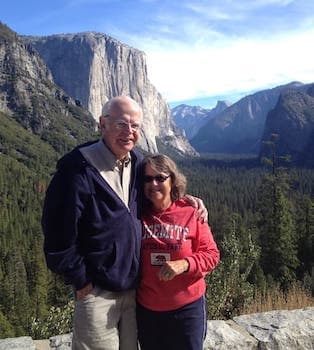
Curated with aloha by
Ted Mooney, P.E. RET
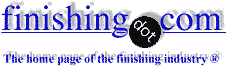
The authoritative public forum
for Metal Finishing 1989-2025
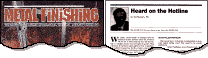
-----
Porosity and die castings
Q. I hope you have time and ambition. It is a toughy. I have tried for 30 hours to solve it and many others have too.
It is a part that all of you have had contact with in one form or another. I work for a auto / military / commercial manufacturing company. I have an issue below that I have not been able to get a clear answer on when I have talked with individuals from NADCA, Casting companies, Inspection equipment companies, individuals that produce the Machinery's Handbook, individuals from the North American Die casters institute, my customer or anyone else for that matter. I have looked at multiple standards and other text but only fall short. I have spent about 30 hours in trying to come up with the answers and feel that if there is not one, there needs to be some guidelines set. The part in question is used in an automotive situation. It is in contact with gasoline, rubber and aluminum. That is about all I can share about the item. sorry
I have a cast part that requires machining. There is a surface finish call out for casted area that has machining preformed but there is not a call out for porosity. Does there need to be a porosity call out or does the surface finish of a machined casted part include porosity in the surface finish requirement? My big issue is that the part is called out as a casting without a porosity spec, but yet has a surface finish call out on a machined surface that has very small porosity not meeting the surface finish spec. I am looking for some type of recognized standard as a reference as to what call out supersedes what.
Thank you,
- Lakeville , Minnesota, USA
2003
A. As I understand your situation, the problem is not with the drawing specification/requirement, so much as it is a problem with the manufacturing process meeting it. IF your drawing clearly indicates that the part/component surface has a minimum requirement for surface roughness, then task 1 has been accomplished. IF the requirement is such that the surface roughness requirement can only be attained by machining (face milling, etc.), then perhaps task 2 needs to be addressed. My definition of task 2 is "the creation of sufficient detail on the drawing such that the part can be suitably manufactured by the die casting process".
The only reason to specify a porosity requirement is so that a casting process with poor control of porosity can be used. If this is necessary, then by all means create a requirement, but there is no inherent rule or specification that just because a part has been agreed upon to be manufactured by the die casting process that any potential part requirement (dimensional, strength, pressure tightness, etc.) that may be compromised by porosity is now exempt. Die casting companies frequently try to do this, but it is not true.
There are a number of ways to rectify this situation. The first is obviously place a requirement on the drawing for maximum porosity. Another is to use a vacuum die casting process, which substantially reduces or eliminates porosity. Gibbs Die Casting in the US is one casting vendor that uses this process. Resin impregnation of the casting may be another option to consider-- low viscosity resins infiltrate the casting porosity and seal it. You can obtain more information from the Loctite website. And lastly, your current die casting supplier should be investigating alternative gating methods, overflow positions, filling parameters (metal velocity/pressure profiles), etc. in order to reduce or eliminate the porosity in the affected areas.
I hope this was somewhat helpful. Feel free to reply if you want to discuss further.
- Troy, Michigan
2003
A. I think what Kevin is implying is that regardless of the surface finish on a diecasting as cast, once you start machining it you cut through the 'skin' of the casting and are left with a very different kind of surface. I'm not sure, but I don't think your response was about that, Toby.
Are you saying, Kevin, that regardless of the machining method you use, you cannot get the porous innards of this casting to meet the surface roughness spec the drawing specifies?
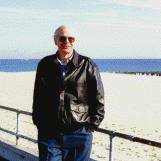
Ted Mooney, P.E.
