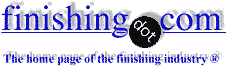
-----
Electrogalvanized vs. hot dip galvanized steel, page

⇦ Tip: Readers want to learn from your situation;
so some readers skip abstract questions.
Q. I want to know what "gZn" and "tZn" mean in surface treatment, thank you.
Jone Shames- hz zhejiang china
April 9, 2021
A. Hi Jone. "tZn" might or might not mean the German acronym for hot dip galvanized as part of, for example, an ISO 4014 nomenclature for a bolt. "GZN" might be a company name, or 'galvanic zinc', or maybe the suffix was left off and it refers to grams of zinc per liter, or grams of zinc per square meter.
In truth, such terms offered out of context are meaningless. Where are you seeing these terms please -- what is the context?
Luck & Regards,
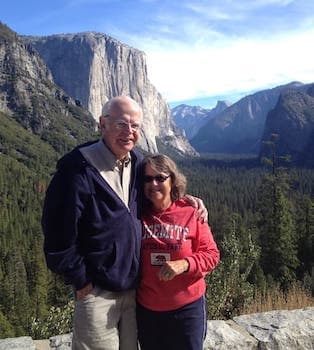
Ted Mooney, P.E. RET
Striving to live Aloha
finishing.com - Pine Beach, New Jersey
April 2021
⇩ Related postings, oldest first ⇩
⇦ Tip: Readers want to learn from your situation;
so some readers skip abstract questions.
Q. I want to know the difference between Electrogalvanized steel and hot dip galvanized steel and process of manufacturing.
Mohammed Adil- Bangalore, Karnataka, India
2003
A. Hi, Mohammed. 'Electrogalvanized' is just another term for 'zinc electroplated'. That means the steel is immersed in an aqueous bath, and electricity is used to move electrons from the anode to the cathode, which induces the zinc anodes to be "oxidized" and dissolve as zinc ions in the aqueous solution, be transported as ions through the solution, and be "reduced" as metal onto the work (the cathode).
In hot dip galvanizing the work is immersed in molten zinc. As it is withdrawn, the zinc cools and forms a coating of zinc on the work (some would say an zinc-iron alloy layer followed by a coating of zinc).
Hot dip galvanized coatings are almost always many times thicker and therefore several times as corrosion resistant. There are some other practical differences in the two coatings for different applications as well. Maybe we can recommend one over the other if you tell us about your proposed application. Thanks!
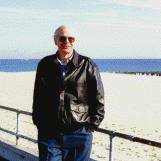
Ted Mooney, P.E.
Striving to live Aloha
finishing.com - Pine Beach, New Jersey
2003
⇦ Tip: Readers want to learn from your situation;
so some readers skip abstract questions.
Q. Dear Sir
I want to know why telecom towers are hot dipped galvanized and not electrogalvanized?
- Mumbai, India
2007
A. Hi, Ashish. Telecom towers are expected to survive many decades in severe environments with minimal or no maintenance. Hot dip galvanized coatings applied "post fab" (on individual components rather than continuously on coil) are far thicker than electrogalvanized (rule of thumb: say 10x as thick) and therefore offer something like 10x the life of electrogalvanized coatings. Good luck.
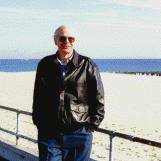
Ted Mooney, P.E.
Striving to live Aloha
finishing.com - Pine Beach, New Jersey
2007
⇦ Tip: Readers want to learn from your situation;
so some readers skip abstract questions.
Q. Can someone please tell the environment in which electro or hot dipped galvanized steels can be used. I mean to say in which environment we prefer electro and in which we prefer hot dipped galvanized steels. Anxiously waiting for reply.
Faheem Anjum- Islamabad, Pakistan
March 5, 2009
A. Hi, Faheem. Electroplated zinc coatings can be smooth and shiny, and preferable for aesthetic reasons, whereas galvanizing may be spangled, or gray and drippy. Zinc electroplating is thin and usually does not cause any problems with fasteners (except very very small ones), whereas galvanized coatings are heavy and will interfere with fastener threads unless they are specially dimensioned to take the coating thickness into account.
But, as mentioned, galvanized coatings are up to 10x as thick and will always greatly outlast zinc electroplating in any environment. Electroplated zinc coatings are rarely adequate for direct outdoor exposure.
Regards,
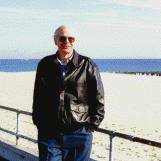
Ted Mooney, P.E.
