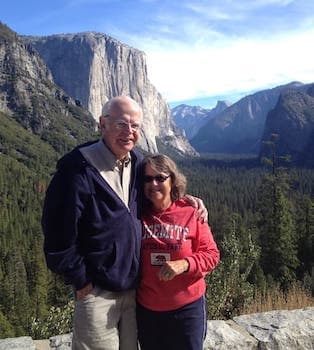
Curated with aloha by
Ted Mooney, P.E. RET
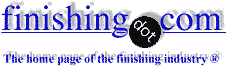
The authoritative public forum
for Metal Finishing 1989-2025
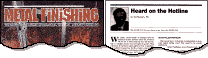
-----
How soon after processing must chromate conversion coated surfaces be painted/powder coated

Quickstart:
Aluminum is often 'chromate conversion coated' as a corrosion resistant final finish or as a pretreatment for painting or powder coating. The process actually involves many steps, usually including alkaline cleaning, etching, deox/desmut, the chromate conversion step per se, and water rinses between each step.
MIL-C-5541 / MIL-DTL-5541 / MIL PRF-5541 is the most commonly cited spec. "Alodine" and "Iridite" are trade names. "Chem film" is a slang term for the process.
Q. Can you tell me how long parts can be stored before they will need to be reactivated?
D Sabol- Lexington, Kentucky
February 28, 2022
A. Hi D. We added your question to a thread where it has been discussed in interesting detail. If this is critical aerospace spec work, the answer is somewhere between 12 and 72 hours as mentioned by Brian and Milt. Even though chromate finishes don't necessarily soon go bad as argued by Robert, the answer seems to be that your question may not be well phrased, because the correct answer seems to be that you should not put chromate conversion coated parts into storage for later painting/powder coating.
Luck & Regards,
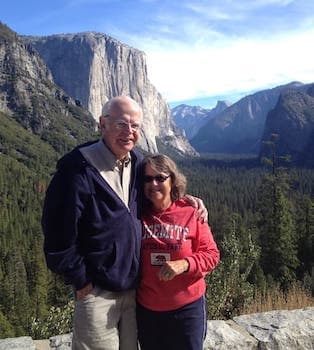
Ted Mooney, P.E. RET
Striving to live Aloha
finishing.com - Pine Beach, New Jersey
March 2022
⇩ Related postings, oldest first ⇩
Q. I have conversion coated surfaces that I would like to powdercoat. The conversion coating has been on for 6-12 months. Does this have to be removed to get good adhesion to the aged surface? Will I still get good corrosion protection?
AJ Nielsen- Duluth, Minnesota, USA
2003
A. Six months room temperature low humidity shelf life should not matter provided you can remove the organic soils that may have settled on the surface.
More important, especially with powder coat, is that the chromate conversion coating be very thin. If the chromate is too thick the coating will sheer and the paint peel right off. Also, if the coating is thick, the high temperature of curing powder paint will crumble the chromate and, again, the paint will peel.
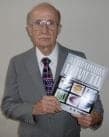
Robert H Probert
Robert H Probert Technical Services

Garner, North Carolina
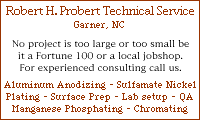
2003
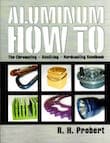
Aluminum How-To
"Chromating - Anodizing - Hardcoating"
by Robert Probert
Also available in Spanish
You'll love this book. Finishing.com has sold almost a thousand copies without a single return request :-)
Q. I have some parts that I want to powder coat in some areas and Alodine in others. I need the Alodine for corrosion resistance and conductivity and the powder coat for corrosion resistance and aesthetics. How should I go about getting this combination? Can the powder coating be subjected to the processes required for Alodine coating? If so, how does this affect the powder if at all? Also, if a part is Alodine coated, then powder coated, and the re. Alodined is the second Alodine coating as good as the first? What kind of dimensional change could I expect from two coatings of Alodine? Any information will be much appreciated.
Thanks,
- Santa Rosa, California, USA
2003
Multiple threads merged: please forgive chronology errors and repetition 🙂
After MIL-C-5541 coating, what is the time window for recoating?
Q. I have 2 questions: I am preparing to receive some aluminum panels that have been pretreated with MIL-C-5541. My job is to then primer them with a chromated epoxy polyamide primer.
My 1st question is: Is there a "time" window in which I would need to have my primer applied to the parts before I would need to "prep" the parts again. I obviously do not want to sand/scuff the parts after the MIL-C-5541 has been done.
The 2nd question is: If there is a "time" window, and I am outside of it, what type of procedure is recommended to "prep" the parts for primer without compromising the pretreatment coating.
Thank You,
industrial coatings - Green Bay, Wisconsin
2005
A. Bob,
The ideal time window for priming after MIL-C-5541 coating is generally considered to be within 16 hours. Most OEMs allow for an extension in time up to 72 hours, if supported by some sort of test procedure to prove out the primer adhesion. This differs between OEMs so you will either have to refer back to the OEM or the OEM specification.
If you miss the target time, the only way I know to activate the surface is to strip chromate film and re-chromate.
aerospace - Yeovil, Somerset, UK
2005
A. There are a couple of ways of answering this and you've already got one reply. In the US from my experience, the maximum delay between pretreatment and organic coating, be it phosphate, glass beading or chem film, is 24 hours. This is the number in many mil specs for organic finishing and, I believe, in the Nadcap checklist. Also, there are certainly many aerospace primes with much tighter limits than this - as short as 8 hours (i.e. one shift). When you're talking about adhesive priming, the later 8 hour limit is the standard. The other response, less pragmatic approach would be, how likely are the parts to get dirty between chromating and painting. If you're a job shop, too much can happen in 72 hours to assure that the parts will stay clean during that dwell time. Also, keep in mind that chromate films tend to heal over the course of their first 24 hours so the film one would coat in say 2 hours is not the coating it would be in say 12 or 24 or 48 hours. If there is no prescriptive limit in the specification you're working to, I would simply set up a DOE and test 1 hour, 8 hours, 24 hours and 72 hours followed by the wet tape test ( X-scribe over primed panel soaked in water for 24-hours ) and see what the impact on adhesion is. If anyone ever challenged you, you'd have objective evidence to back up on for establishing a realistic limit for your particular shop and coating system.
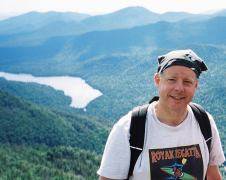
Milt Stevenson, Jr.
Syracuse, New York
2005
Q, A, or Comment on THIS thread -or- Start a NEW Thread