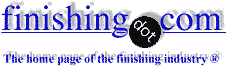
-----
H2S resistance of nickel-plated aluminum
I saw in an earlier post that it was better to have 12% or higher phosphorous content for EN to have the best resistance to corrosion caused by H2S. My plater uses 9% phosphorus content in his EN process and doing a special run would be expensive. Can I get away with using 0.0015" EN with 9% phosphorous content for H2S resistance on Aluminum, or do I need to find another plater that uses more phosphorous?
John Buetow- Boulder, Colorado, USA
2003
Well, that depends on what the cost of a failure or lots of failures is. If you are talking about down hole oil well equipment, you better go for the high P. Consistent 12-13% P is not an easy EN bath to operate compared to a 6-9%. I would want someone with experience with that bath doing it.
James Watts- Navarre, Florida
2003
2003
This is not for down-hole equipment. This is for measuring moisture content of natural gas that may have a high H2S component. I know that we want to have thick plating, as I have had a problem recently where a standard 0.0005" electroless-nickel plating has had a pin-hole in it.
This allowed the moisture in the gas to attack the aluminum underneath and caused it to oxidize. I am not sure what else happened, because there was a black component as well as the standard white Al oxidation. Anyone have any ideas out there what the black stuff could be? Also, does anyone have any recommendations about what to put underneath the electroless Ni to protect the Al from oxidizing?
Or, will just a thicker Ni plating, say 0.002" be sufficient?
Boulder, CO USA
As you found out 0.0005 EN has pin holes. It will cost about twice as much to put on 0.0015 per side, but you should have less than 1% failure. I am not sure that 0.002 is that much better for your application. The black is probably aluminum sulfide, possibly nickel sulfide. As for underneath, there is nothing that is going to help you that is affordable. A good double zincating for adhesion should work with the 0.0015".
James Watts- Navarre, Florida
2003
High phos is less prone to pitting and should be less cathodic to aluminum. If you have bare or exposed aluminum in a corrosive environment the aluminum will become anodic to the nickel.
Todd Osmolski- Charlotte, North Carolina, USA
2003
Q, A, or Comment on THIS thread -or- Start a NEW Thread