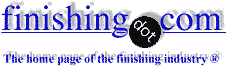
-----
Nitriding, Malcomizing or Kolsterizing 316 Stainless Steel
316 Stainless Shaft Gets Grooved by Radial Seals
Q. I'm an electric motor development engineer working in the marine propulsion space.
I'm trying to reduce the cost of a motor shaft. We currently use Duplex 2205, which creates a significant material cost. We have found ordinary 316 to be too soft to run a radial seal on, with characteristic grooving of the shaft face occurring. I anticipate the run time being at most 500 hours, with a surface speed of around 3.7 m/s.
What coatings or treatments can be made to a stainless steel shaft that will permit a radial seal to run on it, without severely harming its corrosion resistance? I've read that you can nitride stainless steels, but that this will harm it's corrosion resistance. I have no experience with the process, and cannot find info on how severe the reduction is.
The shaft will be used in a marine environment, mostly shielded, but with the possibility of some intermittent salt water contact.
- Auckland, New Zealand
September 24, 2024
A. Hi Josh.
I'm not a metallurgist but I believe that you are correct that nitriding of stainless steel tends to either deplete the chrome, nickel, and other important elements on the surface, thus reducing the corrosion resistance, or fails to reduce them, such that the nitriding tends to not develop correctly and penetrate deeply enough
Nitriding of stainless steel is a tricky process and each type of stainless requires its own tricks. There is reportedly a proprietary low-temperature nitride diffusion well suited to 316SS offed by Bodycote and called Kolsterising which may be an appropriate solution to the problem.
There are, of course, many corrosion resistant coatings which would be applied as an alternative, including the most traditional hard chrome plating, as well as electroless nickel plating. Because the intention is cost savings, you can probably rule out expensive operations like flame spraying, and it would be necessary to know the size of the parts, the production volume, and other logistics to know whether PVD coating would reduce or increase costs. Kolsterizing (highly proprietary) and hard chrome plating (quite generic) would probably be my first two choices for further consideration.
Luck & Regards,
Ted Mooney, P.E. RET
Striving to live Aloha
finishing.com - Pine Beach, New Jersey
⇩ Related postings, oldest first ⇩
Q. My name is Martin Greene, I am a quality specialist for a company which manufactures air and gas compressor valves.
We regularly send a variety of components for a Malcomizing surface treatment to improve wear and fatigue resistance. Malcomizing is similar to gas nitriding but requires an activator to destroy the protective oxide layer on stainless steel; it then hardens the surface through the diffusion of nitrogen. This is an effective process which has worked well on our 17-4, 410 and 420 stainless steel parts.
Our problem is with 316SS material, which we find resists penetration to required depth. This produces a thin brittle shell which chips at the slightest knock, defeating the whole purpose of our efforts to improve the wear on this soft material.
We cannot substitute or harden the material. Any solutions or recommendations are welcome.
- POMPANO BEACH, FLORIDA, USA
2003
A. Your vendor should resolve this problem. Either contact directly, or try posting on Bodycote's Technical Advice Forum. As an alternative, consider their low temperature carbon diffusion process for austenitic stainless steels. They claim that it hardens without forming chromium carbides; thus it does not adversely affect the corrosion resistance.
Ken Vlach [deceased]- Goleta, California

Rest in peace, Ken. Thank you for your hard work which the finishing world, and we at finishing.com, continue to benefit from.
A. Bodycote has a process called Kolsterising that is capable of providing a diffusion hardened surface on Type 316 stainless steel parts. I recommend you contact them for more information.
Toby Padfield- Troy, Michigan USA
Readers may be interested in this related but more active thread:
• Thread 28871, "Hardening 304 & 316 stainless steel"
Q, A, or Comment on THIS thread -or- Start a NEW Thread