highest cooler in duty is the 2nd stage of intercooler (the 1st intercooler and 3rd aftercooler didn't face any problem). the problem briefly is that every year we are facing a tube failure in the 2nd stage cooler only, every summer we are plugging five to ten leaking tubes! till now we have changed three tube bundles because of this problems, but the cooler it self is OK! I'm asking, why this phenomena happening in the 2nd stage intercooler(highest duty)? How we can solve the problem? (the whole tube bundle made of Copper) Your feedback on this issue will be highly appreciated Best Regards, Sami ZOBEIR Sabic-IbnRushd
Sami ZOBEIRSABIC IBNRUSHD - Yanbu Industerial City, Western Region, K. Saudi Arabia
2003
2005
Sami ZOBEIR SABIC IBNRUSHD,
To be able to accurately isolate the cause of the tube failures a person would need to be able to both:
1. Inspect the failed tubes and
2. Identify the Mechanical and Operating differences between the three coolers.
Without being able to inspect/view the failed tubes or objectively compare the Mechanical and Operating conditions of the three coolers I have to make a number of "assumptions" that greatly impact the final solution. From the data you have provided I will assume that:
1. Mechanically the three coolers are of similar design and are fabricated of the same materials and have the same approximate sizing/heat exchange capacities.
2. The major operating differences are: Operating pressure and temperature of the air (tube side,) and the flow rate and outlet temperature of the water (shell side).
If this is the case my first thought would be that the tubes are failing due to an EROSION action of some type. As this is the highest heat exchange loading then the water flow rates will be greatest in this exchanger. The tubes being copper will have the lowest resistance to erosion action while the shell is likely fabricated of mild steel.
I hope this helps,
Technical Training and Education - Burnaby, BC Canada
Q, A, or Comment on THIS thread -or- Start a NEW Thread