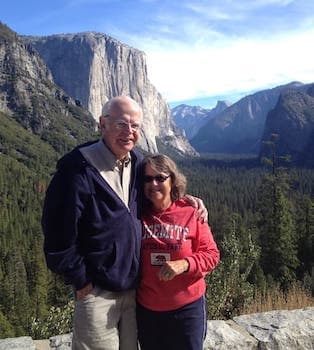
Curated with aloha by
Ted Mooney, P.E. RET
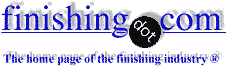
The authoritative public forum
for Metal Finishing 1989-2025
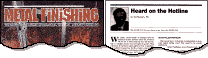
Thread 221/11
The repairing process of roller bearing axle
Q. Based on manual of standards and recommended practice, section G (electro chemical metal deposition process), the repairing process of roller bearing axle journals which are grooved or undersize should be done by nickel selective electroplating. With mention to hardness and thickness of coating, is it possible to do the process by hard chromium electroplating or not? "1- Machining 2- Hard chromium electroplating 3- Machining "
Arezpo SalehiRAD AVARAN SANAT CO. - Tehran
2003
publicly reply to Arezpo Salehi
A. Repair options can depend on the application. Bearing journals used in certain heavy-duty applications are not successfully repaired by hard chrome plating due to the brittleness of the plating. An example is the repair of railroad axles where the journal is subjected to extreme load and vibration which caused premature failure when repaired with chrome. It was found that "electrochemical deposition of metal" using brush plating produced the only acceptable results.
Brush plating also allows the option of locally filling a groove with metal to restore a surface instead of the machining-plating-machining process.
From my experience, if a S&RP manual specifies brush plating it is usually the superior and most economical repair method. If the S&RP specifies "brush plating only", it is because other standard repair methods such as hard chrome playing have fail to produce satisfactory repairs.
- Chatsworth, California, USA
2003
publicly reply to Michael Wisniewski
A. The current most economical method of repairing roller bearing axles is brush plating with Nickel. FYI.
Dan Kahmann- Indep, Missouri
2003
publicly reply to Dan Kahmann
Repairing an embossing roll
Q. I want to fill some dented area by copper electroplating,
It is an embossing roll of steel, which compresses fabric. This will work as a cathode. Copper plate will be acting as an anode.
Should I add some zinc to make it hardened?
- Ahmedabad, Gujarat, India
February 22, 2016
publicly reply to kalicharan sharma
A. Hi Kalicharan. Although you may know more about this subject than me, such that zinc can be practically added to copper plating to harden it, I tend to doubt it.
To my knowledge, the common ways to repair such rolls include welding or brush plating with nickel. If you have access to a certified, highly skilled welder, I think you should ask him what he thinks. If not, I would contact a brush plating specialist to come in and repair this roll by brush plating with nickel. The chances of trial-and-error and OJT solving the problem are probably slim, and I think copper will prove too soft. Good luck.
Regards,
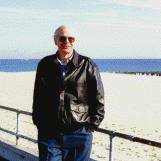
Ted Mooney, P.E.
Striving to live Aloha
finishing.com - Pine Beach, New Jersey
February 2016
publicly reply to Ted Mooney
A. I would strongly suggest welding with an IGBT [insulated gate bipolar transistor] based welding machine wherein beads are very dense, porosity is very minimum, and they can be machined/ground/polished easily. However, use welding rods after confirmation of material grade, you can use pure No. welding rod for the same. Best luck.
Mahendra Gargatti- BELGAUM KARNATAKA India
February 24, 2016
publicly reply to Mahendra Gargatti
Q. Hi,
I need help. I have seen some people filling damaged roll patterns by electroplating. They use white powder not blue copper sulphate. I tried this but Blue copper sulphate
⇦ this on
eBay or
Amazon [affil links] is not even sticking on the rolls.
What can be the reason? Can anybody tell?
- Ahmedabad, Gujarat, India
February 26, 2016
publicly reply to Dipak Patel / kalicharan sharma
Q. Dears,
I have seen some people doing this. The defective spot of roller is covered by insulation media. After that coppersulphate mixture with water is poured in it. Then copper electroplating is performed on it to fill. Final shape is given by filing and making required pattern.
The thing I want to know the why cupric sulphate white fine power is used and not normal blue copper sulphate is used.
Next question is that when I tried this with blue copper sulphate adhesion was so poor that copper layer just peeled out with cloth.
What can be the reason?
Thanks.
- Ahmedabad , Gujarat, India
February 27, 2016
publicly reply to kalicharan sharma
A. Hi kalicharan. copper sulphate pentahydrate (CuSO4.5H20) is blue crystals, but it is possible to drive the water out and get anhydrous copper sulphate (CuSO4), which is a white powder.
I don't know why that was used, but it is significantly more concentrated, so that might possibly be the explanation. I don't think that is what causes the difference in adhesion though -- I think proper cleaning and activation is necessary so that you are not trying to get adhesion to oils or tarnishes. What material is the roll made of?
Regards,
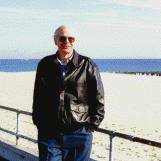
Ted Mooney, P.E.
Striving to live Aloha
finishing.com - Pine Beach, New Jersey
publicly reply to Ted Mooney
adv.
Brush plating equipment, chemicals, and supplies from Gold Touch
Q, A, or Comment on THIS thread -or- Start a NEW Thread