Striving to live Aloha
finishing.com - Pine Beach, New Jersey
March 9, 2009
⇦ Tip: Readers want to learn from your situation;
so some readers skip abstract questions.
by Kuklik & Kudlacek
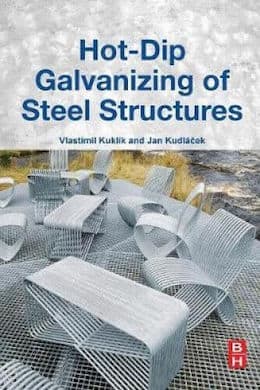
on eBay or Amazon
or AbeBooks
(affil link)
Q. Pertaining to rigid metal conduit threads, what is the difference between hot dipped galvanization and hot galvanizing?
Matt Durning- Chicago, Illinois
April 6, 2009
A. Hi, Matt. As far as I know there is no difference between those two phrases.
Regards,
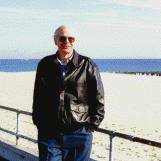
Ted Mooney, P.E.
Striving to live Aloha
finishing.com - Pine Beach, New Jersey
April 2009
⇦ Tip: Readers want to learn from your situation;
so some readers skip abstract questions.
Q. What are the temperatures that a product either electrogalvanised or hot dip galvanised can take or withstand up to? And what are options if it does not survive high temperatures (above 250 °C)?
Dharmil Gopani- Mumbai, India
April 10, 2009
A. Hi, Dharmil. Zinc coatings, whether electrogalvanized or hot dip usually employ chromate conversion coatings to deter white rust. The chromate has a very limited temperature suitability, far less than 250 °C.
There are many platings and coatings, but pure sulfamate nickel plating, with no organic brighteners, is a very good high temperature plating.
What are the components you have in mind, where are they used, and what is expected of them? Thanks!
Regards,
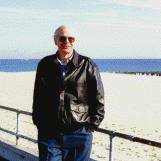
Ted Mooney, P.E.
Striving to live Aloha
finishing.com - Pine Beach, New Jersey
June 7, 2009
Q. Dear Sir,
I have a situation where I need to understand more from you on the Galvanize finishing.
The material is Hangers and Supports to MEP Pipes and Ductwork specified to be GALVANIZED STEEL.
The Contractor has offered ELECTRO GALVANIZED STEEL.
Is ELECTRO GALVANIZED STEEL better then GALVANIZED STEEL?
Please advice.
Thanks and Regards,
consultants - Dubai, United Arab Emirates
A. Hi, Javid. While it can't be claimed that one thing is "better" than another except in response to a detailed list of exactly what qualities the thing should offer, the general thrust of this thread is that electrogalvanized coatings are greatly inferior in corrosion resistance.
Also, I believe that electrogalvanized (zinc electroplated) coatings are susceptible to zinc whiskers and galvanized (hot dipped)coatings are much less susceptible. If this piping is for a hospital or computer room, there may be a problem with using electrogalvanized components due to zinc whisker concerns.
If something is specified to be galvanized steel, that means hot dip galvanized to me ... not obfuscating it with word games of calling zinc electroplated items "electrogalvanized" and then taking the liberty of shortening the term to "galvanized".
Regards,
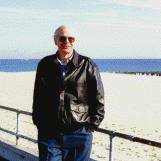
Ted Mooney, P.E.
Striving to live Aloha
finishing.com - Pine Beach, New Jersey
June 8, 2009
June 30, 2009
Q. DEAR SIR,
I AM WORKING IN COMMERCIAL REFRIGERATOR FACTORY AND WE HAVE electrogalvanized steel and hot dip galvanized steel WHICH OF THEM IS BETTER IN PAINTING WITHOUT CHEMICAL TREATMENT (CURING TEMPERATURE IS 200 °C FOR 9 MIN.)
- 6 TH OF OCTOBER, Egypt
A. Hi, Cousin Mohamed. Actually, the pretreatment is usually more important to the durability of a finish than the paint. The paint will not stick without pretreatment. But most zinc plating (electrogalvanizing) will already have a chromate conversion coating on it that comprises pretreatment and is usually paintable.
Please remember that a chain is only as strong as its weakest link. Without proper pretreatment, there is a very weak link adhering (or failing to adhere) the paint to the object, so there is built-in failure.
Which is a better paint base without pretreatment, bare zinc plating or bare hot-dip galvanizing? They both absolutely, completely, suck. Neither is even remotely satisfactory. Good luck.
Regards,
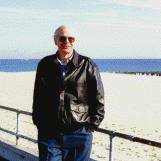
Ted Mooney, P.E.
Striving to live Aloha
finishing.com - Pine Beach, New Jersey
June 30, 2009
Q. Are there any ramifications with regards to CE certification for use of hot-dipped galvanized or electroplated / electrogalvanized?
Bob Simpson- Houston, Texas, U.S.A.