Striving to live Aloha
finishing.com - Pine Beach, New Jersey
2003
Q. My situation is similar to Kevin's. We have steel and grey iron castings that we machine.
I have a casting specification that calls out allowable porosity on the cast surface and a machine surface finish call out per the drawing.
There is porosity being uncovered on the machined surfaces. I am trying to discover if there are any specs that addresses the issue of allowable porosity after machining. More specifically, specs which may be used justify machine surface porosity or a spec which discusses a repair procedure such as weld repair.
Thanks,
part fabrication - Sealy, Texas
2004
A. Kevin,
Some applications require machined surfaces to be free of holes so as not not to corrupt seals.
Some companies have porosity on surface standards for items going into gas field applications.
I suggest that you give the customer a better casting by eliminating the porosity, by using high vacuum technique.
- Milton Keynes, Buckinghamshire, England
2004
My situation is the same as Kevin's
How about your solutions?
We are working on gate system, but the worst thing is the casting station lost pressure during operation sometimes.....
industrial supply- Shanghai, China
2007
A. Kevin's issue(s) are very common and ALWAYS a headache. I've been in engineering & manufacturing for many years. The only way I have found to effectively remedy exposing porosity when machining is to include a specification for the casting and including a class and grade...and that spec needs to refer to ASTM E155 which are radiograph (X-ray) reference slides depicting the amount of porosity that can be tolerated. It's expensive because you can add the price of the NDT right to the price of the casting. Once you get a reliable process down, remove the requirement for the radiographing (only). Sorry I am at my residence so I do not have all of the specifications in front of me. Hot Isostatic Pressing is a nice way to reduce included porosity, but it's expensive as well. You need to ask yourself: "How valuable are these castings?". Another trick that is sometimes harder to do than it sounds is to design the product so that a little allowable porosity will not affect the function of the design. That can take considerable work. The best way, in any case, is to hold your foundry's feet to the fire, and also be willing to revise the design to accommodate the process.
David Vranson- Valencia, California, USA
May 22, 2008
A. Kevin,
I might be a little out of my element here, however I think that my 2 cents might help.
If I understand correctly, you are trying to find out which standard supersedes the other, porosity of cast surface vs surface quality of machined surface. If this is true, than I think your issue is more of a configuration management one than anything. In my experience, this problem is solved by separating the casting and machining drawings. The casting drawing includes your draft angles, ejector pin locations, and porosity spec. The machining drawing calls on the casted part as it's material requirement, in effect creating a one line BOM. The secondary operations, with applicable tolerances and surface quality specifications are included on this drawing.
I hope this helps.
- Maspeth, New York
June 18, 2008
A. Kevin,
I found this after a search as I have the same problem. we have many high volume parts that are machined castings with tight tolerance bores and they have high finish specs on them.
Now if the machinist sets up the machining operation and I give him high quality steel plate or bar he meets the finish all the time, but if I give him a casting he might not on some percentage. let us say we are trying to achieve a very low PPM rate. the castings in some cases have just enough fog that they do not meet the finish spec when the inspector checks.
Now all castings are porous they are just relative and to a degree. there are ASTM specs with grades or quality levels. and they involve cost.
So you can meet the intended casting quality level but not meet the machining finish spec on a percentage.
That is your problem and mine Kevin.
I do not know the solution except to change the design and allow for sleeves out of mill material that can repeat over and over to meet the spec.
so I think it is a design issue. either allow the casting flaws to the casting spec or redesign with sleeves.
Jess
- norwalk, California
Q. I came across in certain technical paper and die caster website that the vacuum high pressure die casting process can achieve "Zero porosity" with control of process parameters and good use of tools. Can "Zero porosity" be achieved in from die casting in reality?
YS Ooi- Penang, Malaysia
November 6, 2015
Q, A, or Comment on THIS thread -or- Start a NEW Thread