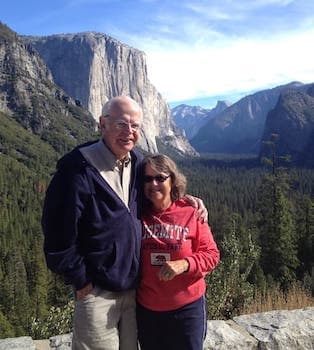
Curated with aloha by
Ted Mooney, P.E. RET
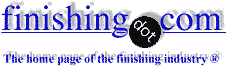
The authoritative public forum
for Metal Finishing 1989-2025
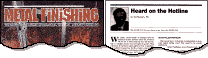
-----
What are the side effects of electroforming nickel sulphamate with insoluble anodes
Q. We are a small family run electroplating job shop. Our company has been handed down through the family for 2 generations and we are trying to set up a nickel sulphamate electroforming solution to coat the inside diameter of aluminum tubes. They are 200mm in length and 50 mm in diameter. We must use insoluble anodes. We are trying to find out the drawbacks of using insoluble anodes and what would be the best way to replenish metal content and control a dropping pH. Should we use Nickel Carbonate? Are we going to effect the sulphamate solution by electroforming this way.
Rob Houghton- Melbourne, Victoria, Australia
2003
A. You are going to have more grief than you can stand if this is a moderately small tank that does not run anything else. pH drops fairly rapidly. The carbonate is a royal pain to get it to dissolve and not turn to a green slime-mud. Then it requires a good filtration before the liquid portion is returned to the tank. Further, you get a breakdown of the sulfamate radical which causes the internal stress to go more and more compressive which you certainly can not stand if you are truly electroforming and not just heavy Ni plate. An option---Make an anode basket with Titanium micromesh. I would use a 1.0" outer diameter possibly less. Contract out making the anode bag covering out of appropriate material, of make it yourself using polyester thread and hand sewing. Talk to the local rep of a brush plating firm and find out who does their covers. Fill the basket with SD nickel pellets. They come in 10K bags. Another option That is less desirable is to use a solid nickel anode such as 400 Ni, again about 1"diameter. This will require a higher chloride content if you can stand it and you will have to watch your internal stress a lot more than with the SD pellets. It will require replacement frequently, so will be more expensive. Plating ID's is never good since you have an anode - cathode ratio of well under 1. This will cause problems. Do not get too carried away with a large anode or you will have threads of the anode cover in the nickel plate at some time- sooner or later. You can get my Email from Ted and send digital pictures. Am willing to pass on other ideas that might help. Free. When it is finalized, send a couple of pictures to Ted for publication. Others might be interested.
James Watts- Navarre, Florida
2003
A. Plating inside the tube of 50 mm diameter is always difficult. You could think of the possibility of electroless nickel plating which is ductile, controllable and feasible by masking off the external surface.
K.V.Phadnis- Mumbai, India
2003
A. James has hit it on the head. You are asking for problems if you use an inert anode in this environment. You will lose control of your pH and additive chemistry. If you start to muck about with the sulphamate bath chemistry, you will lose the advantages of nickel sulphamate as an electroforming solution; i.e., you will increase its stress and ductility.
I appreciate you cannot use an anode inside the tube, as it would need to be only 5/8inch or less in diameter and be precisely located. However, one idea that may appeal to you would be to rig up a centralised inert (plastic?) pipe with graduated holes in it that goes in the tube bore. To ensure centricity, you perhaps could rotate the tube about the vertical axis, whilst keeping this tube stationary. Set up a sulfur depolarised nickel anode as near to the central tube as possible and pump the electrolyte through the anode and into the central tube. Make sure the anodes are very well bagged as you cannot filter the electrolyte between the anode and the inside of the aluminium tube. Also make sure that there is no way the current flux can get from the anode to the aluminium tube other than by the pipework that goes into the middle of it. You may find it beneficial to pump from both ends of the central tube. The graduated holes in the central tube will act as a screen to even out the current distribution. You may also experience induced polarisation, with the outside of the aluminium tube becoming anodic, but this can be avoided by making sure there are no other metal parts in the plating tank.
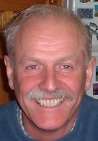
Trevor Crichton
R&D practical scientist
Chesham, Bucks, UK
2003
![]() |
Hi Trevor, - Navarre, Florida 2003 |
Q, A, or Comment on THIS thread -or- Start a NEW Thread