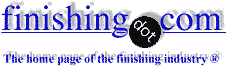
-----
Solutions to Problems blasting stainless steel
Q. I have stainless steel covers 18" x 18" x 4" that get Aluminum Oxide and Glass Bead Blast from a job shop. Over the course of this job, the parts have come back with tiny black spots on them (would not come out with thinner) marks and abrasions. The marks are shiny and seem to be on top of the bead blast. The abrasions almost look like roller marks. After the part is done it gets packed inside of a plastic bag and then in a cardboard box. Anybody have any ideas.
Bob Manzella- Bohemia, New York
2003
![]() |
A. Have you tried different mesh size of glass beads? Have you tried wet blasting? I may suggest you should try those alternatives. Timur Ulucakaluminum extrusions & finishing - Istanbul, Turkey 2003 A. It sounds like you or your subcontractor has a contamination problem. Because blast systems recirculate the abrasive blast media they are subject to contamination from a number of sources. I suspect that is the case here. Even if the subcontractor changes all of the media, it is still possible to encounter the same problem unless the cabinet is cleaned and hoses changed. ![]() AF Kenton retired business owner - Hatboro, Pennsylvania 2003 |
A. The marks you refer to are probably from the blast job shop rolling hence scratching the profile left by the blasting. i.e., they are wearing down the profile making it shinier or darker than the matte finish of the blast. Talk to your job shop about being more careful with handling your parts. This is a common problem.
Jeff chadwick- mississsauga,ontario,canada
2003
A. You need to send your cover to someone who knows to handle the material. After they're blasted they need to be washed or wiped down then wrapped in soft foam, then shrinkwrap with plastic.
Cardboard will scratch stainless if it is slid on it. The shiny marks that look like roller marks could be from the material finish before blasting; if the material was #4 it would have about a 180 grit shiny grain. Which is hard to blast because it would have to be DA sanded to a 80 grit. The best material finish for bead blasting is 2b or mill finish. Also stainless needs to be blasted with clean sand most blast shop do not tell you that because they don't care.The cover might rust if the sand was contaminated with carbon steel (black Spots). Most stainless specialty shops will blast stainless and only stainless in there booths. I only use glass beads unless I need a real rough finish. They should be able to show you blasted samples so you can pick out the finish (grit) you want.
stainless steel welding - Kenosha, Wisconsin
July 30, 2009
Aluminum Impregnation in Stainless Steel? - Glass Media Blasting
Q. Hi,
I produce some parts made of 303 and 304 stainless. These have always been finished in house using glass beads in a media blasting cabinet. The cabinet is only used for the 303 and 304 stainless steel. The volume is now too great for my Harbor Freight blast cabinet so have been asking around locally for a media blaster. The only blaster with a "clean" glass bead cabinet (not used for rusty car parts) does only aluminum for electroplating. My question is: Will the aluminum dust from their parts impregnate my stainless to create an aluminum oxidizing situation on the exterior of the stainless parts similar to what happens if normal steel impregnates the stainless? Of course the aluminum wont be "rusty" looking but still possibly give a hazy oxidized look eventually? I would think the aluminum dust would not have enough mass to impregnate the stainless. However I do not want to take an inexperienced guess and send out a product that may have the appearance of aluminum oxidation later. And for their sake would my stainless contaminate their processes (Anodizing and Alodine)?
Any help would be greatly appreciated.
- Paradise, California
August 24, 2018
Q, A, or Comment on THIS thread -or- Start a NEW Thread