July 13, 2009
A. Hi, Bob. While "any ramifications" is a pretty broad concept, my understanding is that the individual component has to be individually assessed for compliance with CE requirements.
Both hot-dipped and zinc plated components could have RoHS-incompatible hexavalent chromates, and hot-dipped components could have excessive lead, for example.
Regards,
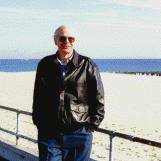
Ted Mooney, P.E.
Striving to live Aloha
finishing.com - Pine Beach, New Jersey
July 13, 2009
⇦ Tip: Readers want to learn from your situation;
so some readers skip abstract questions.
Q. Hi!
I request you to me please refer for what type of applications electrogalvanised steel is used? And some special application where electrogalvanised sheets are preferred over hot dip galvanised steel?
Please do reply. This can give idea to all regarding their differences.
- Delhi, India
July 15, 2009
A. Hi, Anik. This question was answered above several times, so I am repeating myself over & over, but components with zinc electroplating (electrogalvanizing) will have have a thin, shiny, drip-free coating, which is usually considered more aesthetically pleasing. Also, hardware that has been zinc plated normally does not have to be cut to special thread dimensions to allow for the coating thickness as is the case with hot-dip galvanized hardware. Plus, the cost of zinc plating should be significantly lower than the cost of hot dip galvanizing.
But if you are speaking of "Pre" galvanizing / "Pre" zinc plating done on a coil coating line there may be little difference because some sort of wiping is often done on coated coils to reduce the hot dip galvanized thickness. If you can please present your own actual situation, I'm confident we can help you.
Regards,
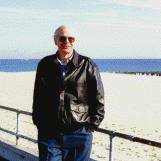
Ted Mooney, P.E.
Striving to live Aloha
finishing.com - Pine Beach, New Jersey
July 20, 2009
Q. Dear Sir,
Is there any standard for thickness of electrogalvanized and hot dip? Product is high strength bolt. Supplier mentioned about 10 µm for electrogalvanized and 55 µm for hot dip but cannot show any standard.
- Ha Noi, Viet Nam
August 2, 2009
A. Hi, Bui. 10 µm = 0.0004", and that would be a reasonable and believable, and fairly heavy, specification for zinc electroplating -- anything from 0.00015" to 0.0006" would be relatively common. As the customer, you get to specify the thickness, and you can choose to specify 10 µm if you wish. Normally you specify a minimum thickness for any spot that can be touched by a 3/4" diameter ball, as well as full coverage (everything must have at least some visible zinc on it).
55 µm = 0.0022" is a perhaps reasonable thickness for hot dip galvanizing, although galvanizing is usually specified by weight rather than thickness. For example, a standard G90 finish would have 0.90 oz of zinc per square foot. And if we estimate the density of zinc at 4.127 oz/in3, you'd be putting 0.90 / 4.127 = 0.218 cu in of zinc on each square foot of surface = .0015 cu in per square inch of surface or .0015" thick. So 55 µm (.0022 in.) would be about half-again as heavy as a G90 finish.
Specs for zinc electroplating include
ASTM B633, but there are others.
Specs for galvanizing include
ASTM A153
, but there are others.
Good luck and regards,
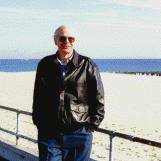
Ted Mooney, P.E.
Striving to live Aloha
finishing.com - Pine Beach, New Jersey
August 3, 2009
September 4, 2009
Q. I am a student in a university in the Philippines. I just want to ask which is advisable to use, the electrogalvanized or the hot-dipped galvanized when it comes to deformed bars to be used in structural construction of buildings and bridges? Good day and thank you!
Jan Michael lafortezastudent - manila, Philippines
by Stephen Yeomans
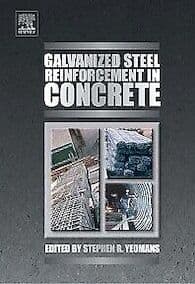
on eBay or Amazon
or AbeBooks
(affil link)
A. Hi, Jan. We've explained the differences in the two coatings above.
Deformed bar (rebar) does not necessarily need zinc coating at all, as plain steel rebar and epoxy coated rebar are also available. But for position papers on hot-dip galvanized bars, please see www.galvanizedrebar.com
I am not sure that electrogalvanized rebar is even available; but if it is, then it would be less expensive but offer less corrosion resistance than hot dipped rebar. Good luck with your studies.
Regards,
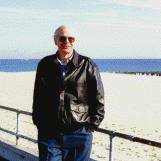
Ted Mooney, P.E.
