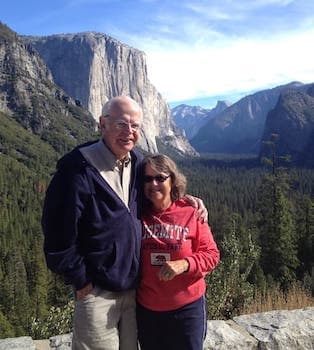
Curated with aloha by
Ted Mooney, P.E. RET
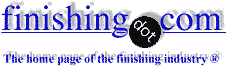
The authoritative public forum
for Metal Finishing 1989-2025
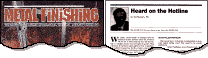
-----
Cr6 Emissions from Conversion Coating tank process
I am working on an emissions evaluation for a chromic acid chemical conversion coating tank which uses a well known product containing chromic acid. The process tank is 6 ft long, 3 ft wide, and 3 feet deep, unheated. The tank is currently air mixed (highly agitated surface). I would like to know if anyone has any info concerning the evolution of CR6 emissions from the surface of such a tank (lbs. Cr6/sq.ft./hr), and what decrease in emissions would be expected if the tank were to be pump mixed, i.e., a quiescent surface. Cr6 in the tank solution is calculated to be approximately 0.02275 lbs Cr6/gallon of solution. approx. tank volume of solution is 404 gals. The tank is not covered.
Richard B. Booth- Corona, California, USA
2003
2003
Hello,
I am working on a similar problem. I have found an emission factor from the US AP 42 of 3.1e4 mg/day for a tank 20ft2 and with an air agitation flowrate of 10 CFM and 24 hours of operation.
I am currently looking for emission rates for not air agitation tanks of chromate conversion baths. If I had the vapour pressure for chromic acid in concentration it could be figured out using EPA equation from EPA-560/4-888-002.
- Waterloo, Ontario, Canada
What I'd like to see in this regard is the results from an exposure badge worn by an employee. I'm reasonably confident that exposure to chromic acid fumes or mists from a chromate conversion coating tank is zero to the limits of detection; but 'reasonably confident' and 'sure' are of course not the same thing.
Chromate is considered a class "A" chemical requiring ventilation regardless of concentration but I've never detected the smell of chrome from a chromate tank, and never seen even the slightest sign of the yellow dust and dark amber stains so often associated with chrome plating tanks.
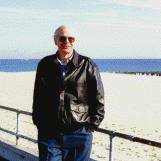
Ted Mooney, P.E.
Striving to live Aloha
finishing.com - Pine Beach, New Jersey
2003
2003
Hi Richard and also Joel,
In my absymal ignorance of your operations, i.e.. not true plating operations generating 'fumes' etc., nevertheless I would assume that a) your are handling a nasty carcinogenic and b) if agitating, ah, oh dear, you most definitely WILL be generating droplets.
Why don't you PLEASE exhaust the system ... use mild steel and a M.S. fan ... and if you feel that you are going to capture spray etc. carry-over from your tanks, at least protect the environment. How to do this? Simple. Use a l2 micron horizontal blade type mist eliminator ... and any captured 'effluent' can be vectored back to the tank.
For a tank 6' x 3' = l8 sq.ft, I'd opt for max. l00 to 75 cfm/sq.ft versus 250 cfm for a proper chrome tank ventilation. By the way, the VAST majority of plating 'fumes and gases' do not exist. They consist instead of invisible small droplets of liquid ... and these you can capture with impunity. Go to the finishing.com library, if you wish, for some further info on materials etc for chrome ventilation systems.
To repeat, if you have any doubts, then please ventilate!
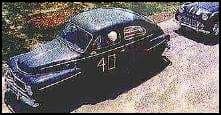
Freeman Newton [deceased]
(It is our sad duty to advise that Freeman passed away
April 21, 2012. R.I.P. old friend).
After having been around literally several hundreds of hard and decorative chrome, chrome anodizing, chrome additive and chromating processes (zinc, Alodine, etc.) I completely concur with Ted (I'm sure Ted has seen many more than I). Having designed many ventilation systems for chrome exhaust and abatement I can only offer this, a far greater amount of NOX, SOX and particulate has been emitted to the general population from power plants due to the energy requirements of exhausting chromate conversion processes than what can possibly be emitted from chromate conversion tanks as a whole.
Sorry I cannot provide an answer to your question but I believe you will need to strike luck in the private sector with a company whom has performed analytical testing.
- Hickory, North Carolina
2003
The amount of entrained chrome will be highly dependent on the amount of air used to agitate and the size of the air bubble as it breaks the surface. The variance from plant to plant is large, if not huge, so valid calculations would require at least a ± 50 %. So why calculate. Some state air quality folks have mandatory formulas. If an exhaust system is sized IAW standard ventilation practices and has a fume scrubber (which is required by most states), there is no problem. PS for chem film, a pumped agitation system is not equal to the results of a properly designed and operated air sparging system. Tried both.
James Watts- Navarre, Florida
2003
Hello Contributors,
The following may be of use. Some 6 years ago I organized some air sampling at a hard chrome plating establishment. The shop had one large tank with a surface area of 5.5 square meters (nearly 60 square feet), and two smaller tanks, about 1.5 to 2 square meters each, and air was used for circulation. Fume suppressant was present in all the tanks, and while there were no obvious signs of vagrant fume one could see the staining on the roof and crane beams, and the skylights were looking brown. Two employees were fitted with samplers and wore them for about 8 hours while they went about their work. The men indicated that the actual electroplating workload on the day of the testing was approximately 50% of normal. The filters were tested and the maximum personal exposure to Cr6 was 0.002 mg/m3, and to Cr metal (from polishing etc) was 0.006 mg/m3. These levels being considerably less than the recommended limits of 0.05 and 0.5 mg/m3 respectively.
- Melbourne, Australia
2003
Q, A, or Comment on THIS thread -or- Start a NEW Thread