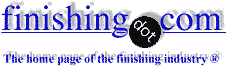
-----
Converting Zinc baths to Zinc-Alloy and Smart Zinc
Currently, I work as the Sales Manager for the southwest territory. My company specializes in zinc, and we have a small cadmium line. We are all familiar with the phase out of cadmium. I want to meet my customers needs, many of which are in the automotive sector. I know that Japan and Europe are already using zinc-tin, and it will only be a matter of time until we see it robustly here. We currently have 14 lines of production. We have both acid chloride and alkaline baths. I want to be able to add other processes at a minimal cost. I would like to know how difficult it would be to convert one or two lines to zinc-tin or zinc-nickel. I know the work is out there, and the market for these alloys will grow.
We are also running one line of something called "smart zinc." It enables us to add about 30% to our barrels, and has potential to increase profit margins if loads are efficient. The smart zinc does not seem to have the same luster, as a chloride bath for example. What information do you have on smart zinc, and converting over to an alloy bath?
- Tucson, Arizona, USA
2003
I believe it's actually called tin-zinc, Mr. Ficken, because the tin content is about 80 percent of the deposit. The only tin-zinc that I had hands-on familiarity with was cyanide-based, although I understand that non-cyanide tin-zinc is available now and works well. Because of the high tin content, lubricity and malleability would be its big advantage over the other alloys, but for the same reason it is more expensive. If your plating lines include "generation tanks", I think you'll find these trials and conversions easier to implement than if they don't.
"Smart zinc", although I am not familiar with it, sounds like a proprietary name. We don't like to discuss proprietaries here for a number of reasons including the impracticality of determining a responder's vested interests, given the relative anonymity of the Internet. High praise can come from a shill pretending to be a satisfied customer, and condemnation can come from a disgruntled employee or a competitor pretending to be a dissatisfied customer. Proprietaries are probably better discussed over dinner at an AESF or NAMF meeting where you can actually see who's doing the talking :-)
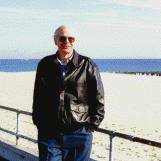
Ted Mooney, P.E.
Striving to live Aloha
finishing.com - Pine Beach, New Jersey
2003
A. Mr Ficken
The trend is towards alloy coats. You possibly have an idea of client need and can look at various options.
- Zinc Tin is one. It's not cheap but works well.
Alkaline Zinc Iron is something the US has not looked at carefully, though it's very popular in Japan. It's the most economical route to high SST hours up to 500. Not recommended for engine components due to poor temperature resistance.
- Alkaline Zinc Nickel is popular in the UK: most expensive route to a 1000 Hour SST.
The Smart Zinc seems to be a high load product that can churn out more tonnage at the cost of finish quality.
You might do well to look at alternative Non Boric based chloride zinc systems that contain less than 30 GPL of Ammonium Chloride and deliver much more consistent quality in 80 percent of the time a Boric Potassium system can.
The ammonia
⇦ on
eBay or
Amazon [affil links] in the waste stream is negligible and controllable, and can be treated judiciously to meet EPA norms.
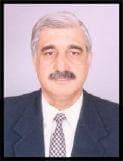
Asif Nurie [deceased] [deceased]
- New Delhi, India
With deep sadness we acknowledge the passing of Asif on Jan 24, 2016

Q, A, or Comment on THIS thread -or- Start a NEW Thread