Striving to live Aloha
finishing.com - Pine Beach, New Jersey
September 4, 2009
⇦ Tip: Readers want to learn from your situation;
so some readers skip abstract questions.
Q. What is the function of electrogalvanized? Can you specify in detail?
What about the function of hot dip galvanized ?
Oil And Gas Trading - Malaysia
A. Hi, Joshua. The principal function of both is corrosion resistance. But the readers are surely dying of boredom by now :-)
-- so please try your best to phrase your question in terms of what has already been said, or explain your own particular situation. Thanks!
Regards,
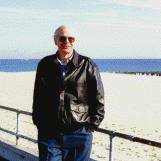
Ted Mooney, P.E.
Striving to live Aloha
finishing.com - Pine Beach, New Jersey
October 2009
Q. Hi,
I have some decking components (sheet metal parts) that I asked for some hot dipped galvanized and the supplier responded that he could only electrogalvanize them. For this kind of application, is electrogalvanize a good enough process.
Thanks
Stephan
industrial design - Quebec,Canada
July 6, 2010
A. Hi, Stephan. Everything is relative, so it's difficult to say whether an undefined electroplating thickness will meet your unstated expectations for an application that I poorly understand :-)
But zinc electroplating is often not acceptable for outdoor exposure, and if this decking includes modern copper-bearing pressure treated wood, which galvanically accelerates the corrosion of zinc and steel, I think it will almost surely prove unsatisfactory.
Regards,
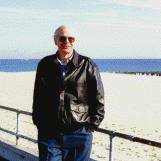
Ted Mooney, P.E.
Striving to live Aloha
finishing.com - Pine Beach, New Jersey
July 6, 2010
Thanks for the response!
So if I have a sheet metal part that helps to hold my structure of the deck that is in aluminum (the main structure is in extruded aluminum), I should use hot dip galvanizing. If the warranty that my client wants to give is 25 years, what grade should I be using?
Best regards
Stephan
- Quebec, Canada
July 7, 2010
A. Hi. I would go with hot dip galvanizing. Generally, a hot dip galvanizer who is "post-galvanizing" fabricated parts is not free to pick a thickness; rather the thickness is simply the result of such factors as the thickness of the part and the amount of silicon in the steel. Find out what thickness he gets on a sample part and start from there. But a 25-year warranty on a mixed metal construction that is subject to galvanic corrosion sounds like a lot, especially if there is high humidity, salt air, or other aggressive aspects of the environment.
Reading between-the-lines, something that may be confusing people is that while finished fabricated parts are often hot dip galvanized, it is also possible to "pre-galvanize" continuous coils of steel. When dealing with those continuous coils, it can be practical to "wipe" the galvanizing down to a lower thickness. So you can buy pre-galvanized sheets or coils with different weights of zinc on them, whereas when galvanizing finished parts we often say the chemistry of the steel controls the thickness of the zinc layer and you don't actually specify the thickness.
Regards,
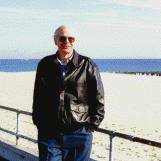
Ted Mooney, P.E.
Striving to live Aloha
finishing.com - Pine Beach, New Jersey
July 7, 2010
Q. Hi Ted,
You already said the difference between HDG & e.g., is the process and also that the corrosion resistance performance is better for HDG than e.g., because the final thickness of Zn. Now, I would like to know if the galvanized method of a material affect the final mechanical properties of a metal sheet. I mean, if I have a commercial steel (sheet metal) and I galvanized it by HDG process and other equal sample by EG...
* The temperature of HDG process could affect the mechanical properties? I mean besides to have different performance on corrosion resistance could I have different mechanical properties because the method of galvanize?
Thanks in advance for your help!
Regards,
Home Appliances - Monterrey, N.L. Mexico
July 7, 2010
A. Hi, Maria. If this is just plain low alloy, non heat-treated steel, and there are no fatigue-loading issues, I don't think either process will have much effect on the mechanical properties.
Ted Mooney, P.E.
Striving to live Aloha
finishing.com - Pine Beach, New Jersey
Q. Hi,
I was wondering what sort of galvanizing coating is best for farm fencing? Hot dipped or electro galvanizing
Cheers,
- Melbourne, Australia
August 17, 2010
A. Hi Matt. How the zinc is applied wouldn't seem to matter very much for farm fencing. It probably just comes down to a case of the thicker the zinc coating the better. But tell us something about your experiences.
Regards,
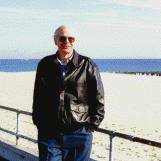
Ted Mooney, P.E.
Striving to live Aloha
finishing.com - Pine Beach, New Jersey
(You're on the 1st page of this topic) Next page >
Q, A, or Comment on THIS thread -or- Start a NEW Thread